Your Ultimate Guide to Sourcing Tool Backpack
Guide to Tool Backpack
- Introduction: Navigating the Global Market for tool backpack
- Understanding tool backpack Types and Variations
- Key Industrial Applications of tool backpack
- Strategic Material Selection Guide for tool backpack
- In-depth Look: Manufacturing Processes and Quality Assurance for tool backpack
- Comprehensive Cost and Pricing Analysis for tool backpack Sourcing
- Spotlight on Potential tool backpack Manufacturers and Suppliers
- Essential Technical Properties and Trade Terminology for tool backpack
- Navigating Market Dynamics, Sourcing Trends, and Sustainability in the tool backpack Sector
- Frequently Asked Questions (FAQs) for B2B Buyers of tool backpack
- Strategic Sourcing Conclusion and Outlook for tool backpack
Introduction: Navigating the Global Market for tool backpack
Navigating the global market for tool backpacks requires a keen understanding of both the product and the diverse needs of international buyers. Tool backpacks are essential for professionals across various industries, including construction, electrical work, and HVAC, offering an organized, efficient way to transport tools and equipment. As the demand for portable solutions grows, so does the need for buyers to make informed sourcing decisions that align with their operational requirements and regional preferences.
This comprehensive guide delves into the multifaceted world of tool backpacks, covering critical aspects such as types of backpacks, materials used, manufacturing and quality control processes, reliable suppliers, and cost considerations. We also explore market trends and frequently asked questions to equip you with the insights necessary for successful procurement.
For B2B buyers from regions like Africa, South America, the Middle East, and Europe, understanding these elements is vital for optimizing inventory and enhancing productivity. Whether you’re in Argentina looking for durable options or in Brazil seeking cost-effective solutions, this guide empowers you to navigate the global landscape confidently. By leveraging the information presented, you can streamline your sourcing process, ensure quality, and ultimately drive your business forward in a competitive market.
Understanding tool backpack Types and Variations
Type Name | Key Distinguishing Features | Primary B2B Applications | Brief Pros & Cons for Buyers |
---|---|---|---|
Multi-Compartment Tool Backpack | Multiple pockets and compartments for organization | Construction, Electrical, HVAC | Pros: Excellent organization; Cons: May be bulkier. |
Heavy-Duty Tool Backpack | Reinforced materials, heavy load capacity | Manufacturing, Carpentry | Pros: Durable; Cons: Heavier, potentially more expensive. |
Lightweight Tool Backpack | Compact design, minimal features | Maintenance, Repair Services | Pros: Easy to carry; Cons: Limited storage space. |
Water-Resistant Tool Backpack | Waterproof materials, sealed zippers | Outdoor Work, Plumbing | Pros: Protects tools from moisture; Cons: Higher cost. |
Specialty Tool Backpack | Designed for specific trades (e.g., electricians) | Niche trades, Specialized tasks | Pros: Tailored for specific tools; Cons: Less versatile. |
Multi-Compartment Tool Backpack
This type of backpack is characterized by its numerous pockets and compartments, allowing users to organize tools efficiently. Ideal for industries like construction, electrical work, and HVAC, these backpacks enable professionals to keep essential tools easily accessible. When purchasing, consider the size and layout of compartments to ensure they meet the specific needs of your team, as well as the quality of zippers and stitching for durability.
Heavy-Duty Tool Backpack
Constructed from reinforced materials, heavy-duty tool backpacks are designed to carry substantial loads without compromising on durability. They are particularly suited for manufacturing and carpentry environments where tools are often heavy and numerous. Buyers should focus on weight capacity and material quality, as investing in a robust backpack can reduce replacement costs and improve worker productivity over time.
