Your Ultimate Guide to Sourcing Turquoise Backpack
Guide to Turquoise Backpack
- Introduction: Navigating the Global Market for turquoise backpack
- Understanding turquoise backpack Types and Variations
- Key Industrial Applications of turquoise backpack
- Strategic Material Selection Guide for turquoise backpack
- In-depth Look: Manufacturing Processes and Quality Assurance for turquoise backpack
- Comprehensive Cost and Pricing Analysis for turquoise backpack Sourcing
- Spotlight on Potential turquoise backpack Manufacturers and Suppliers
- Essential Technical Properties and Trade Terminology for turquoise backpack
- Navigating Market Dynamics, Sourcing Trends, and Sustainability in the turquoise backpack Sector
- Frequently Asked Questions (FAQs) for B2B Buyers of turquoise backpack
- Strategic Sourcing Conclusion and Outlook for turquoise backpack
Introduction: Navigating the Global Market for turquoise backpack
Navigating the global market for turquoise backpacks offers international B2B buyers a unique opportunity to capitalize on a vibrant and trendy product that appeals to diverse consumer bases. The turquoise color, symbolizing tranquility and creativity, resonates well across various demographics, making it an attractive option for retailers looking to enhance their product offerings. As the global bags and luggage market is projected to reach $85 billion by 2030, understanding the nuances of sourcing turquoise backpacks becomes crucial for competitive advantage.
This comprehensive guide will delve into critical aspects of the turquoise backpack market, including the various types available, suitable materials, manufacturing processes, and quality control measures. Buyers will gain insights into identifying reliable suppliers and understanding cost structures, enabling them to make informed sourcing decisions. Furthermore, the guide will address market trends and consumer preferences, essential for tailoring product lines to meet regional demands.
For B2B buyers in Africa, South America, the Middle East, and Europe—particularly in countries like France and Egypt—this guide will serve as a valuable resource. It empowers stakeholders to navigate the complexities of international sourcing, ensuring they are equipped to meet the evolving needs of their markets while maintaining quality and compliance with social and environmental standards. Ultimately, this knowledge will enhance strategic sourcing efforts and drive successful business outcomes in the turquoise backpack segment.
Understanding turquoise backpack Types and Variations
Type Name | Key Distinguishing Features | Primary B2B Applications | Brief Pros & Cons for Buyers |
---|---|---|---|
Daypack | Compact size, typically 15-30 liters, lightweight | Outdoor activities, day trips | Pros: Versatile, easy to carry. Cons: Limited storage for longer trips. |
Travel Backpack | Larger capacity, often with multiple compartments | Travel, business trips | Pros: Ample space, organizational features. Cons: Can be bulky to carry. |
Technical Backpack | Designed for specific activities (e.g., hiking, climbing) | Sports, outdoor gear retailers | Pros: Specialized features enhance performance. Cons: Higher price point. |
Laptop Backpack | Padded compartment for laptops, often with USB ports | Tech companies, educational institutions | Pros: Protects devices, convenient for commuting. Cons: Less space for other items. |
Eco-Friendly Backpack | Made from sustainable materials, often stylish | Eco-conscious brands, fashion retailers | Pros: Appeals to environmentally aware consumers. Cons: May have higher costs. |
Daypack
Daypacks are ideal for short excursions, typically ranging from 15 to 30 liters in capacity. These backpacks are lightweight and easy to carry, making them suitable for outdoor activities such as hiking, picnics, or day trips. When considering B2B purchases, businesses should focus on durability and comfort features, as well as the potential for branding opportunities through custom designs.
