Master Sourcing Strategies for Backpack Rabbit: Boost Your
Guide to Backpack Rabbit
- Introduction: Navigating the Global Market for backpack rabbit
- Understanding backpack rabbit Types and Variations
- Key Industrial Applications of backpack rabbit
- Strategic Material Selection Guide for backpack rabbit
- In-depth Look: Manufacturing Processes and Quality Assurance for backpack rabbit
- Comprehensive Cost and Pricing Analysis for backpack rabbit Sourcing
- Spotlight on Potential backpack rabbit Manufacturers and Suppliers
- Essential Technical Properties and Trade Terminology for backpack rabbit
- Navigating Market Dynamics, Sourcing Trends, and Sustainability in the backpack rabbit Sector
- Frequently Asked Questions (FAQs) for B2B Buyers of backpack rabbit
- Strategic Sourcing Conclusion and Outlook for backpack rabbit
Introduction: Navigating the Global Market for backpack rabbit
Navigating the global market for “backpack rabbit” presents a unique opportunity for international B2B buyers, particularly in regions such as Africa, South America, the Middle East, and Europe. As consumer demand for functional and stylish backpacks grows, understanding the nuances of sourcing these products becomes critical. “Backpack rabbit,” a term that encapsulates a range of innovative and versatile backpacks, is poised to capture the attention of businesses looking to enhance their offerings.
This comprehensive guide will delve into the essential aspects of sourcing and manufacturing “backpack rabbit,” including the various types available, the materials that define quality, and the manufacturing processes that ensure durability. We will also discuss best practices in quality control, strategies for selecting reliable suppliers, and insights into pricing structures in the market.
By equipping yourself with this knowledge, you will be empowered to make informed sourcing decisions that align with your business objectives. Whether you are a retailer in the UK or a wholesaler in Argentina, understanding the dynamics of the backpack market will enable you to select products that not only meet quality standards but also resonate with your target audience. Explore the following sections to uncover actionable insights that will enhance your sourcing strategies and drive your business forward in this competitive landscape.
Understanding backpack rabbit Types and Variations
Type Name | Key Distinguishing Features | Primary B2B Applications | Brief Pros & Cons for Buyers |
---|---|---|---|
Daypack | Compact size, minimal features, lightweight | Retail, schools, outdoor activities | Pros: Affordable, versatile; Cons: Limited capacity |
Hiking Backpack | Enhanced durability, ergonomic design, hydration systems | Outdoor retail, adventure tourism | Pros: Comfortable for long use; Cons: Can be expensive |
Travel Backpack | Multiple compartments, security features, laptop sleeves | E-commerce, travel agencies | Pros: Organized, functional; Cons: Bulky for some users |
Diaper Backpack | Specialized pockets, easy access, often waterproof | Baby product retailers, e-commerce | Pros: Practical for parents; Cons: Niche market |
Tactical Backpack | Heavy-duty materials, modular design, military-style | Law enforcement, outdoor survival gear | Pros: Highly durable, customizable; Cons: Heavier than others |
Daypack
Daypacks are designed for short trips and everyday use, making them a popular choice for retailers targeting students and casual hikers. Their lightweight and compact design allows for easy portability, catering to buyers looking for cost-effective solutions. When sourcing daypacks, consider the material quality and stitching to ensure durability, as these factors directly impact customer satisfaction.
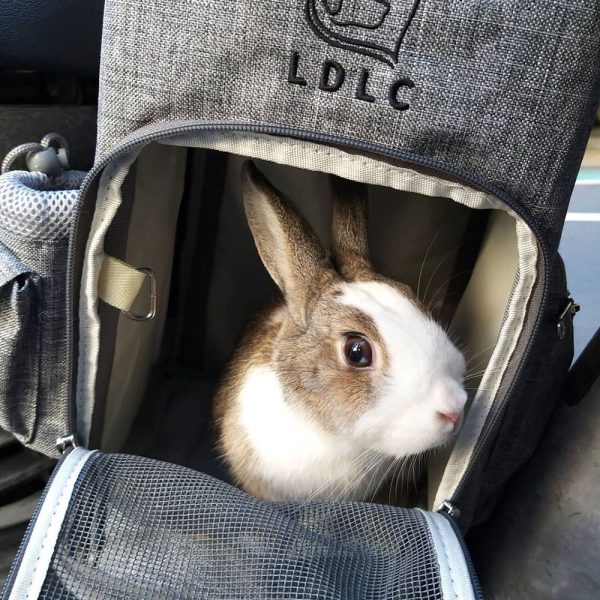
Illustrative Image (Source: Google Search)
Hiking Backpack
Hiking backpacks are built to withstand rugged conditions, featuring ergonomic designs that distribute weight evenly. They often include hydration systems and multiple pockets for organization, making them ideal for outdoor retailers and adventure tourism businesses. Buyers should prioritize suppliers who offer durability testing and ergonomic designs to meet the demands of serious hikers.