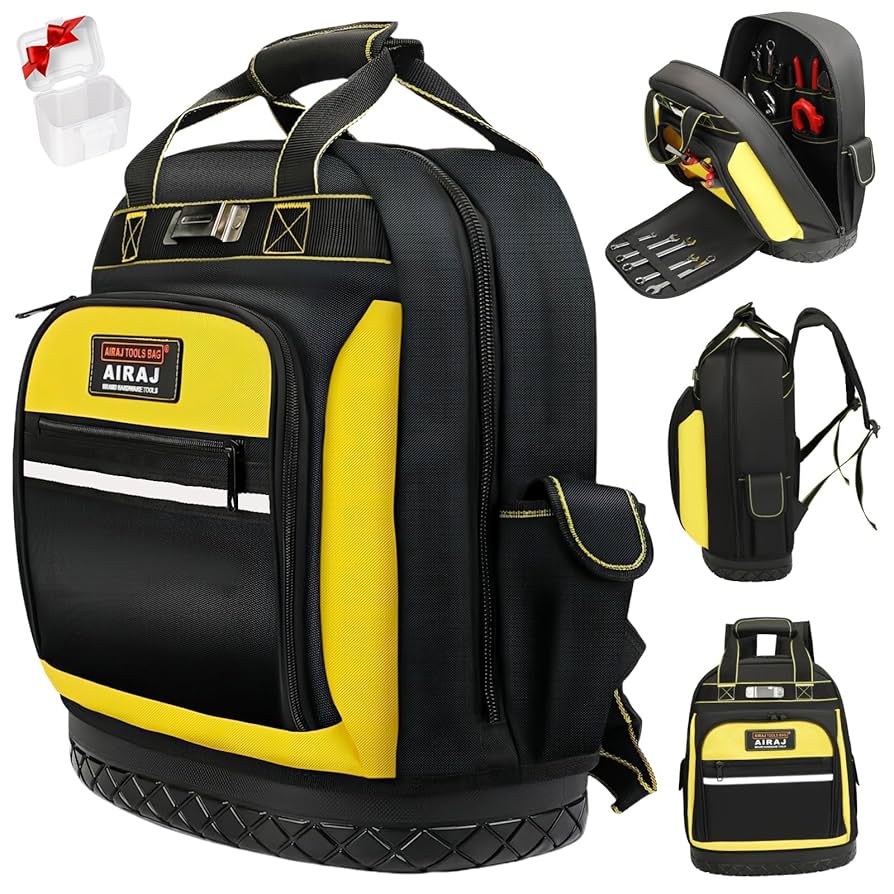
Illustrative Image (Source: Google Search)
Lightweight Tool Backpack
For those requiring a more compact and easy-to-carry option, lightweight tool backpacks offer simplicity and convenience. These are best suited for maintenance and repair services where mobility is key. When considering a lightweight option, evaluate the trade-off between weight and storage capacity, as these backpacks may not accommodate larger tools or extensive collections.
Water-Resistant Tool Backpack
These backpacks are made from waterproof materials and feature sealed zippers, making them ideal for outdoor work or plumbing tasks where exposure to moisture is a concern. The ability to protect tools from the elements is a significant advantage, especially in regions with unpredictable weather. Buyers should assess the level of water resistance needed based on their specific work environments and the potential for exposure to wet conditions.
Specialty Tool Backpack
Specialty tool backpacks are tailored for specific trades, such as electricians or plumbers, providing designated spaces for unique tools. This type of backpack enhances efficiency by ensuring that all necessary equipment is organized and ready for use. When purchasing, it’s crucial to ensure that the design aligns with the tools your team uses regularly, as this can significantly impact workflow and productivity in specialized tasks.
Related Video: Large Language Models (LLMs) – Everything You NEED To Know
Key Industrial Applications of tool backpack
Industry/Sector | Specific Application of Tool Backpack | Value/Benefit for the Business | Key Sourcing Considerations for this Application |
---|---|---|---|
Construction | On-site tool organization and transport | Increased efficiency and reduced downtime | Durability of materials, weight capacity, and ergonomic design |
Electrical Services | Carrying electrical tools and safety gear | Streamlined workflow and improved safety compliance | Water resistance, compartmentalization for tools, and safety features |
HVAC (Heating, Ventilation, and Air Conditioning) | Equipment transport for installation and repair | Enhanced mobility and quicker response to service calls | Size compatibility with tools, insulation properties, and ease of access |
Automotive Repair | Tool management during vehicle service | Reduced tool loss and improved service turnaround times | Robustness, ease of cleaning, and organizational features |
Telecommunications | Transporting installation tools | Efficient deployment of services and reduced project delays | Lightweight design, protective padding, and weather resistance |
In the construction industry, tool backpacks are essential for on-site organization and transport of various tools and equipment. They help workers streamline their workflow by keeping all necessary items readily accessible, thus minimizing downtime. B2B buyers in this sector should prioritize backpacks made from durable materials that can withstand harsh job site conditions, along with ergonomic designs to reduce physical strain.
For electrical services, tool backpacks are indispensable for carrying essential tools and safety gear. They facilitate a more organized approach to work, ensuring that technicians can quickly access the tools they need while maintaining compliance with safety regulations. Buyers should look for features such as water resistance and effective compartmentalization, which can protect sensitive electrical tools from damage.
In the HVAC sector, professionals use tool backpacks to transport equipment for installation and repair jobs. These backpacks enhance mobility, allowing technicians to respond quickly to service calls. Buyers must consider size compatibility with their specific tools, as well as insulation properties to protect sensitive equipment during transport.
Automotive repair businesses benefit significantly from tool backpacks that provide effective management of tools during vehicle servicing. These backpacks help reduce the likelihood of tool loss and improve service turnaround times, which is crucial in a competitive market. Robustness and ease of cleaning are critical factors for buyers looking to maintain hygiene and efficiency in their operations.
Finally, in the telecommunications sector, tool backpacks are used to transport installation tools, enabling efficient deployment of services. This not only reduces project delays but also enhances overall service delivery. Buyers should focus on lightweight designs that are easy to carry, as well as protective padding to safeguard tools from damage during transit.