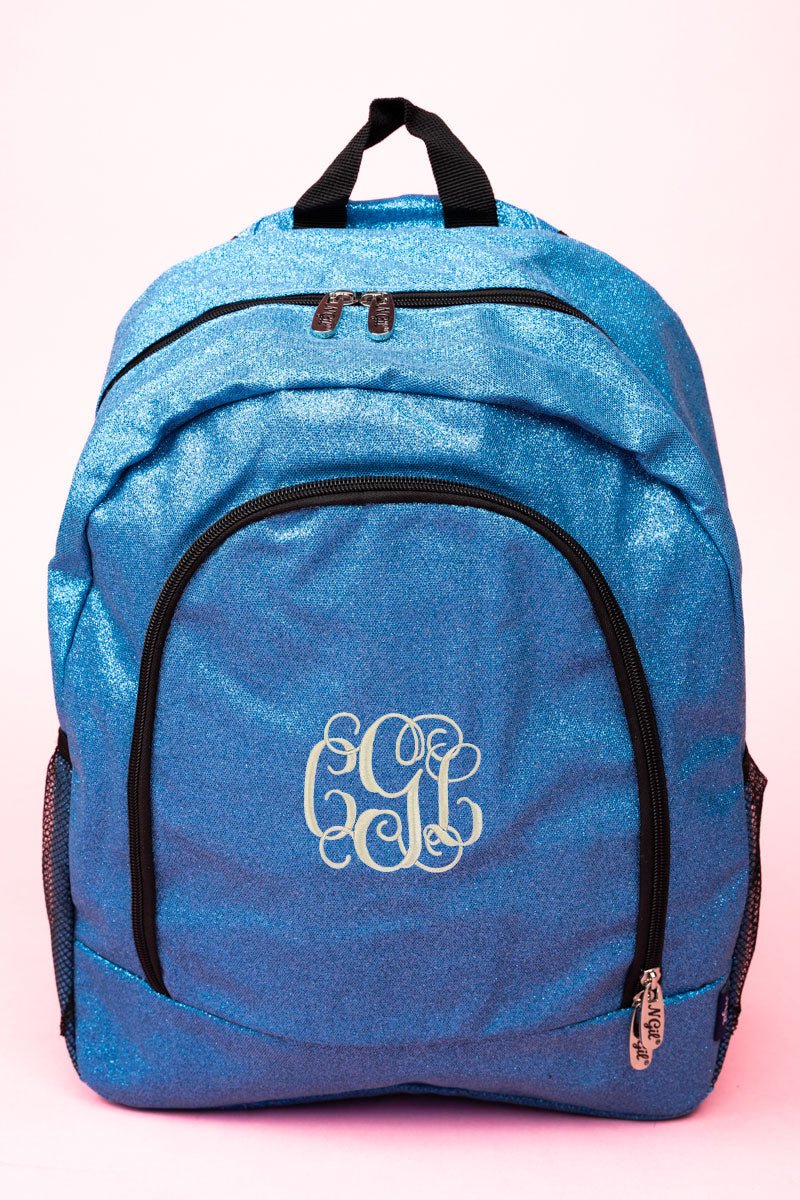
Illustrative Image (Source: Google Search)
Travel Backpack
Travel backpacks are designed for longer journeys and often feature multiple compartments for organization. They are particularly popular among business travelers and tourists. B2B buyers should prioritize backpacks with durable materials and good warranty policies, as these will enhance the longevity and reliability of the product. Additionally, assessing the backpack’s weight and carrying comfort can influence purchasing decisions.
Technical Backpack
Technical backpacks cater to specific outdoor activities, such as hiking, climbing, or skiing. They often include features like hydration reservoirs, gear loops, and reinforced areas for added durability. Companies in the sports and outdoor sectors should consider the performance-enhancing features of these backpacks, balancing cost with functionality to meet the needs of their target market.
Laptop Backpack
Laptop backpacks are designed with a padded compartment to protect electronic devices, making them essential for tech companies and educational institutions. Many models also include USB charging ports for convenience. B2B buyers should evaluate the quality of padding and the overall design to ensure the safety of devices, while also considering additional storage for everyday items.
Eco-Friendly Backpack
Eco-friendly backpacks are crafted from sustainable materials, appealing to brands that prioritize environmental responsibility. These backpacks can be marketed effectively to eco-conscious consumers. B2B buyers should assess the sourcing of materials, production processes, and potential certifications that could enhance brand reputation. However, it’s important to consider that eco-friendly options may come at a higher price point, which could affect profit margins.
Related Video: What Makes Large Language Models Expensive?
Key Industrial Applications of turquoise backpack
Industry/Sector | Specific Application of turquoise backpack | Value/Benefit for the Business | Key Sourcing Considerations for this Application |
---|---|---|---|
Education | School backpacks for students | Enhances student engagement and brand loyalty | Quality of materials, compliance with safety standards |
Outdoor Recreation | Hiking and adventure gear | Durability and functionality in rugged conditions | Weather resistance, weight, and ergonomic design |
Corporate Gifting | Promotional backpacks for brand visibility | Increases brand awareness and customer loyalty | Customization options, lead times, and pricing flexibility |
Travel and Tourism | Travel backpacks for tourists | Convenience and organization for travelers | Size, weight, and features like anti-theft mechanisms |
Retail | Fashionable backpacks for retail outlets | Attracts diverse customer demographics | Trend alignment, seasonal designs, and competitive pricing |
Education
In the education sector, turquoise backpacks serve as essential items for students, helping to facilitate a better learning experience. These backpacks not only provide ample storage for books and supplies but also contribute to a student’s identity through color choice. For international B2B buyers, particularly in regions like Africa and South America, it is critical to source backpacks that meet safety standards, are made from durable materials, and offer customization options for schools to promote their branding.
Outdoor Recreation
Turquoise backpacks are increasingly popular in the outdoor recreation industry, especially among hiking and adventure enthusiasts. These backpacks are designed for durability, comfort, and functionality, making them ideal for rugged environments. Buyers in the Middle East and Europe should prioritize sourcing products that feature weather-resistant materials and ergonomic designs to ensure customer satisfaction and product longevity. Additionally, understanding local preferences for size and style can enhance market penetration.
