Master Sourcing Stoney Clover Backpacks: A B2B Buyer’s
Guide to Stoney Clover Backpack
- Introduction: Navigating the Global Market for stoney clover backpack
- Understanding stoney clover backpack Types and Variations
- Key Industrial Applications of stoney clover backpack
- Strategic Material Selection Guide for stoney clover backpack
- In-depth Look: Manufacturing Processes and Quality Assurance for stoney clover backpack
- Comprehensive Cost and Pricing Analysis for stoney clover backpack Sourcing
- Spotlight on Potential stoney clover backpack Manufacturers and Suppliers
- Essential Technical Properties and Trade Terminology for stoney clover backpack
- Navigating Market Dynamics, Sourcing Trends, and Sustainability in the stoney clover backpack Sector
- Frequently Asked Questions (FAQs) for B2B Buyers of stoney clover backpack
- Strategic Sourcing Conclusion and Outlook for stoney clover backpack
Introduction: Navigating the Global Market for stoney clover backpack
In the competitive landscape of international trade, the Stoney Clover backpack stands out as a symbol of quality, customization, and consumer appeal. As a B2B buyer from regions such as Africa, South America, the Middle East, or Europe, understanding the nuances of this product line is critical for capturing market opportunities and driving sales. With a growing demand for fashionable, personalized accessories, the Stoney Clover brand offers a diverse range of styles that can cater to various consumer preferences, making it a lucrative addition to any inventory.
This guide serves as a comprehensive resource for international buyers looking to navigate the complexities of sourcing Stoney Clover backpacks. It covers essential topics, including backpack types and customization options, material sourcing, manufacturing workflows and quality control, supplier vetting strategies, and global pricing factors. Additionally, it provides insights into emerging market trends and consumer behaviors, ensuring that you are well-equipped to make informed purchasing decisions.
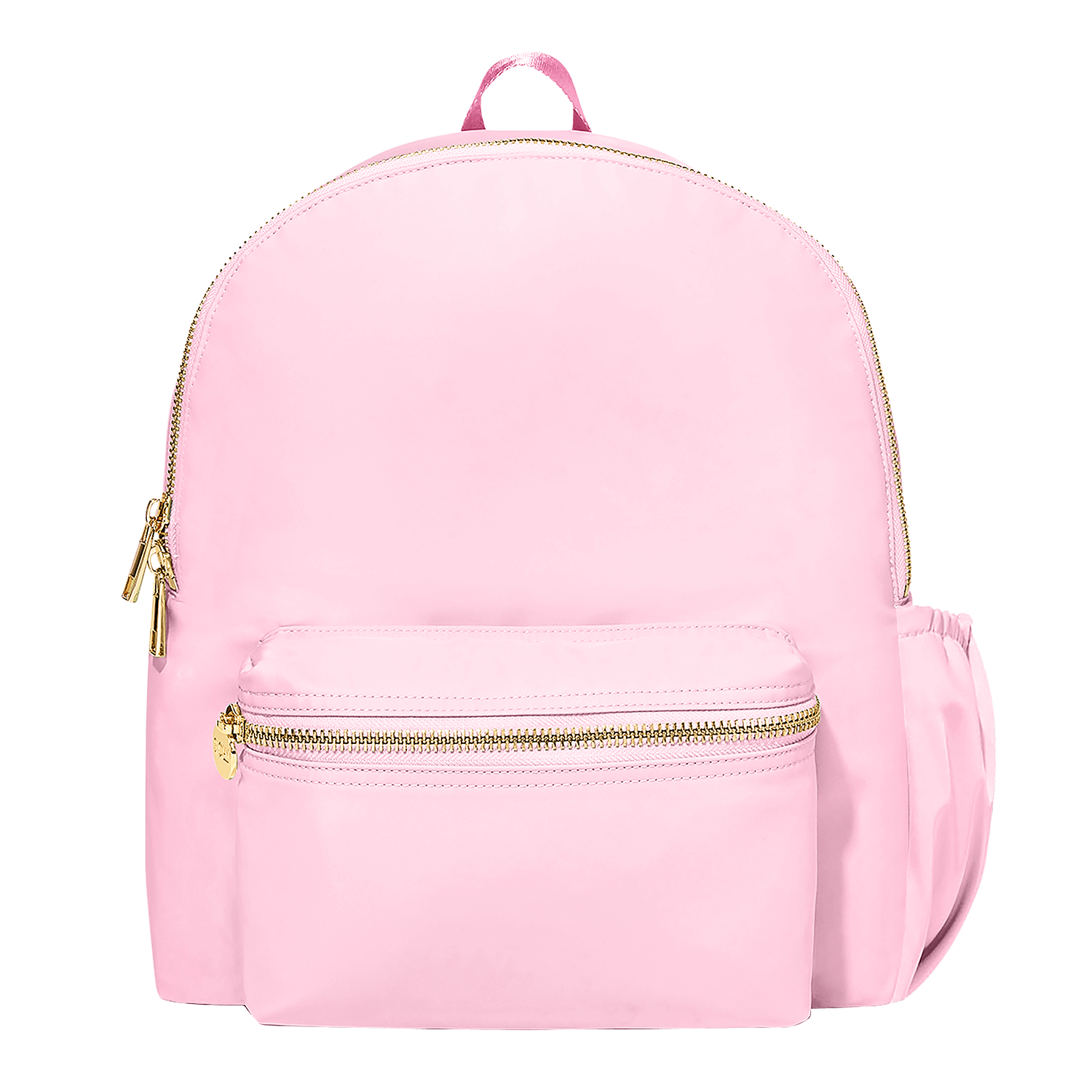
Illustrative Image (Source: Google Search)
By leveraging the actionable insights presented in this guide, B2B buyers will be empowered to minimize risks and maximize profit margins in the highly competitive lifestyle accessories market. Whether you are a retailer in Mexico seeking to expand your product line or a distributor in South Africa aiming to meet rising consumer demands, this resource is designed to facilitate your journey towards successful sourcing of Stoney Clover backpacks.