Related Video: Working Tool Backpack Tour Maintenance and Handyman
Strategic Material Selection Guide for tool backpack
When selecting materials for tool backpacks, it’s essential to consider various factors that affect performance, durability, and overall cost. Here, we analyze four common materials used in the manufacturing of tool backpacks, providing insights that are particularly relevant for international B2B buyers from regions such as Africa, South America, the Middle East, and Europe.
1. Nylon
Key Properties:
Nylon is a synthetic polymer known for its strength, elasticity, and resistance to abrasion. It typically has a temperature rating up to 120°C and can withstand moderate pressure without deforming.
Pros & Cons:
Nylon is highly durable and lightweight, making it ideal for tool backpacks that require frequent transport. However, it can be more expensive than natural fibers and may require specialized manufacturing techniques, which can increase production complexity.
Impact on Application:
Nylon’s resistance to wear and tear makes it suitable for heavy-duty applications, especially in construction and industrial settings. It is also water-resistant, which is beneficial for outdoor use.
Considerations for International Buyers:
Nylon is widely accepted across international markets, but buyers should ensure compliance with local environmental regulations regarding synthetic materials. Standards such as ASTM D751 (for textile testing) are relevant.
2. Polyester
Key Properties:
Polyester is another synthetic material known for its durability and resistance to shrinking and stretching. It can typically handle temperatures up to 130°C and is resistant to many chemicals.
Pros & Cons:
Polyester is generally less expensive than nylon and offers good UV resistance, making it suitable for outdoor applications. However, it may not be as strong as nylon and can be prone to fading over time.
Impact on Application:
Polyester is ideal for tool backpacks used in environments where exposure to sunlight and moisture is common. Its lightweight nature also contributes to ease of transport.
Considerations for International Buyers:
Compliance with standards such as ISO 105 (for color fastness) is crucial for ensuring product quality. Buyers should also consider local preferences for materials, as polyester may be favored in certain markets for its cost-effectiveness.
3. Canvas
Key Properties:
Canvas is a heavy-duty fabric made from cotton or a blend of cotton and synthetic fibers. It is breathable and can withstand temperatures up to 180°C, making it suitable for various applications.
Pros & Cons:
Canvas is known for its durability and classic aesthetic appeal. However, it can be heavier than synthetic alternatives and may require additional treatments to enhance water resistance.
Impact on Application:
Canvas tool backpacks are often used in trades where a rugged appearance is valued, such as carpentry or landscaping. Its breathability also makes it comfortable for extended wear.
Considerations for International Buyers:
Canvas is generally well-accepted in international markets, but buyers should be aware of regulations regarding cotton sourcing and environmental impact. Compliance with standards like GOTS (Global Organic Textile Standard) may also be relevant.
4. Leather
Key Properties:
Leather is a natural material prized for its strength and durability. It can handle a wide range of temperatures and offers excellent resistance to wear and tear.
Pros & Cons:
Leather provides a premium look and feel, which can enhance brand perception. However, it is typically more expensive than synthetic materials and may require more maintenance to prevent degradation.
Impact on Application:
Leather tool backpacks are often used in high-end markets or by professionals who prioritize aesthetics along with functionality, such as electricians or designers.
Considerations for International Buyers:
Buyers should ensure compliance with local animal welfare regulations and environmental standards related to leather processing. Certifications like LWG (Leather Working Group) can provide assurance of responsible sourcing.
Summary Table
Material | Typical Use Case for tool backpack | Key Advantage | Key Disadvantage/Limitation | Relative Cost (Low/Med/High) |
---|---|---|---|---|
Nylon | Heavy-duty, industrial applications | Lightweight, durable | Higher cost, complex manufacturing | High |
Polyester | Outdoor and UV-exposed environments | Cost-effective, UV resistant | Less durable than nylon, fading | Medium |
Canvas | Trades requiring rugged aesthetics | Durable, breathable | Heavier, may need water treatment | Medium |
Leather | High-end, aesthetic-focused applications | Premium look and durability | Expensive, requires maintenance | High |
This material selection guide offers valuable insights for B2B buyers, helping them make informed decisions that align with their product requirements and market standards.
In-depth Look: Manufacturing Processes and Quality Assurance for tool backpack
Manufacturing Processes for Tool Backpacks
The manufacturing of tool backpacks involves several critical stages, each designed to ensure that the final product meets the rigorous demands of functionality, durability, and user comfort. Understanding these processes helps international B2B buyers make informed decisions when sourcing from manufacturers, particularly in regions like Africa, South America, the Middle East, and Europe.
1. Material Preparation
Material selection is foundational in the production of tool backpacks. Manufacturers typically utilize a range of fabrics, including polyester, nylon, and canvas, each offering different levels of durability and water resistance. The preparation stage includes:
- Sourcing Materials: Buyers should ensure that suppliers source materials that comply with international safety and environmental standards. Look for certifications such as OEKO-TEX or GOTS for eco-friendly fabrics.