Corporate Gifting
In the corporate sector, turquoise backpacks can be utilized as promotional items, enhancing brand visibility at events and trade shows. Companies can customize these backpacks with their logos, making them effective marketing tools that improve customer loyalty and engagement. B2B buyers should consider sourcing backpacks that offer a range of customization options, competitive pricing, and timely delivery to align with promotional campaigns. Compliance with quality standards is also essential to maintain brand reputation.
Travel and Tourism
The travel and tourism industry benefits significantly from turquoise backpacks, which provide travelers with a convenient and organized way to carry their belongings. These backpacks often include features like anti-theft mechanisms and compartments for electronics, appealing to security-conscious travelers. Buyers from Europe and Africa should focus on sourcing lightweight designs that cater to the needs of tourists while ensuring that the materials used are both durable and easy to clean.
Retail
In retail, turquoise backpacks can attract a diverse customer base, appealing to both youth and adults due to their trendy color and design. Retailers can leverage these backpacks to create seasonal promotions or themed collections. For B2B buyers, it is crucial to source products that align with current fashion trends, offer competitive pricing, and provide flexibility in order quantities. Understanding local market dynamics and customer preferences will be key to successful sales strategies.
Related Video: 25 Amazing Uses for IBC Totes
Strategic Material Selection Guide for turquoise backpack
When selecting materials for turquoise backpacks, B2B buyers must consider various factors that influence product performance, cost, and market compliance. Below is an analysis of four common materials used in backpack manufacturing, focusing on their properties, advantages, disadvantages, and implications for international buyers.
1. Polyester
Key Properties:
Polyester is a synthetic fabric known for its durability and resistance to stretching and shrinking. It has a temperature rating that allows it to perform well in various climates, making it suitable for outdoor use.
Pros & Cons:
– Advantages: Polyester is lightweight, water-resistant, and dries quickly, making it ideal for backpacks exposed to the elements. It is also relatively inexpensive and easy to dye, allowing for vibrant turquoise colors.
– Disadvantages: While it is durable, polyester can be less breathable than natural fibers, potentially leading to discomfort in hot conditions. It may also degrade under prolonged exposure to UV light.
Impact on Application:
Polyester’s water resistance makes it suitable for outdoor and travel backpacks, where exposure to moisture is common.
Considerations for International Buyers:
Buyers should ensure compliance with international standards such as ASTM and ISO regarding fabric safety and environmental impact. Countries like France and Egypt may have specific regulations concerning synthetic materials.
2. Nylon
Key Properties:
Nylon is another synthetic fabric that offers excellent strength-to-weight ratios and is resistant to abrasion and mildew. It has a high tensile strength, making it suitable for heavy loads.
Pros & Cons:
– Advantages: Nylon is highly durable and can withstand harsh conditions, making it perfect for rugged outdoor backpacks. Its elasticity allows for flexibility without losing shape.
– Disadvantages: Nylon can be more expensive than polyester and may require special treatment to enhance water resistance. It can also absorb water, leading to increased weight when wet.
Impact on Application:
Nylon is often used in high-performance backpacks, especially those designed for hiking or travel, where durability is critical.
Considerations for International Buyers:
Nylon production may involve chemicals that require compliance with environmental regulations in various regions. Buyers should verify adherence to local standards in Africa and South America, particularly regarding chemical safety.
3. Canvas
Key Properties:
Canvas is a heavy-duty fabric made from cotton or linen. It is known for its sturdiness and ability to withstand wear and tear.
Pros & Cons:
– Advantages: Canvas is highly durable and offers a classic aesthetic that appeals to many consumers. It is also biodegradable, making it a more environmentally friendly option.
– Disadvantages: Canvas can be heavier than synthetic materials and may require waterproofing treatments to enhance its resistance to moisture.
Impact on Application:
Canvas is often used in casual and fashion backpacks, where style and durability are prioritized over performance in extreme conditions.
Considerations for International Buyers:
Eco-conscious brands may prefer canvas due to its natural composition. Buyers should check for compliance with organic standards, especially in Europe, where sustainability is a significant market driver.
4. Leather
Key Properties:
Leather is a natural material known for its luxurious feel and durability. It has good resistance to wear and can last for many years when properly cared for.
Pros & Cons:
– Advantages: Leather provides a premium look and feel, appealing to high-end markets. It is also naturally water-resistant to some extent and can be treated for enhanced performance.
– Disadvantages: Leather is typically more expensive than synthetic options and requires more care and maintenance. It is also less flexible than fabrics like nylon and polyester.
Impact on Application:
Leather is often used in fashion-forward backpacks aimed at urban consumers, where aesthetics and durability are essential.
Considerations for International Buyers:
Buyers should ensure that leather products comply with regulations regarding animal welfare and environmental impact, particularly in Europe and the Middle East, where such standards are increasingly stringent.