Travel Backpack
Travel backpacks are characterized by their multiple compartments, security features, and dedicated laptop sleeves, appealing to e-commerce platforms and travel agencies. Their organizational capabilities make them a favorite among frequent travelers. B2B buyers should assess the quality of zippers and locks, as these are critical for the safety of personal belongings during transit.
Diaper Backpack
Diaper backpacks are designed with parents in mind, featuring specialized pockets for baby essentials and easy access compartments. They are increasingly popular among baby product retailers and e-commerce sellers. When sourcing these backpacks, consider the waterproof materials and ease of cleaning, as these features significantly enhance user experience and satisfaction.
Tactical Backpack
Tactical backpacks are crafted from heavy-duty materials and often feature a modular design for customization. They are primarily used in law enforcement and outdoor survival scenarios, making them suitable for specialized retailers. Buyers should focus on suppliers who can provide evidence of durability tests and offer a range of customization options, ensuring the backpacks meet specific operational needs.
Related Video: Large Language Models (LLMs) – Everything You NEED To Know
Key Industrial Applications of backpack rabbit
Industry/Sector | Specific Application of backpack rabbit | Value/Benefit for the Business | Key Sourcing Considerations for this Application |
---|---|---|---|
Education | Student backpacks with specialized compartments | Enhanced organization and functionality for students | Material durability, ergonomic design, customization options |
Outdoor Recreation | Hiking and camping gear | Increased customer satisfaction with durable products | Weather-resistant materials, lightweight design, comfort features |
Logistics & Transport | Carrying equipment for field personnel | Improved mobility and efficiency in operations | Load capacity, easy access pockets, robust stitching |
Retail | Branded promotional backpacks | Strengthened brand visibility and customer loyalty | Custom branding options, quality assurance, design flexibility |
Emergency Services | Rapid response backpacks for first responders | Quick access to essential gear during emergencies | Lightweight materials, high visibility colors, compartmentalization |
Education
In the education sector, backpack rabbit is utilized to create student backpacks with specialized compartments tailored for books, laptops, and personal items. This design not only enhances organization but also caters to the diverse needs of students, including those attending schools in regions like Africa and South America where access to resources may be limited. Buyers should prioritize sourcing durable materials and ergonomic designs to ensure comfort during daily commutes.
Outdoor Recreation
For outdoor recreation, backpack rabbit serves as an ideal solution for producing hiking and camping gear. These backpacks are designed to withstand rugged conditions and provide ample storage for essential gear. Businesses in this sector benefit from increased customer satisfaction due to the durability and functionality of the products. When sourcing, it’s crucial to focus on weather-resistant materials and lightweight designs that do not compromise on comfort.
Logistics & Transport
In logistics and transport, backpack rabbit is applied in creating backpacks for field personnel who require mobility while carrying essential equipment. These backpacks facilitate improved efficiency and organization during operations. B2B buyers should consider aspects such as load capacity, easy access pockets, and robust stitching to ensure the backpacks can withstand the demands of the job, especially in challenging environments found in regions like the Middle East.
Retail
In the retail industry, backpack rabbit can be leveraged to produce branded promotional backpacks. These backpacks not only serve as functional items but also enhance brand visibility and foster customer loyalty. When sourcing, businesses should look for customization options that allow for unique branding, along with quality assurance to maintain the integrity of the product. This is particularly important in competitive markets in Europe and South America.
Emergency Services
The application of backpack rabbit in emergency services focuses on developing rapid response backpacks for first responders. These backpacks are designed for quick access to essential gear during emergencies, making them a critical tool for saving lives. Key sourcing considerations include lightweight materials, high visibility colors, and efficient compartmentalization to ensure that responders can act swiftly and effectively in critical situations.
Related Video: Introduction to Uses and Gratifications Theory
Strategic Material Selection Guide for backpack rabbit
When selecting materials for the manufacturing of “backpack rabbit,” it is essential for international B2B buyers to understand the properties, advantages, and limitations of various materials. This knowledge will aid in making informed decisions that align with product performance, cost, and market preferences. Below, we analyze four common materials used in backpack production, focusing on their suitability for the backpack rabbit.
1. Nylon
Key Properties: Nylon is known for its high tensile strength, abrasion resistance, and lightweight nature. It performs well under various temperatures and is generally resistant to mildew and mold.
Pros & Cons: The durability of nylon makes it an excellent choice for backpacks that undergo heavy use. However, it can be more expensive than other materials, and its manufacturing process can be complex due to the need for specialized equipment.
Impact on Application: Nylon is compatible with various media, including water-resistant coatings, making it suitable for outdoor and travel backpacks.
Considerations for International Buyers: Buyers from regions like Africa and South America should consider the availability of nylon and its cost implications. Compliance with international standards such as ASTM and ISO for textile products is crucial to ensure quality and safety.
2. Polyester
Key Properties: Polyester is highly resistant to shrinking and stretching, and it maintains its shape well. It offers good UV resistance and is less prone to fading compared to nylon.