- Cutting: Once materials are sourced, they are cut into specific shapes and sizes based on the design specifications. Precision in cutting is crucial to minimize waste and ensure quality.
2. Forming
Forming involves shaping the cut materials into the components of the backpack. This stage can include various techniques:
- Sewing: The primary method for assembling tool backpacks is sewing. Manufacturers may use double stitching in high-stress areas to enhance durability.
- Heat Sealing: For waterproof backpacks, heat sealing is often used to bond seams, preventing water ingress.
- Molding: Some backpacks incorporate molded components, such as hard-shell pockets, which require specialized equipment.
3. Assembly
The assembly stage brings together all the components of the backpack. Key processes include:
- Zippers and Buckles Installation: Quality control is critical during this step. Manufacturers should ensure that zippers are tested for durability and ease of use.
- Straps and Handles Attachment: Reinforcement of these areas is essential, as they are subject to the most stress during use.
- Quality Checks During Assembly: Implementing in-process quality checks (IPQC) at this stage can help catch defects early.
4. Finishing
Finishing touches enhance both the aesthetics and functionality of the tool backpack. This includes:
- Final Stitching and Trimming: Any loose threads are trimmed, and final stitches are made to ensure a polished appearance.
- Waterproofing Treatments: If applicable, backpacks may undergo additional treatments to enhance water resistance.
- Branding: Application of logos or branding elements should be done with attention to detail to maintain quality.
Quality Assurance Standards
Quality assurance (QA) is critical in ensuring that the final product meets the expected standards. For tool backpacks, adherence to international and industry-specific standards is essential.
Relevant International Standards
- ISO 9001: This standard outlines the criteria for a quality management system (QMS). Manufacturers who comply with ISO 9001 demonstrate their ability to consistently provide products that meet customer and regulatory requirements.
- CE Marking: For products sold in the European market, CE marking indicates conformity with health, safety, and environmental protection standards.
- API Standards: If the backpacks are designed for industrial use, compliance with American Petroleum Institute (API) standards may be necessary, particularly for products used in hazardous environments.
Quality Control Checkpoints
Effective quality control involves multiple checkpoints throughout the manufacturing process:
- Incoming Quality Control (IQC): Inspecting materials upon arrival to ensure they meet specifications before production begins.
- In-Process Quality Control (IPQC): Ongoing inspections during the assembly process to identify and rectify defects early.
- Final Quality Control (FQC): Comprehensive testing of the finished product to ensure it meets all quality and safety standards.
Common Testing Methods
To ensure the durability and functionality of tool backpacks, several testing methods are commonly employed:
- Load Testing: Backpacks are tested under weight to simulate usage conditions and ensure structural integrity.
- Water Resistance Testing: This assesses how well the backpack withstands exposure to water, which is critical for tool backpacks.
- Material Abrasion Testing: Evaluates the wear resistance of the fabrics used in the backpack.
Verifying Supplier Quality Control
International B2B buyers should take proactive steps to verify the quality control processes of potential suppliers:
- Supplier Audits: Conduct regular audits of suppliers’ manufacturing facilities to ensure adherence to quality standards. This can include reviewing their production processes, quality control measures, and employee training programs.
- Quality Reports: Request detailed quality reports from suppliers, including data on defect rates and corrective actions taken.
- Third-Party Inspections: Engage independent third-party inspection services to evaluate products before shipment. This adds an extra layer of assurance regarding product quality.
Navigating Quality Control Nuances
For buyers from diverse regions such as Africa, South America, the Middle East, and Europe, it is crucial to understand the nuances of quality control in international trade:
- Cultural Differences: Be aware of cultural differences in business practices that may impact quality expectations and communication.
- Regulatory Compliance: Different regions have varying regulations regarding product safety and quality. Ensure your suppliers understand and comply with the relevant regulations in your target market.
- Language Barriers: Establish clear communication channels and documentation to avoid misunderstandings that could affect quality.
Conclusion
Understanding the manufacturing processes and quality assurance practices for tool backpacks is vital for B2B buyers seeking reliable suppliers. By focusing on material preparation, forming, assembly, and finishing, along with stringent quality control measures, buyers can ensure that they source high-quality products that meet their specific needs. By implementing thorough verification processes, buyers can mitigate risks and foster successful partnerships with manufacturers worldwide.
Related Video: How a Backpack is Made : Every Step on the Production Line
Comprehensive Cost and Pricing Analysis for tool backpack Sourcing
Understanding the cost structure and pricing dynamics of tool backpacks is crucial for international B2B buyers, especially those operating in diverse markets such as Africa, South America, the Middle East, and Europe. By grasping the various cost components and price influencers, businesses can make informed sourcing decisions that align with their operational needs and budget constraints.