Summary Table
Material | Typical Use Case for turquoise backpack | Key Advantage | Key Disadvantage/Limitation | Relative Cost (Low/Med/High) |
---|---|---|---|---|
Polyester | General-purpose backpacks, outdoor gear | Lightweight, water-resistant | Less breathable than natural fibers | Low |
Nylon | High-performance outdoor backpacks | Highly durable, abrasion-resistant | More expensive, can absorb water | Medium |
Canvas | Casual and fashion backpacks | Durable, biodegradable | Heavier, requires waterproofing | Medium |
Leather | Luxury and fashion-forward backpacks | Premium look and feel | Expensive, requires maintenance | High |
This material selection guide provides actionable insights for B2B buyers considering the diverse needs of their markets, especially in regions like Africa, South America, the Middle East, and Europe. Understanding the properties and implications of each material can facilitate informed purchasing decisions that align with both consumer preferences and regulatory requirements.
In-depth Look: Manufacturing Processes and Quality Assurance for turquoise backpack
When considering the manufacturing processes and quality assurance for turquoise backpacks, international B2B buyers should have a clear understanding of the stages involved, key techniques employed, and the quality standards that govern production. This knowledge is crucial for making informed sourcing decisions that align with their business objectives and market requirements.
Manufacturing Process Overview
The manufacturing of turquoise backpacks involves several key stages, each critical to ensuring the final product meets quality expectations and market standards.
1. Material Preparation
The first step in the manufacturing process is the selection and preparation of materials. Common materials used in backpack production include nylon, polyester, canvas, and eco-friendly fabrics.
- Sourcing: Buyers should consider suppliers that provide high-quality, durable materials. For instance, recycled polyester is increasingly popular due to its environmental benefits.
- Pre-treatment: Materials are often treated for water resistance and durability. This includes applying coatings or finishes that enhance performance.
2. Forming
Once materials are prepared, the next stage involves forming the backpack components.
- Cutting: Automated cutting machines are used to achieve precision in fabric dimensions, reducing waste.
- Sewing: Advanced sewing techniques, including double-stitching and reinforced seams, are utilized to enhance the strength and durability of the backpacks.
3. Assembly
After forming the components, the assembly stage begins.
- Component Assembly: This includes attaching straps, zippers, and other hardware. Quality checks during this phase ensure that all components fit correctly and function as intended.
- Sub-assembly: Some manufacturers may create sub-assemblies (e.g., attaching pockets or frames) before final assembly, allowing for more efficient production.
4. Finishing
The final stage involves finishing touches that enhance the aesthetic and functional qualities of the backpack.
- Quality Inspection: Before moving to packaging, each backpack undergoes a thorough inspection to identify any defects or irregularities.
- Branding: This is also the stage where branding elements, such as logos and tags, are added.
Quality Assurance Framework
Quality assurance is vital in ensuring that the turquoise backpacks meet both international standards and buyer expectations.
International Standards
B2B buyers should be familiar with relevant international quality standards that apply to backpack manufacturing:
- ISO 9001: This standard focuses on quality management systems and is applicable across various industries. It helps ensure that manufacturers maintain consistent quality throughout their processes.
- CE Marking: In Europe, CE marking indicates that a product complies with health, safety, and environmental protection standards. This is particularly important for backpacks sold in the European market.
Industry-Specific Standards
Certain industry-specific certifications may also be relevant:
- API (American Petroleum Institute): While primarily focused on oil and gas, understanding API standards can be beneficial if the backpacks are intended for rugged environments.
- Oeko-Tex Standard 100: This certification indicates that textiles are free from harmful substances, which is increasingly important for consumer safety and environmental sustainability.
Quality Control Checkpoints
Effective quality control (QC) involves several checkpoints throughout the manufacturing process:
-
Incoming Quality Control (IQC): This initial checkpoint assesses raw materials and components before production begins. Suppliers should provide documentation of material certifications.
-
In-Process Quality Control (IPQC): During production, IPQC ensures adherence to quality standards at various stages. This includes checks on stitching, component fit, and material integrity.
-
Final Quality Control (FQC): After assembly and before packaging, FQC involves a comprehensive inspection of finished products to ensure they meet all specifications and standards.
Common Testing Methods
To ensure quality and durability, several testing methods are commonly employed:
- Tensile Strength Testing: Measures how much force the fabric can withstand before breaking.
- Water Resistance Testing: Assesses how well the backpack materials repel water, crucial for outdoor products.
- Zipper and Hardware Testing: Ensures that zippers and other closures function properly under repeated use.
Verifying Supplier Quality Control
B2B buyers can take several steps to verify the quality control processes of their suppliers:
- Audits: Conducting regular audits of suppliers can provide insights into their production processes and adherence to quality standards. Buyers should request access to audit reports or certifications.
- Third-Party Inspections: Engaging third-party inspection services can provide an unbiased assessment of product quality before shipping. This is particularly beneficial for buyers in regions where they cannot easily visit factories.
- Documentation and Reporting: Buyers should require suppliers to maintain comprehensive QC documentation, including test results and inspection reports, to ensure transparency and accountability.
Quality Control Considerations for International Buyers
For international buyers, particularly those from Africa, South America, the Middle East, and Europe, several nuances should be considered:
- Cultural Differences: Understanding cultural attitudes towards quality and compliance can help in negotiating and establishing expectations with suppliers.