Pros & Cons: Polyester is generally more affordable than nylon, making it a cost-effective option for manufacturers. However, it is less durable than nylon and may not perform as well under extreme conditions.
Impact on Application: Polyester is suitable for everyday backpacks and school bags. Its compatibility with various dyes allows for vibrant colors and patterns.
Considerations for International Buyers: Buyers in Europe may prefer polyester for its eco-friendly options, as recycled polyester is increasingly available. Compliance with European Union regulations on textiles can also affect sourcing decisions.
3. Canvas
Key Properties: Canvas is a heavy-duty fabric known for its durability and resistance to wear and tear. It provides good breathability and is often treated for water resistance.
Pros & Cons: The natural look and feel of canvas appeal to many consumers, making it popular for fashion-oriented backpacks. However, it can be heavier than synthetic materials and may require additional treatments to enhance water resistance.
Impact on Application: Canvas is ideal for casual and lifestyle backpacks, particularly those targeting eco-conscious consumers.
Considerations for International Buyers: Buyers from the Middle East may need to consider the climate impact on canvas durability, as extreme heat can affect its longevity. Compliance with local textile standards, such as those set by the Gulf Cooperation Council (GCC), is also important.
4. Leather
Key Properties: Leather is known for its luxurious appearance and durability. It offers good resistance to wear and can withstand various environmental conditions.
Pros & Cons: Leather backpacks are often perceived as high-end products, appealing to a premium market. However, leather can be expensive and requires more maintenance than synthetic options.
Impact on Application: Leather is suitable for fashion-forward and professional backpacks, often used in business settings.
Considerations for International Buyers: Buyers in Europe may face stricter regulations regarding leather sourcing and animal welfare, necessitating compliance with EU legislation. Additionally, understanding the sourcing practices and environmental impact of leather production is critical.
Summary Table
Material | Typical Use Case for backpack rabbit | Key Advantage | Key Disadvantage/Limitation | Relative Cost (Low/Med/High) |
---|---|---|---|---|
Nylon | Outdoor and travel backpacks | High durability and abrasion resistance | Higher cost, complex manufacturing | High |
Polyester | Everyday and school backpacks | Cost-effective, good UV resistance | Less durable than nylon | Medium |
Canvas | Casual and lifestyle backpacks | Natural look, good durability | Heavier, requires treatment for water resistance | Medium |
Leather | Fashion-forward and professional backpacks | Luxurious appearance, durable | Expensive, requires maintenance | High |
This strategic material selection guide provides essential insights for B2B buyers in different regions, helping them make informed decisions that align with their market needs and compliance requirements.
In-depth Look: Manufacturing Processes and Quality Assurance for backpack rabbit
The manufacturing process for backpacks, including models like the “backpack rabbit,” involves multiple key stages, each requiring careful attention to detail and quality assurance. For international B2B buyers, understanding these processes can lead to more informed sourcing decisions and better product outcomes.
Manufacturing Process Stages
1. Material Preparation
The first step in the manufacturing process is sourcing and preparing the materials. High-quality materials are essential for the durability and functionality of backpacks. Buyers should focus on:
- Sourcing Quality Fabrics: Look for materials like nylon, polyester, or canvas, which provide strength and resistance to wear. Specialized fabrics such as waterproof or UV-resistant options can also enhance product appeal.
- Testing Materials: Request samples and ensure they undergo rigorous testing for abrasion resistance, tear strength, and colorfastness. This helps prevent issues like color fading or tearing in the final product.
2. Forming
Once materials are sourced, they are transformed into usable components through various techniques:
- Pattern Creation: CAD software is often used to design and create patterns for cutting. This ensures accuracy in dimensions and reduces waste.
- Fabric Cutting: Automated cutting machines may be employed for larger orders, while manual cutting is suitable for smaller batches. Precision is crucial to avoid inconsistencies.
3. Assembly
The assembly stage is where all components come together to form the final product:
- Sewing Techniques: Skilled workers use industrial sewing machines to assemble the backpack. Techniques like double-stitching at stress points, bar tacking, and reinforcing seams are vital for durability.
- Quality Checks: Implement inline inspections during the assembly to catch defects early. This includes checking for proper alignment of zippers, buckles, and straps.
4. Finishing
The final stage involves adding finishing touches to ensure the product is ready for the market:
- Final Assembly: Components such as zippers, straps, and buckles are attached, and the backpack is inverted to hide seams.
- Quality Control: Perform final inspections to check for any defects, ensuring that all backpacks meet the required specifications and quality standards.
Quality Assurance Protocols
Quality assurance is essential to maintain product integrity and brand reputation. International buyers should familiarize themselves with various standards and practices.
Relevant International Standards
- ISO 9001: This standard ensures quality management systems are in place, which helps improve overall efficiency and customer satisfaction.