Cost Components
-
Materials
The material cost is a significant portion of the overall expense. High-quality fabrics, zippers, and padding directly impact durability and functionality. Common materials include nylon, polyester, and leather, each with varying price points. Buyers should consider not only the initial cost but also the longevity and performance of the materials selected. -
Labor
Labor costs fluctuate based on the manufacturing location. For instance, countries with lower labor costs, like some in South America and Africa, may offer competitive pricing, but this can be offset by potential quality issues. It’s essential to evaluate the skill level of workers and the associated labor costs in the production region. -
Manufacturing Overhead
This encompasses costs related to utilities, equipment maintenance, and facility management. Overhead can vary widely depending on the factory’s operational efficiency and location. Understanding these costs can aid in negotiating better pricing. -
Tooling
Tooling costs are relevant when custom designs or unique features are required. These costs can be significant for low-volume orders but can be amortized over larger production runs, making volume purchases more cost-effective. -
Quality Control (QC)
Implementing stringent QC processes is essential for maintaining product standards. While this incurs additional costs, the long-term benefits of reducing defects and returns can justify the investment. -
Logistics
Shipping and handling costs are influenced by the distance between the supplier and the buyer, as well as the chosen shipping method. International logistics can introduce complexities, including tariffs and customs duties, which should be factored into the total cost.
- Margin
Supplier profit margins can vary based on market dynamics and competition. Understanding the margin expectations of suppliers can help buyers negotiate more effectively.
Price Influencers
-
Volume/MOQ (Minimum Order Quantity)
Higher order volumes often lead to lower per-unit costs. Buyers should assess their demand forecasts to determine optimal order sizes that balance inventory costs with pricing advantages. -
Specifications/Customization
Customization can significantly affect pricing. Detailed specifications may require unique tooling or materials, which can increase costs. Buyers should clearly define their needs to avoid unexpected price hikes. -
Quality/Certifications
Products that meet specific quality standards or certifications typically command higher prices. However, investing in certified products may reduce risks associated with performance and compliance. -
Supplier Factors
Supplier reputation, reliability, and production capabilities can influence pricing. Established suppliers may charge a premium for their experience and quality assurance. -
Incoterms
Understanding Incoterms (International Commercial Terms) is vital for determining who is responsible for shipping costs and risks. This knowledge helps in accurately calculating the total landed cost of tool backpacks.
Buyer Tips
-
Negotiation
Leverage knowledge of cost components and market conditions during negotiations. Aim for transparency regarding pricing structures to foster long-term partnerships. -
Cost-Efficiency
Consider total cost of ownership (TCO) rather than just initial purchase prices. Evaluate factors such as durability and maintenance to make more informed decisions. -
Pricing Nuances
International buyers should be aware of regional pricing variances. For example, sourcing from local suppliers in South America or Africa may yield lower logistics costs, while European suppliers might offer advanced technology and higher quality.
Disclaimer on Indicative Prices
Pricing can vary widely based on market conditions, material availability, and supplier negotiations. It is advisable for buyers to conduct thorough market research and obtain multiple quotes to ensure competitive pricing and value for money.
Spotlight on Potential tool backpack Manufacturers and Suppliers
This section offers a look at a few manufacturers active in the ‘tool backpack’ market. This is a representative sample for illustrative purposes; B2B buyers must conduct their own extensive due diligence before any engagement. Information is synthesized from public sources and general industry knowledge.
Essential Technical Properties and Trade Terminology for tool backpack
When sourcing tool backpacks for B2B purposes, understanding the essential technical properties and trade terminology is crucial for making informed purchasing decisions. Below, we delve into key specifications and common jargon that can aid international buyers, particularly those from Africa, South America, the Middle East, and Europe.
Essential Technical Properties
-
Material Grade
– Definition: Refers to the quality and type of materials used in the construction of the tool backpack, such as nylon, polyester, or canvas.
– Importance: Higher material grades enhance durability, resistance to wear and tear, and overall performance in challenging environments. This is particularly vital for buyers in industries like construction or maintenance, where backpacks are subjected to heavy use. -
Load Capacity
– Definition: Indicates the maximum weight the backpack can safely carry, typically measured in kilograms or pounds.
– Importance: Understanding load capacity helps buyers select a backpack that meets their needs without risking damage to the product or injury to the user. This is especially relevant in regions where tools and equipment can be heavy. -
Water Resistance
– Definition: Refers to the ability of the backpack materials to resist water penetration.
– Importance: In many regions, including those with tropical climates or frequent rain, water resistance can protect tools from moisture damage. Buyers should seek backpacks with coatings like polyurethane or features like waterproof zippers for enhanced protection. -
Ergonomic Design
– Definition: A design that promotes comfort and efficiency, often including padded straps, back panels, and adjustable features.
– Importance: Ergonomically designed backpacks reduce strain on the user, which is crucial for professionals who carry tools for extended periods. This consideration can lead to higher productivity and lower injury rates. -
Zipper Quality
– Definition: The durability and functionality of the zippers used in the backpack.