- Regulatory Compliance: Buyers must be aware of the specific regulations and standards applicable in their target markets. For example, European buyers need to ensure compliance with EU regulations on product safety.
- Logistics and Lead Times: Longer lead times from overseas suppliers may necessitate more rigorous quality control measures. Buyers should plan accordingly to allow time for inspections and potential rework.
By understanding the manufacturing processes and quality assurance practices associated with turquoise backpacks, international B2B buyers can make informed decisions that align with their quality expectations and market demands. This knowledge not only facilitates better supplier relationships but also enhances product reliability and customer satisfaction in a competitive marketplace.
Related Video: How a Backpack is Made : Every Step on the Production Line
Comprehensive Cost and Pricing Analysis for turquoise backpack Sourcing
Understanding the cost structure and pricing dynamics for sourcing turquoise backpacks is crucial for international B2B buyers. This section outlines the various cost components, price influencers, and practical tips to enhance negotiation strategies and overall cost-efficiency.
Cost Components
- Materials: The choice of materials significantly influences the cost of turquoise backpacks. Common materials include polyester, nylon, and canvas, with prices varying based on quality and availability. Eco-friendly materials, such as recycled fabrics, may incur higher costs but can appeal to sustainability-focused buyers.
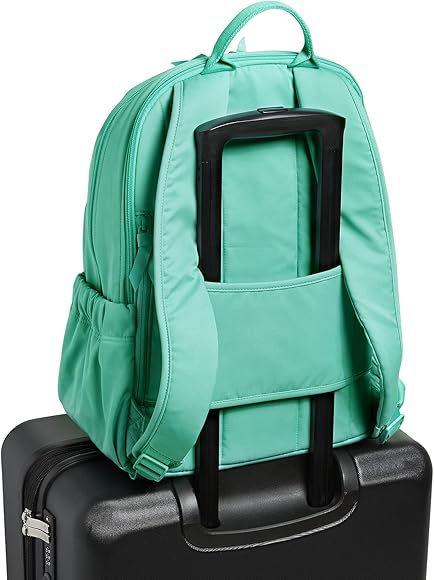
Illustrative Image (Source: Google Search)
- Labor: Labor costs can vary widely depending on the manufacturing country. For instance, countries like China and Vietnam offer competitive labor rates, while regions in Europe might have higher labor costs but also offer superior craftsmanship.
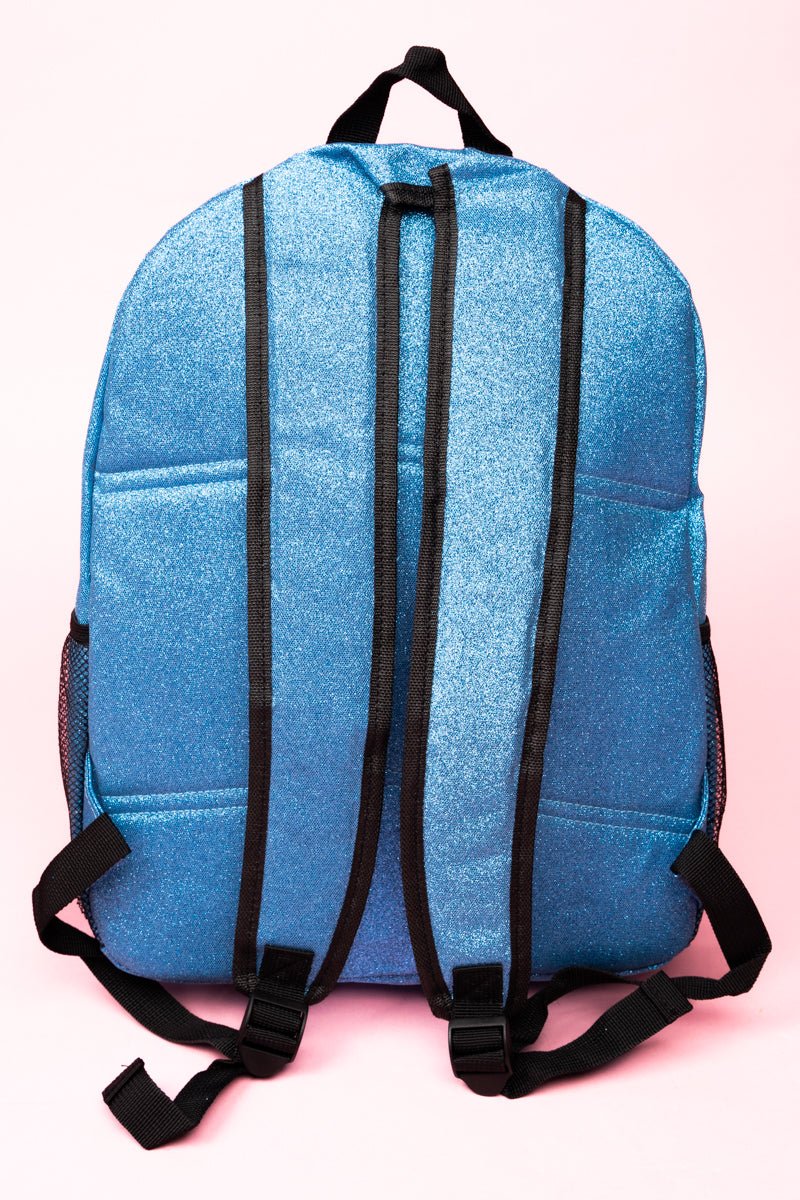
Illustrative Image (Source: Google Search)
-
Manufacturing Overhead: This includes costs related to factory operations, utilities, and equipment maintenance. Understanding the manufacturer’s overhead can provide insights into their pricing structure.