- CE Marking: Particularly important for products sold in the European market, CE marking indicates compliance with health, safety, and environmental protection standards.
- API Standards: Though more common in industrial applications, some backpack manufacturers may adhere to these standards to assure quality in specific contexts.
Quality Control Checkpoints
To ensure product quality at every stage of manufacturing, establish the following checkpoints:
- Incoming Quality Control (IQC): Inspect materials upon arrival to ensure they meet specifications before production begins.
- In-Process Quality Control (IPQC): Conduct checks during the manufacturing process, focusing on key assembly stages to catch issues early.
- Final Quality Control (FQC): Perform thorough inspections of the finished product to ensure all backpacks meet design and quality specifications before shipping.
Common Testing Methods
B2B buyers should insist on the following testing methods to verify product quality:
- Durability Tests: Assess the fabric’s resistance to tearing and abrasion.
- Water Resistance Tests: Ensure materials can withstand exposure to moisture without compromising integrity.
- Comfort Tests: Evaluate ergonomic features, such as strap design and padding, to ensure user comfort.
Verifying Supplier Quality Control
To mitigate risks associated with poor-quality products, B2B buyers must verify suppliers’ quality control measures:
- Conduct Audits: Regularly audit suppliers’ facilities to ensure adherence to quality standards. This includes reviewing processes, materials, and the overall production environment.
- Request Quality Reports: Ask suppliers for documentation of quality checks, testing results, and compliance with international standards.
- Third-Party Inspections: Engage third-party inspection services to conduct unbiased assessments of the manufacturing process and final products.
QC and Certification Nuances for International Buyers
B2B buyers from Africa, South America, the Middle East, and Europe should be aware of specific nuances when it comes to quality control and certification:
- Regulatory Compliance: Different regions may have varying regulations regarding product safety and quality. Buyers should familiarize themselves with local laws and ensure suppliers comply.
- Cultural Considerations: Understand cultural differences that may affect communication and expectations regarding quality. Building strong relationships with suppliers can lead to better compliance with quality standards.
- Supply Chain Logistics: International shipping can pose challenges in maintaining quality. Buyers should discuss packaging and handling practices with suppliers to minimize damage during transit.
By comprehensively understanding the manufacturing processes and quality assurance practices involved in sourcing backpacks like the “backpack rabbit,” international B2B buyers can make informed decisions that enhance product quality and customer satisfaction.
Related Video: How a Backpack is Made : Every Step on the Production Line
Comprehensive Cost and Pricing Analysis for backpack rabbit Sourcing
When sourcing ‘backpack rabbit’, understanding the comprehensive cost structure is essential for effective budget planning and price negotiation. The following breakdown outlines the key components involved in the cost structure and the various factors that influence pricing.
Cost Components
-
Materials
The choice of materials significantly impacts the overall cost. High-quality fabrics (such as ripstop nylon or waterproof materials) and durable hardware (like zippers and buckles) can raise initial expenditures but may result in lower return rates and increased customer satisfaction. -
Labor
Labor costs can vary widely depending on the region and the complexity of the manufacturing process. Countries with lower labor costs may offer attractive pricing, but this often correlates with quality risks. It is crucial to balance labor costs with the skill level of the workforce to ensure high-quality production. -
Manufacturing Overhead
This includes costs associated with factory operations, such as utilities, equipment maintenance, and general administrative expenses. Understanding a supplier’s overhead structure can help in assessing their pricing. -
Tooling
If custom tooling is required for specific designs, this can add to the initial investment. Tooling costs are typically amortized over the production run, so larger orders can lead to reduced costs per unit. -
Quality Control (QC)
Implementing stringent quality control measures can incur additional costs but is vital for maintaining product standards. Investing in QC helps avoid costly returns and damages to brand reputation. -
Logistics
Shipping and handling costs should not be overlooked. These costs can vary based on the shipping method, distance, and logistics provider. Understanding Incoterms is essential, as they determine who bears the costs and risks during transportation. -
Margin
Finally, suppliers will add their profit margin to the cost structure. This margin can vary depending on the supplier’s market position, quality assurances, and services offered.
Price Influencers
Several factors can influence the pricing of backpacks:
-
Volume/MOQ: Larger orders often qualify for lower per-unit prices due to economies of scale. Negotiating minimum order quantities (MOQs) can yield better pricing.
-
Specifications/Customization: Unique designs or custom features can increase costs. Buyers should weigh the benefits of customization against potential price increases.
-
Materials: The choice of high-quality materials can lead to higher initial costs but often results in better long-term value and customer satisfaction.
-
Quality Certifications: Products that meet specific quality standards or certifications may command higher prices due to the assurance of quality.
-
Supplier Factors: Established suppliers with a strong reputation may charge more due to their reliability and quality assurance processes.
-
Incoterms: Understanding the shipping terms can help manage costs effectively. Terms like FOB (Free on Board) can shift some shipping costs to the buyer, while DDP (Delivered Duty Paid) includes all costs up to delivery.