– Importance: High-quality zippers prevent failures during use, which can be a significant inconvenience. Investing in backpacks with robust, corrosion-resistant zippers is advisable, especially in humid or harsh environments. -
Compartments and Organization
– Definition: Refers to the internal and external pockets and organizational features of the backpack.
– Importance: Effective organization allows users to access tools quickly, improving efficiency on the job. Buyers should consider backpacks with customizable compartments to accommodate various tool sizes and types.
Common Trade Terminology
- OEM (Original Equipment Manufacturer)
– Definition: A company that produces parts or equipment that may be marketed by another manufacturer.
– Relevance: Understanding OEM relationships can help buyers identify the source of their products and ensure quality control, especially when sourcing backpacks from different manufacturers.
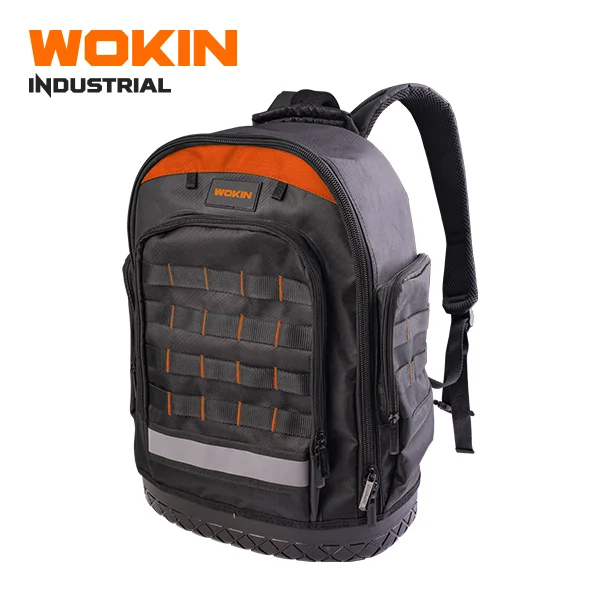
Illustrative Image (Source: Google Search)
-
MOQ (Minimum Order Quantity)
– Definition: The smallest quantity of a product that a supplier is willing to sell.
– Relevance: Knowing the MOQ is essential for budget planning and inventory management. Buyers should negotiate MOQs to align with their needs without overcommitting resources. -
RFQ (Request for Quotation)
– Definition: A document sent to suppliers requesting price quotes for specific products.
– Relevance: Issuing an RFQ allows buyers to compare prices and terms from multiple suppliers, facilitating better purchasing decisions. -
Incoterms (International Commercial Terms)
– Definition: A set of internationally recognized rules that define the responsibilities of buyers and sellers regarding the transportation and delivery of goods.
– Relevance: Familiarity with Incoterms helps buyers understand shipping costs, risks, and responsibilities, which is particularly important for international transactions. -
Lead Time
– Definition: The amount of time it takes from placing an order to receiving the product.
– Relevance: Understanding lead times aids in project planning and ensures that tools and backpacks are available when needed, preventing delays in operations. -
Warranty
– Definition: A guarantee provided by the manufacturer regarding the quality and longevity of the product.
– Relevance: A robust warranty can indicate the manufacturer’s confidence in their product and provide buyers with assurance against defects, which is particularly valuable in B2B transactions.
By grasping these technical properties and trade terms, international B2B buyers can make more informed decisions when sourcing tool backpacks, ultimately enhancing operational efficiency and cost-effectiveness.
Navigating Market Dynamics, Sourcing Trends, and Sustainability in the tool backpack Sector
Market Overview & Key Trends
The tool backpack market is experiencing robust growth, driven by the increasing demand for portable and organized storage solutions among professionals in construction, electrical, and maintenance sectors. Global drivers such as urbanization, a surge in DIY projects, and the rise of remote work have spurred the need for efficient tool transport. In regions like Africa and South America, infrastructure development is creating new opportunities, while Europe and the Middle East are seeing a shift toward multifunctional designs that cater to both professionals and hobbyists.
Emerging B2B tech trends include the integration of smart technology into tool backpacks, enhancing user experience through features like RFID tracking and built-in charging ports. As buyers increasingly seek customization options, manufacturers are adopting agile production methods to cater to diverse market needs. Additionally, the trend towards online sourcing platforms is transforming the procurement landscape, allowing international buyers to access a wider range of products and suppliers with ease.
International B2B buyers should be aware of the competitive landscape characterized by both established brands and new entrants. Understanding local preferences and regulatory requirements is crucial, particularly in diverse markets like Argentina and Brazil, where consumer behavior and purchasing power can vary significantly. Collaborating with local distributors can enhance market entry strategies and streamline logistics.