-
Tooling: Initial tooling costs for custom designs or unique specifications can be significant. A one-time investment is often required to create molds or specialized equipment for producing distinct backpack features.
-
Quality Control (QC): Implementing stringent quality control measures is essential to ensure product consistency and compliance with international standards. This may involve additional costs, but it is vital for maintaining brand reputation.
-
Logistics: Shipping costs are a major factor in the total cost of ownership. Factors such as distance, shipping method, and customs duties can greatly affect the final price of the backpacks.
-
Margin: Suppliers typically add a profit margin to the base cost, which varies depending on their business model and market positioning.
Price Influencers
-
Volume/MOQ (Minimum Order Quantity): Bulk orders often lead to lower per-unit costs. Understanding the supplier’s MOQ can help buyers negotiate better pricing, especially when planning for larger inventory needs.
-
Specifications/Customization: Custom features, such as unique designs, additional pockets, or branding, can increase costs. Buyers should clearly define specifications to avoid unexpected charges.
-
Quality/Certifications: Higher-quality materials and certifications (e.g., eco-friendly certifications) can lead to increased costs. However, these investments can enhance product appeal in markets demanding higher standards.
-
Supplier Factors: The reliability and reputation of the supplier can impact pricing. Established suppliers may command higher prices due to their proven track record, while newer entrants might offer lower rates to build clientele.
-
Incoterms: Understanding Incoterms (International Commercial Terms) is vital as they define the responsibilities of buyers and sellers regarding shipping, insurance, and tariffs. Choosing the right Incoterm can influence overall costs.
Buyer Tips
-
Negotiation: Always negotiate pricing based on total cost considerations rather than just the unit price. Highlighting potential bulk orders or long-term partnerships can leverage better deals.
-
Cost-Efficiency: Analyze the total cost of ownership, which includes purchase price, shipping, and potential returns due to quality issues. This holistic view can lead to more informed purchasing decisions.
-
Pricing Nuances: Be aware of regional pricing variations. For instance, sourcing from Southeast Asia may offer lower costs compared to European suppliers, but consider the trade-offs in terms of lead times and shipping costs.
-
Market Trends: Stay informed about market trends and demand shifts in your target regions (Africa, South America, the Middle East, and Europe). This knowledge can aid in negotiating better prices based on market conditions.
Disclaimer
Prices mentioned in sourcing discussions are indicative and can fluctuate based on market conditions, supplier negotiations, and order specifics. It’s essential to conduct thorough market research and supplier assessments before finalizing any contracts.
Spotlight on Potential turquoise backpack Manufacturers and Suppliers
This section offers a look at a few manufacturers active in the ‘turquoise backpack’ market. This is a representative sample for illustrative purposes; B2B buyers must conduct their own extensive due diligence before any engagement. Information is synthesized from public sources and general industry knowledge.
Essential Technical Properties and Trade Terminology for turquoise backpack
Key Technical Properties of Turquoise Backpacks
When sourcing turquoise backpacks, understanding the technical properties is crucial for ensuring product quality and alignment with market demands. Here are some essential specifications to consider:
-
Material Grade
The material used in backpacks significantly impacts durability, weight, and aesthetic appeal. Common materials include nylon, polyester, and canvas. For turquoise backpacks, high-denier nylon is often preferred for its strength and water resistance, while eco-friendly fabrics are gaining traction among environmentally conscious consumers. Selecting the right material grade not only influences the product’s lifespan but also affects its marketability in diverse regions. -
Weight Capacity
Weight capacity refers to the maximum load a backpack can support without compromising its structural integrity. This is particularly important for B2B buyers targeting outdoor and travel markets. A typical turquoise backpack should have a weight capacity ranging from 15 to 25 kilograms, depending on its design and intended use. Ensuring the backpack meets these specifications will enhance customer satisfaction and reduce the likelihood of returns. -
Zipper Quality
The quality of zippers plays a vital role in the overall functionality and durability of backpacks. For turquoise backpacks, YKK zippers are often the industry standard due to their reliability and smooth operation. B2B buyers should verify that zippers are corrosion-resistant and have a high cycle count to prevent failures during use. This attention to detail can significantly enhance the product’s reputation. -
Water Resistance
Water resistance is a critical feature for backpacks, especially in regions with unpredictable weather. Look for backpacks that incorporate water-resistant coatings or materials, such as polyurethane or TPU (thermoplastic polyurethane). This specification not only protects the contents from moisture but also caters to the growing demand for outdoor and travel gear in markets like Africa and South America. -
Size and Dimensions
The dimensions of a backpack affect its usability and market appeal. Standard sizes for backpacks can range from 20 to 40 liters in capacity, catering to various consumer needs. B2B buyers should consider specific dimensions that align with target demographics, such as school children, travelers, or outdoor enthusiasts.