Buyer Tips
-
Negotiate Wisely: Leverage your purchasing power, especially if you are placing large orders. Don’t hesitate to negotiate prices and terms with suppliers.
-
Focus on Cost-Efficiency: Consider the Total Cost of Ownership (TCO), which includes not only the purchase price but also logistics, handling, and potential returns.
-
Understand Pricing Nuances: International buyers should be aware of local market conditions, currency fluctuations, and trade tariffs that can affect pricing.
-
Conduct Supplier Research: Vet potential suppliers thoroughly to ensure they can meet your quality and delivery expectations. Request samples and quality certifications before finalizing contracts.
-
Plan for Hidden Costs: Be aware of additional costs that may arise, such as customs duties or unexpected logistics fees, to avoid budget overruns.
Disclaimer
Prices can vary significantly based on market conditions, supplier capabilities, and specific buyer requirements. The insights provided are intended as a guideline and should be adjusted according to individual circumstances and negotiations.
Spotlight on Potential backpack rabbit Manufacturers and Suppliers
This section offers a look at a few manufacturers active in the ‘backpack rabbit’ market. This is a representative sample for illustrative purposes; B2B buyers must conduct their own extensive due diligence before any engagement. Information is synthesized from public sources and general industry knowledge.
Essential Technical Properties and Trade Terminology for backpack rabbit
Critical Technical Properties of Backpack Rabbit
Understanding the essential technical properties of backpacks is crucial for B2B buyers looking to ensure product quality and consumer satisfaction. Here are some critical specifications to consider:
1. Material Grade
The material grade refers to the quality and durability of the fabrics used in manufacturing the backpack. Common materials include nylon, polyester, and canvas, each offering different levels of strength, weight, and water resistance.
B2B Importance: Selecting high-grade materials is essential to ensure longevity and customer satisfaction, reducing returns and enhancing brand reputation.
2. Tolerance
Tolerance defines the allowable deviation in dimensions and manufacturing processes. For backpacks, this may pertain to the size of pockets, strap lengths, and overall dimensions.
B2B Importance: Maintaining tight tolerances ensures that all components fit together seamlessly, which is critical for functionality and aesthetics. Poor tolerances can lead to assembly issues and affect product performance.
3. Load Capacity
Load capacity indicates the maximum weight a backpack can safely carry without compromising its structural integrity. This specification is vital for backpacks designed for specific uses, such as hiking or travel.
B2B Importance: Understanding load capacity helps buyers select products that meet their target market’s needs, ensuring user safety and satisfaction.
4. Stitching Techniques
The type and quality of stitching used in backpack production, such as double-stitching or bar tacking, can significantly affect durability.
B2B Importance: Quality stitching minimizes the risk of seams breaking under stress, which is particularly important for high-use areas such as straps and pockets.
5. Water Resistance Rating
This property indicates how well a backpack can resist water ingress. Ratings are often given in terms of hydrostatic pressure measured in millimeters.
B2B Importance: For buyers targeting outdoor markets, knowing the water resistance rating is crucial for meeting consumer expectations and preventing returns due to moisture damage.
6. Weight
The overall weight of the backpack affects user comfort and usability, especially for travel and outdoor activities.
B2B Importance: Lighter backpacks are often preferred by consumers, especially for hiking or daily commuting, making weight a key factor in product selection.
Common Trade Terminology in Backpack Sourcing
Familiarity with industry jargon is vital for effective communication and negotiation. Here are some common terms that B2B buyers should know:
1. OEM (Original Equipment Manufacturer)
An OEM is a company that produces parts or equipment that may be marketed by another manufacturer. In the backpack industry, this often refers to manufacturers that create backpacks under another brand’s specifications.
Importance: Understanding OEM relationships can help buyers identify manufacturers that can produce custom designs according to their specifications.
2. MOQ (Minimum Order Quantity)
MOQ refers to the smallest quantity of a product that a supplier is willing to sell. This number can vary significantly between manufacturers.
Importance: Knowing the MOQ helps buyers plan their inventory and budget effectively, ensuring that they do not overcommit financially.
3. RFQ (Request for Quotation)
An RFQ is a document sent to suppliers requesting a price quote for specific goods or services.
Importance: Utilizing RFQs allows buyers to compare prices and terms from multiple suppliers, fostering competitive pricing and better procurement decisions.
4. Incoterms
Incoterms (International Commercial Terms) are a set of predefined commercial terms published by the International Chamber of Commerce. They define the responsibilities of buyers and sellers in international transactions.
Importance: Understanding Incoterms helps buyers clarify shipping responsibilities, costs, and risks, which is crucial for smooth international transactions.
5. Lead Time
Lead time is the period between the initiation of a process and its completion. In manufacturing, it often refers to the time taken from placing an order to receiving the finished product.
Importance: Knowing lead times is essential for inventory management and aligning supply with demand, particularly in fast-paced markets.