Sustainability & Ethical Sourcing in B2B
Sustainability has become a pivotal factor in the tool backpack sector, with increasing pressure from consumers and regulatory bodies for environmentally responsible practices. The environmental impact of production processes, including resource extraction and waste generation, necessitates a commitment to sustainable materials and manufacturing methods. B2B buyers should prioritize suppliers that demonstrate transparency in their supply chains and adhere to eco-friendly practices.
Ethical sourcing is equally important, with an emphasis on fair labor practices and community impact. Buyers can enhance their brand reputation by partnering with manufacturers who hold recognized certifications such as Fair Trade, Global Organic Textile Standard (GOTS), and OEKO-TEX. These certifications not only ensure compliance with ethical standards but also resonate with environmentally conscious consumers.
Investing in ‘green’ materials, such as recycled fabrics and biodegradable components, can significantly reduce the carbon footprint of tool backpacks. By advocating for sustainable practices and ethical sourcing, B2B buyers can differentiate their offerings in a competitive market while contributing to a more sustainable future.
Brief Evolution/History
The evolution of tool backpacks can be traced back to the increasing complexity of tools and the need for effective transport solutions. Initially designed for construction workers, these backpacks have transitioned into multifunctional carriers that cater to a broad audience, including electricians, plumbers, and DIY enthusiasts. Over the years, advancements in materials and ergonomic designs have improved comfort and functionality, making tool backpacks a staple in both professional and personal settings.
As consumer preferences have shifted towards sustainability and multifunctionality, manufacturers have adapted by introducing innovative designs that meet these demands. This evolution reflects the broader trends in the B2B market, where adaptability and responsiveness to consumer needs are essential for long-term success.
Related Video: International Trade 101 | Economics Explained
Frequently Asked Questions (FAQs) for B2B Buyers of tool backpack
-
What key factors should I consider when vetting suppliers for tool backpacks?
When vetting suppliers, prioritize their experience in manufacturing tool backpacks, certifications (like ISO or CE), and the quality of materials used. Request samples to assess craftsmanship and durability. Additionally, investigate their production capacity, lead times, and past client reviews to gauge reliability. Ensure they have a clear understanding of international trade regulations and can navigate logistics effectively, especially if you’re sourcing from regions with different standards. -
Can I customize tool backpacks to meet specific needs for my business?
Yes, many manufacturers offer customization options for tool backpacks, including color, size, pocket configurations, and branding (like logos). When discussing customization, provide detailed specifications and ask for a tech pack to ensure clarity. Keep in mind that extensive customization might affect the minimum order quantities (MOQs) and lead times, so it’s essential to communicate your requirements early in the negotiation process. -
What are the typical minimum order quantities (MOQs) and lead times for tool backpacks?
MOQs for tool backpacks can vary significantly based on the supplier and the complexity of your order. Generally, MOQs range from 100 to 1,000 units. Lead times can also differ, typically ranging from 30 to 90 days, depending on the supplier’s capacity and your customization needs. Always confirm these details upfront to avoid unexpected delays and costs in your supply chain. -
What payment methods are commonly accepted when sourcing tool backpacks?