Common Trade Terminology
Understanding trade terminology is essential for effective communication and negotiation in the backpack industry. Here are some commonly used terms:
-
OEM (Original Equipment Manufacturer)
OEM refers to a company that produces products or components that are used in another company’s end products. For B2B buyers, partnering with an OEM allows for customization of turquoise backpacks while leveraging the manufacturer’s expertise in production and quality control. -
MOQ (Minimum Order Quantity)
MOQ indicates the smallest number of units a supplier is willing to produce or sell. This term is crucial for B2B buyers as it affects initial investment and inventory management. Typical MOQs for backpacks can range from 500 to 5,000 units, depending on the manufacturer and product complexity. -
RFQ (Request for Quotation)
An RFQ is a document that buyers send to suppliers to request pricing and terms for specific products. For turquoise backpacks, an RFQ should detail specifications, quantities, and delivery timelines to ensure accurate quotes. This process helps streamline procurement and fosters competitive pricing. -
Incoterms (International Commercial Terms)
Incoterms are a set of international rules that define the responsibilities of buyers and sellers in the shipping process. Familiarity with terms like FOB (Free on Board) or CIF (Cost, Insurance, and Freight) is essential for B2B buyers to understand shipping costs and risks associated with transporting turquoise backpacks across borders. -
Lead Time
Lead time refers to the time taken from placing an order to receiving the product. This is a critical factor in supply chain management, especially for seasonal markets. Understanding lead times helps B2B buyers plan inventory effectively and meet customer demand without delays.
By grasping these technical properties and trade terms, international B2B buyers can make informed decisions when sourcing turquoise backpacks, ultimately enhancing their business operations and market competitiveness.
Navigating Market Dynamics, Sourcing Trends, and Sustainability in the turquoise backpack Sector
Market Overview & Key Trends
The turquoise backpack sector is experiencing dynamic growth, driven by a combination of fashion trends, increased outdoor activities, and the rise of eco-conscious consumerism. The global backpack market is projected to reach $85 billion by 2030, with turquoise backpacks gaining popularity due to their vibrant aesthetics and versatility. Key markets include Europe, where outdoor tourism thrives, and regions in Africa and South America, where youth culture increasingly embraces unique and colorful fashion statements.
B2B buyers should be aware of emerging sourcing trends, particularly the “China Plus One” strategy. This approach encourages diversifying supply chains beyond China to countries like Vietnam, India, and Bangladesh, which offer competitive pricing and manufacturing capabilities. In addition, advancements in technology, such as digital sourcing platforms and data analytics, are enabling buyers to identify reliable suppliers quickly and streamline procurement processes. These tools enhance transparency, allowing for better decision-making regarding lead times and quality control.
Furthermore, buyers must adapt to fluctuating consumer demands influenced by social media trends and sustainability concerns. Real-time data analytics can provide insights into trending colors and styles, ensuring that inventory aligns with market preferences. Engaging with local manufacturers can also facilitate faster response times and reduce shipping costs, particularly for buyers in Europe and the Middle East.
Sustainability & Ethical Sourcing in B2B
Sustainability has become a critical consideration in the sourcing of turquoise backpacks. The environmental impact of production processes, particularly in textile manufacturing, necessitates a focus on ethical sourcing and the use of eco-friendly materials. B2B buyers should prioritize suppliers who adhere to sustainable practices, such as using organic cotton, recycled materials, or biodegradable fabrics. Certifications like Global Organic Textile Standard (GOTS) and OEKO-TEX can help verify that materials meet environmental and safety standards.
Moreover, ethical supply chains are increasingly important as consumers demand transparency. Brands that demonstrate a commitment to fair labor practices and sustainable sourcing are more likely to resonate with eco-conscious consumers. For B2B buyers, this means establishing relationships with manufacturers that not only comply with local regulations but also uphold international labor rights.
Investing in sustainable practices can also lead to long-term cost savings. Utilizing renewable materials can reduce dependency on fluctuating fossil fuel prices, while efficient manufacturing processes can lower waste and improve overall production efficiency. As sustainability becomes a competitive differentiator, B2B buyers should align their sourcing strategies with these values to enhance brand reputation and consumer loyalty.
Brief Evolution/History
The turquoise backpack has evolved significantly over the past few decades. Initially viewed as a functional item for students and travelers, the backpack has transformed into a fashion statement, with brands experimenting with colors, designs, and materials. The rise of outdoor activities and travel culture has fueled demand for stylish yet practical backpacks, leading to the emergence of niche markets.