6. Quality Assurance (QA)
QA refers to the systematic processes and measures taken to ensure that products meet specified quality standards throughout the manufacturing process.
Importance: Implementing QA practices helps buyers ensure that the backpacks sourced meet their quality expectations, reducing the risk of defects and enhancing customer satisfaction.
By understanding these technical properties and trade terms, B2B buyers can make more informed decisions, ensuring that they source high-quality backpacks that meet market demands and customer expectations.
Navigating Market Dynamics, Sourcing Trends, and Sustainability in the backpack rabbit Sector
Market Overview & Key Trends
The global backpack market is witnessing significant growth, driven by increasing demand for functional and fashionable options among consumers. B2B buyers, particularly in regions like Africa, South America, the Middle East, and Europe, should note the following key trends shaping the landscape:
-
Digital Transformation: The rise of e-commerce platforms is revolutionizing how backpacks are sourced. Buyers can now leverage technologies like AI and big data analytics to better understand market demands and consumer preferences, leading to more informed purchasing decisions.
-
Customization and Personalization: There is a growing trend towards offering customized backpacks, catering to niche markets such as outdoor enthusiasts and urban commuters. B2B buyers should consider suppliers that provide flexible manufacturing options to meet this demand.
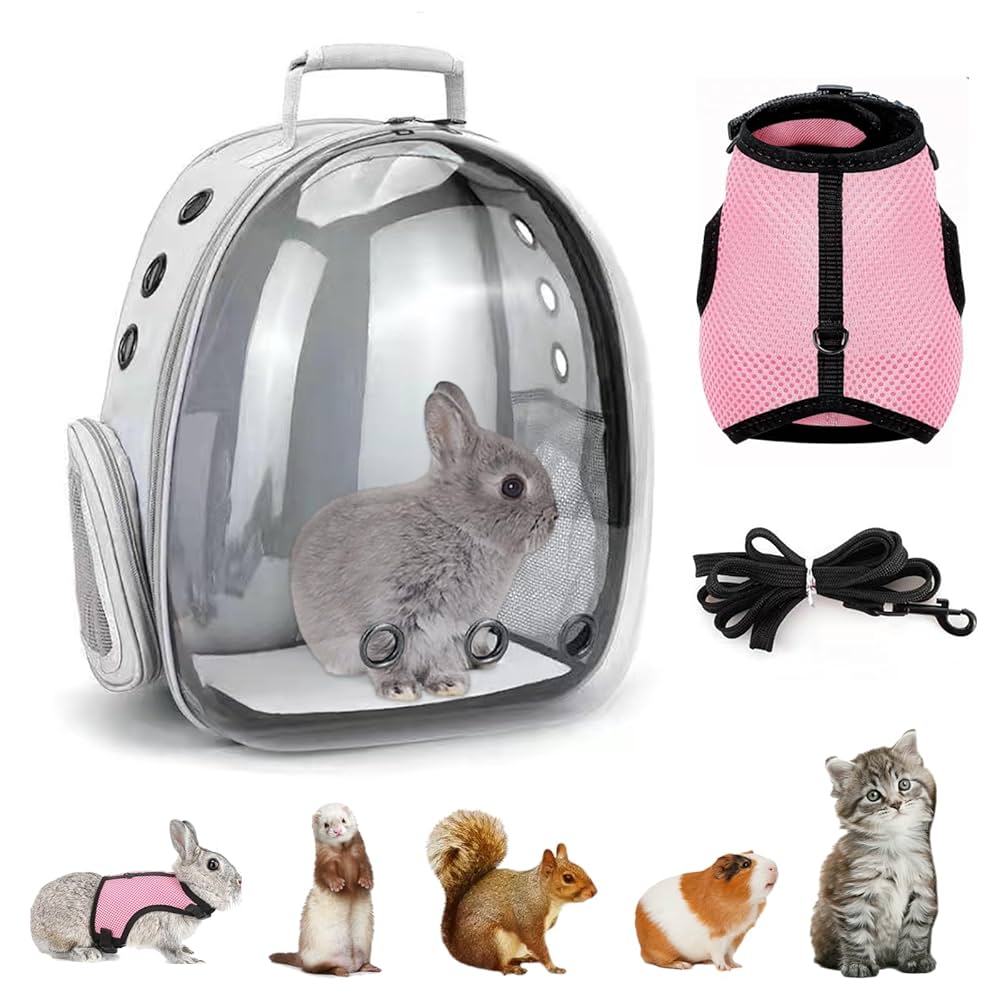
Illustrative Image (Source: Google Search)
-
Sustainable Practices: Increasing awareness about environmental issues is pushing manufacturers to adopt sustainable practices. Buyers are now prioritizing suppliers that utilize eco-friendly materials and processes, reflecting a broader shift towards sustainability in purchasing decisions.
-
Quality Assurance: As competition intensifies, the emphasis on quality has never been more critical. Buyers must engage with suppliers who demonstrate robust quality control processes, ensuring that the products sourced meet the highest standards.