Common payment methods include bank transfers, letters of credit, PayPal, and escrow services. Each option has its advantages and disadvantages in terms of security and transaction fees. For larger orders, consider using letters of credit to protect your investment. Establish clear payment terms before finalizing contracts, including deposits and payment schedules, to ensure a smooth transaction process.
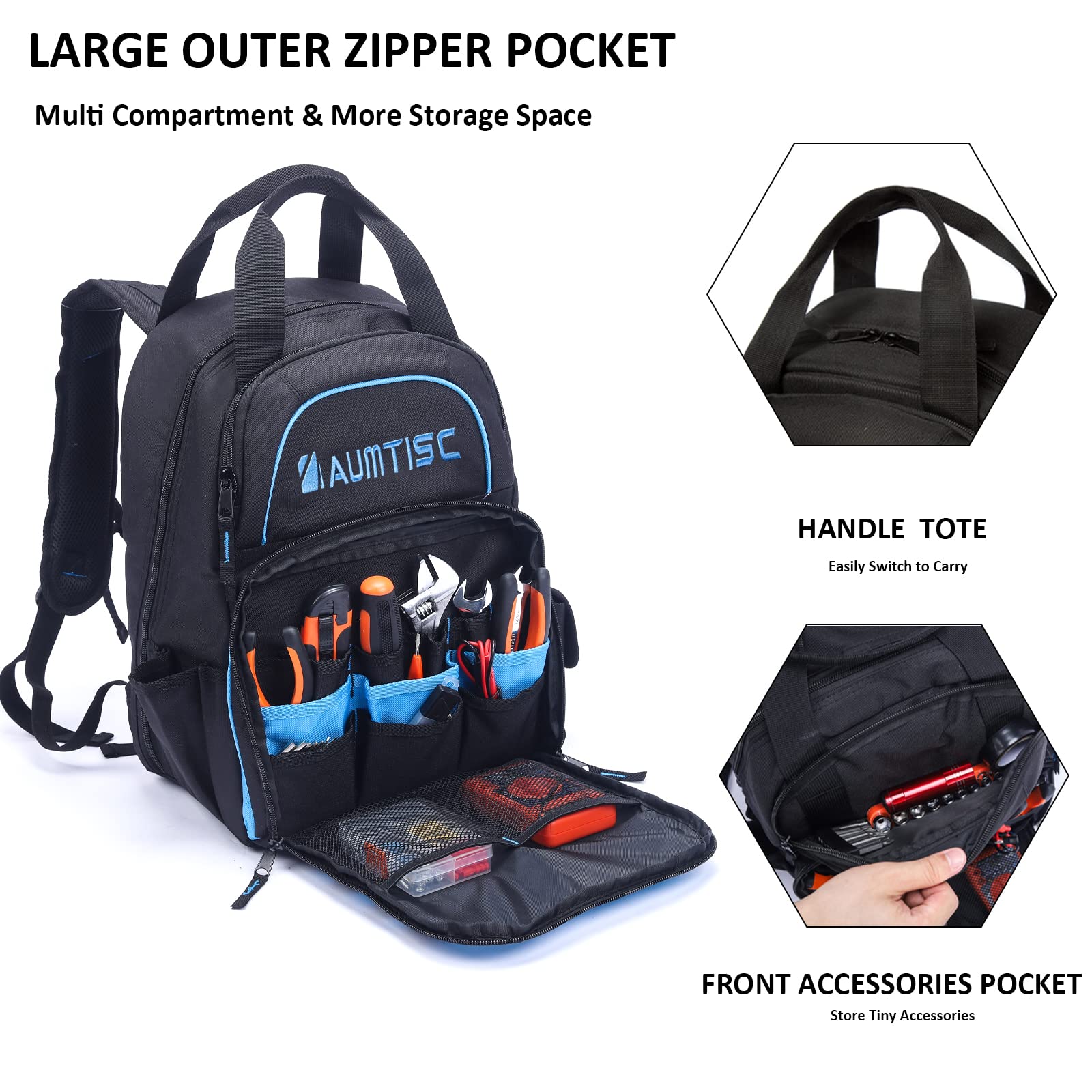
Illustrative Image (Source: Google Search)
-
How can I ensure quality assurance (QA) for my tool backpack orders?
To ensure quality, request samples before placing large orders and conduct a thorough inspection upon arrival. It’s advisable to establish a QA process that includes regular inspections during production and pre-shipment checks. Additionally, ask suppliers for their quality control certifications and whether they can provide third-party inspection reports. This proactive approach helps mitigate risks of defects and ensures product consistency. -
What certifications should I look for in tool backpack suppliers?
Key certifications to consider include ISO 9001 for quality management systems, ISO 14001 for environmental management, and CE marking for compliance with EU safety standards. These certifications indicate that suppliers adhere to international quality and safety norms. In regions like Africa and South America, also check for local certifications that may impact your business operations and compliance. -
How should I handle logistics when importing tool backpacks?
When importing tool backpacks, collaborate with a reliable freight forwarder who understands international shipping regulations. Discuss shipping options (air vs. sea), customs clearance, and duties to avoid unexpected costs. Ensure you have all necessary documentation, such as commercial invoices and packing lists, to facilitate a smooth import process. Planning logistics in advance can significantly reduce delays and enhance supply chain efficiency. -
What steps should I take if a dispute arises with a supplier?
In case of a dispute, first attempt to resolve the issue amicably through direct communication. Document all correspondence and agreements to have a clear record. If informal negotiations fail, consult your contract for dispute resolution mechanisms, such as mediation or arbitration. It’s wise to seek legal advice, especially when dealing with international suppliers, as local laws and regulations can vary significantly.
Strategic Sourcing Conclusion and Outlook for tool backpack
Strategic sourcing in the realm of tool backpacks is essential for international B2B buyers aiming to optimize their procurement processes. By emphasizing the importance of detailed specifications, such as those outlined in a tech pack, businesses can prevent costly miscommunications and production delays. A well-defined tech pack not only streamlines manufacturing but also ensures quality and consistency across multiple production runs, crucial for maintaining brand integrity.
Moreover, understanding the environmental and social impact of sourcing decisions can enhance a company’s reputation, especially in markets that prioritize sustainability. As buyers from Africa, South America, the Middle East, and Europe navigate diverse supply chains, adopting a strategic approach can yield significant cost savings and operational efficiencies.
Looking ahead, the demand for versatile and durable tool backpacks will continue to rise. Buyers should engage with suppliers who demonstrate adaptability and innovation in their offerings. By investing in relationships with reliable manufacturers and prioritizing transparent communication, international B2B buyers can secure the best products while fostering sustainable practices. Take action now—evaluate your sourcing strategy and leverage the insights shared to ensure your tool backpack procurement aligns with your business goals.