Manufacturers have also adapted to changing consumer preferences by incorporating innovative materials and sustainable practices. The shift towards eco-friendly production reflects broader societal trends towards sustainability, pushing brands to rethink their sourcing strategies. As the market continues to evolve, international B2B buyers must stay attuned to these shifts to remain competitive and relevant in the turquoise backpack sector.
Related Video: International Trade Explained
Frequently Asked Questions (FAQs) for B2B Buyers of turquoise backpack
-
What should I consider when vetting suppliers for turquoise backpacks?
When vetting suppliers, prioritize their experience in manufacturing backpacks and their reputation in the industry. Request samples to assess quality and craftsmanship. Check for certifications like ISO or compliance with safety standards, particularly if you are sourcing from regions like Asia or Africa. Additionally, investigate their production capacity, lead times, and reliability in meeting deadlines. Utilize platforms like Alibaba or trade shows to gather feedback from other buyers and ensure a trustworthy partnership. -
Can I customize turquoise backpacks to fit my brand’s needs?
Yes, many manufacturers offer customization options, including color variations, materials, and branding elements like logos. Discuss your specific requirements early in the negotiation process to ensure the supplier can accommodate them. Be mindful of potential costs associated with customization, such as design fees or higher minimum order quantities (MOQs). Ensure you receive a prototype before mass production to confirm that the customization meets your expectations. -
What are the typical MOQs and lead times for turquoise backpacks?
Minimum Order Quantities (MOQs) for turquoise backpacks can range from 500 to 5,000 units, depending on the manufacturer and customization level. Lead times typically vary between 4 to 8 weeks, influenced by the supplier’s location and production capacity. To avoid delays, communicate your timeline and needs upfront, and consider placing orders well in advance of peak sales periods. Always have a buffer in your timeline for unexpected issues in production or shipping. -
What payment methods are commonly accepted by backpack suppliers?
Common payment methods include wire transfers, letters of credit, and online payment platforms like PayPal. Each method carries different risks and costs, so choose one that aligns with your business practices and offers sufficient buyer protection. For larger orders, consider negotiating payment terms that include a deposit upfront and the remainder upon delivery or inspection. This approach can minimize risk while ensuring the supplier is committed to fulfilling the order. -
How can I ensure quality assurance for my turquoise backpacks?
Establish a clear quality assurance (QA) process with your supplier, which may include pre-production samples and in-line inspections. Request third-party quality certifications and conduct factory audits, especially if sourcing from countries with less stringent regulations. Specify your quality standards in the contract to hold the supplier accountable. It’s also beneficial to build a relationship with a local inspection company to facilitate on-site checks before shipment. -
What logistics considerations should I keep in mind when importing backpacks?
Logistics for importing turquoise backpacks involves understanding shipping options, customs regulations, and potential tariffs. Choose between air freight for speed or sea freight for cost-effectiveness based on your urgency and budget. Collaborate with a reliable freight forwarder who can guide you through customs clearance and paperwork. Additionally, consider shipping insurance to protect your investment against loss or damage during transit. -
How should I handle disputes with suppliers?
To handle disputes effectively, maintain clear and open communication with your supplier. Document all agreements, specifications, and communications to provide a reference in case of misunderstandings. If issues arise, attempt to resolve them amicably through negotiation. If necessary, escalate the matter to mediation or arbitration as outlined in your contract. Having a legal framework in place can protect your interests and facilitate a more efficient resolution process. -
What certifications should I look for in a backpack supplier?
Look for certifications that demonstrate compliance with international safety and environmental standards. ISO 9001 for quality management, ISO 14001 for environmental management, and compliance with REACH or CPSIA regulations for safety are critical. These certifications indicate a commitment to quality and sustainability, which can enhance your brand’s reputation. Additionally, inquire about ethical sourcing certifications, such as Fair Trade, which can resonate well with consumers in markets like Europe and North America.
Strategic Sourcing Conclusion and Outlook for turquoise backpack
In conclusion, strategic sourcing for turquoise backpacks is essential for B2B buyers aiming to enhance their market presence and operational efficiency. The global landscape, dominated by countries like China, Vietnam, and India, offers various manufacturing advantages, including scalability, quality craftsmanship, and competitive pricing. By adopting a diversified sourcing strategy, businesses can mitigate risks associated with supply chain disruptions and leverage regional strengths to optimize costs.
Key takeaways for international buyers include the importance of evaluating total cost of ownership beyond unit prices, ensuring supplier reliability, and prioritizing compliance with social and environmental standards. As the demand for eco-friendly and high-quality backpacks grows, aligning sourcing strategies with these trends will be critical.
Looking forward, we encourage B2B buyers from Africa, South America, the Middle East, and Europe to explore innovative partnerships with manufacturers that prioritize sustainability and craftsmanship. By doing so, you not only enhance your product offerings but also position your brand as a leader in the competitive backpack market. Embrace the opportunities that strategic sourcing presents and take actionable steps towards building a resilient supply chain.