-
Global Supply Chain Resilience: Recent global disruptions have highlighted the need for resilient supply chains. B2B buyers should assess the geographic diversity of their suppliers and consider risk mitigation strategies, such as multi-sourcing, to avoid potential shortages.
These trends indicate a dynamic market environment that requires B2B buyers to stay informed and agile in their sourcing strategies.
Sustainability & Ethical Sourcing in B2B
Sustainability is becoming a focal point in the backpack industry, with buyers increasingly recognizing the importance of ethical sourcing. The environmental impact of production processes, including pollution and waste generation, necessitates a shift towards more responsible practices. B2B buyers can enhance their brand reputation by prioritizing suppliers committed to sustainable practices.
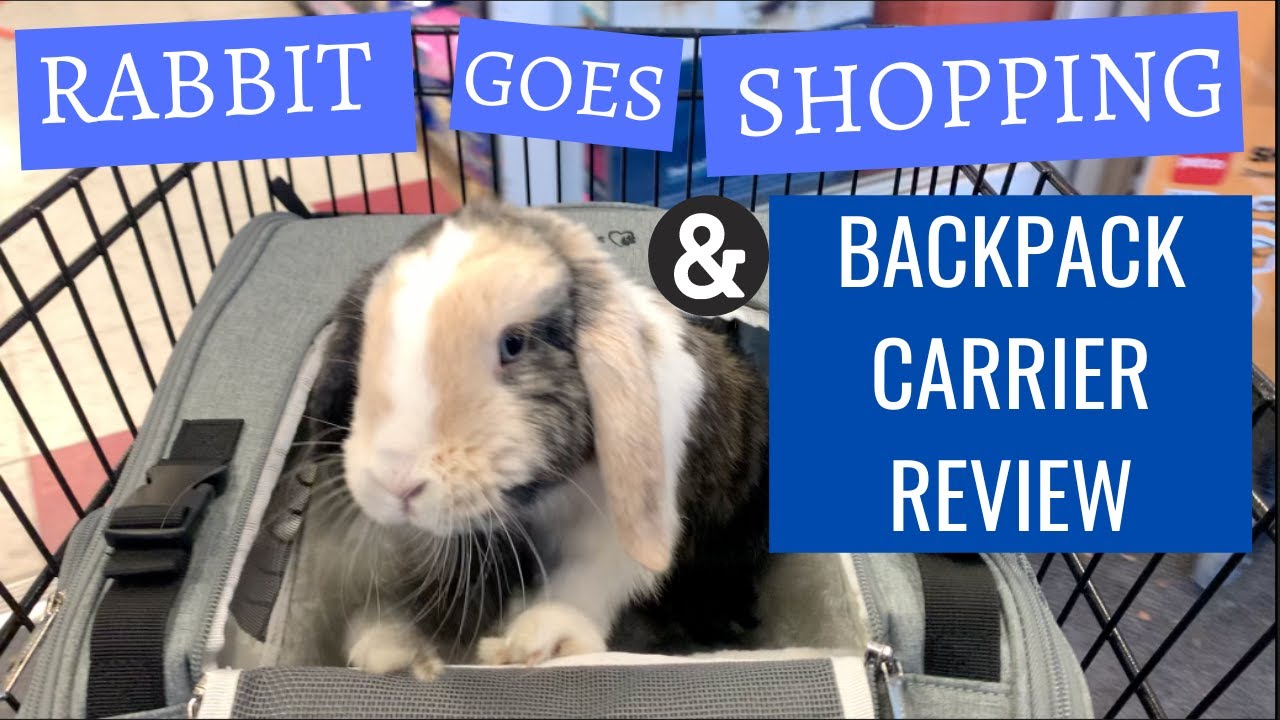
Illustrative Image (Source: Google Search)
-
Green Certifications: Look for suppliers that hold certifications such as Global Organic Textile Standard (GOTS) or OEKO-TEX Standard 100. These certifications ensure that materials are sourced and processed in an environmentally friendly manner.
-
Eco-Friendly Materials: Materials such as recycled polyester, organic cotton, and biodegradable fabrics are gaining traction. Incorporating these materials not only reduces environmental impact but also appeals to a growing segment of eco-conscious consumers.
-
Transparency in Supply Chains: Ethical sourcing involves transparency at every stage of production. B2B buyers should demand visibility into their suppliers’ supply chains, ensuring that labor practices are fair and that workers are treated ethically.
-
Lifecycle Considerations: Buyers should consider the entire lifecycle of the backpack, from production to disposal. Encouraging suppliers to adopt circular economy principles—such as designing for recyclability—can significantly reduce the environmental footprint.
By integrating sustainability into sourcing strategies, B2B buyers can contribute positively to environmental conservation while meeting consumer demand for responsible products.
Brief Evolution/History
The evolution of the backpack market can be traced back to its functional origins in the early 20th century, primarily serving outdoor enthusiasts and military personnel. Over the decades, the backpack has transformed from a utilitarian item into a fashion statement, driven by lifestyle changes and urbanization. The introduction of advanced materials and ergonomic designs in the late 20th century further broadened its appeal, making backpacks suitable for various consumer segments, including students, professionals, and travelers. Today, the market is characterized by a blend of innovation, style, and sustainability, reflecting changing consumer preferences and the growing importance of ethical sourcing. As a B2B buyer, understanding this evolution can provide insights into consumer trends and help inform sourcing decisions.
Related Video: International Trade Explained
Frequently Asked Questions (FAQs) for B2B Buyers of backpack rabbit
-
How do I vet suppliers when sourcing backpacks?
When vetting suppliers for backpacks, prioritize those with a proven track record in quality and reliability. Request references from previous clients and check online reviews. Conduct factory visits, if possible, to assess their production processes and capabilities. Ensure they have necessary certifications, such as ISO or compliance with international standards. Establish communication regarding their quality assurance processes and inquire about their handling of quality issues to gauge responsiveness. -
Can I customize backpack designs for my brand?
Yes, many manufacturers offer customization options, allowing you to tailor designs, colors, and features to fit your brand’s identity. Discuss your specific requirements upfront, including materials, sizes, and any unique functionalities. Be prepared to provide design sketches or specifications. It’s beneficial to work with suppliers who have experience in custom production, as they can guide you through the design process and suggest feasible modifications. -
What are typical minimum order quantities (MOQs) and lead times?
Minimum order quantities can vary widely depending on the manufacturer and the complexity of the design. Generally, MOQs for backpacks may range from 100 to 1000 units. Lead times typically range from 4 to 12 weeks, contingent on the order size and production capacity. Always clarify these details during negotiations and consider placing a smaller initial order to test the market before committing to larger quantities. -
What payment terms should I expect when sourcing internationally?
Payment terms can differ by supplier, but common practices include a deposit (usually 30-50%) upfront and the balance upon completion or prior to shipment. Consider using secure payment methods, such as letters of credit or escrow services, to protect your investment. Ensure clarity on the currency used for transactions and any associated bank fees. Discuss potential discounts for early payments or larger orders to optimize costs. -
How can I ensure quality assurance and compliance with standards?
To ensure quality, request documentation of quality control processes from your supplier, including inspection reports and certifications. Establish a clear agreement on quality standards before production begins. Consider implementing third-party inspections at various production stages to verify compliance with your specifications. Regular communication with the supplier can also help address any concerns proactively and maintain product quality. -
What logistics considerations should I keep in mind when importing backpacks?
When importing backpacks, consider shipping methods (air vs. sea), customs regulations, and potential tariffs. Research logistics providers experienced in international shipping to ensure timely and efficient delivery. Understand the Incoterms (International Commercial Terms) that dictate responsibilities for shipping costs and risks. Plan for potential delays at customs and have contingency plans to mitigate disruptions in your supply chain. -
How do I handle disputes with suppliers?
To handle disputes effectively, maintain open communication with your supplier to address issues as they arise. Document all agreements and communications to provide a clear reference in case of disagreements. If a resolution cannot be reached, consider mediation or arbitration as alternatives to legal action. Understanding the legal framework in the supplier’s country can also help navigate disputes more effectively. -
What certifications should I look for in backpack manufacturers?
Look for certifications that demonstrate compliance with international quality and safety standards, such as ISO 9001 for quality management and OEKO-TEX for textile safety. Certifications related to environmental management (ISO 14001) and ethical labor practices (SA8000) can also be important, particularly for brands focusing on sustainability. Request documentation to verify these certifications and ensure they are current and relevant to your production needs.
Strategic Sourcing Conclusion and Outlook for backpack rabbit
Strategic sourcing for backpacks, particularly in the competitive landscape of international markets, is crucial for ensuring quality and brand reputation. By understanding the common quality issues—such as material defects, stitching problems, and design flaws—B2B buyers can make informed decisions when selecting suppliers. Implementing rigorous testing protocols and demanding transparency from manufacturers not only mitigates risks but also enhances customer satisfaction.
Key Takeaways:
– Prioritize Quality: Invest in materials and craftsmanship to reduce return rates and foster customer loyalty.
– Supplier Assessment: Conduct thorough evaluations of potential suppliers, focusing on their manufacturing capabilities and commitment to quality.
– Proactive Communication: Maintain open lines of communication with suppliers to address any concerns swiftly and effectively.
Looking ahead, the demand for high-quality backpacks is expected to grow, driven by an increasing focus on sustainability and functionality. International B2B buyers from regions like Africa, South America, the Middle East, and Europe should seize this opportunity by leveraging strategic sourcing practices to elevate their product offerings. Embrace innovation and quality to stay competitive, and consider partnering with trusted manufacturers who align with your brand values. Start your journey today by evaluating your sourcing strategies to ensure a successful future in the backpack market.