Understanding stoney clover backpack Types and Variations
Type Name | Key Distinguishing Features | Primary B2B Applications | Brief Pros & Cons for Buyers |
---|---|---|---|
Classic Nylon | Lightweight, water-resistant, vibrant color options | Retail, school supplies, promotions | High demand and lower cost; moderate margins due to competition |
Canvas | Sturdy cotton fabric, customizable with prints | Boutiques, corporate gifts | Eco-friendly; higher sourcing costs and weight |
Leather Accent | Premium leather details, luxurious feel | High-end retail, hospitality | Upscale image and margins; longer lead times and higher costs |
Woven/Limited Edition | Unique fabrics/patterns, seasonal or numbered releases | Special campaigns, collaborations | Exclusivity drives demand; complex inventory management |
Pre-Customized | Ready-made with trendy patches/embroidery | Fast-moving retail, events | High visual impact; less flexibility in inventory mix |
Classic Nylon
Classic nylon Stoney Clover backpacks are characterized by their lightweight and durable design, making them ideal for everyday use. Their vibrant colors and water-resistant properties appeal to a broad market, particularly in regions like Africa and South America where functionality is essential. B2B buyers should focus on ensuring fabric quality and color consistency, as these factors significantly affect customer satisfaction and brand reputation. The lower price point makes them attractive for bulk purchases, especially for school supplies or promotional giveaways.
Canvas
Canvas backpacks offer a robust, eco-friendly alternative with a vintage aesthetic that appeals to boutique retailers and environmentally conscious consumers. The customization options available for prints and logos make them suitable for corporate gifting and branding initiatives, particularly in Europe and the Middle East. However, buyers should be aware that canvas is heavier and may incur higher sourcing costs. Additionally, confirming the fabric’s sustainability credentials can enhance brand image and meet growing consumer demand for eco-friendly products.
Leather Accent
The leather-accented Stoney Clover backpack combines the durability of nylon or canvas with the luxurious appeal of leather details. This type is particularly suited for high-end retail and hospitality applications, where an upscale presentation is crucial. B2B buyers should consider the implications of sourcing genuine leather versus synthetic alternatives, as this affects pricing and compliance with regional regulations. The longer lead times associated with this type can pose challenges, so effective planning and supplier communication are essential.
Woven/Limited Edition
Woven or limited edition backpacks feature unique fabrics and patterns that can create buzz and attract attention in the market. These backpacks are often released in small quantities, making them ideal for special campaigns and collaborations that aim to generate exclusivity and urgency. However, managing inventory can be complex due to their limited nature, and buyers should negotiate terms for potential reorders carefully. The rarity of these items can lead to premium pricing, appealing to niche markets willing to pay more for unique products.
Pre-Customized
Pre-customized Stoney Clover backpacks come embellished with trendy patches or embroidery, catering to the fast-moving retail sector and event promotions. Their striking designs can drive impulse purchases, making them an attractive option for buyers looking to capitalize on current trends. However, the limited flexibility in stock mixing may pose a challenge for inventory management. B2B buyers should assess the potential for customization options and the impact on overall margin, as these factors can influence long-term purchasing strategies.
Related Video: Stoney Clover Lane Mini Backpack Try-On & Review
Key Industrial Applications of stoney clover backpack
Industry/Sector | Specific Application of Stoney Clover Backpack | Value/Benefit for the Business | Key Sourcing Considerations for this Application |
---|---|---|---|
Education | School Supply Programs | Durable, trendy option for students | Bulk purchasing agreements, customization options |
Retail | Seasonal Promotions | Attracts diverse consumer demographics | Quality assurance, design trends, and inventory management |
Corporate Gifting | Employee Recognition Programs | Enhances brand loyalty and employee morale | Custom branding options, timely delivery, and packaging |
Hospitality | Guest Amenities in Hotels | Adds a unique touch to guest experiences | Quality materials, compliance with local regulations |
Event Marketing | Promotional Events and Trade Shows | High visibility and brand exposure | Lead times, customization, and logistics coordination |
Education
In the education sector, Stoney Clover backpacks are increasingly utilized in school supply programs. Their durability and contemporary designs make them appealing to students and parents alike, ensuring steady demand. B2B buyers in this field should focus on bulk purchasing agreements that allow for customization, such as school logos or student names, which can enhance brand loyalty and reduce competition. Ensuring quality control and colorfastness is essential to maintain a professional appearance throughout the school year.
Retail
Retailers often leverage Stoney Clover backpacks for seasonal promotions, especially around back-to-school and holiday sales. Their vibrant colors and customizable options attract a wide range of consumers, from young students to trendy adults. B2B buyers must stay informed about current design trends and ensure quality assurance to meet consumer expectations. Effective inventory management is crucial to balance supply with demand, particularly during peak sales periods.
Corporate Gifting
In the realm of corporate gifting, Stoney Clover backpacks serve as ideal items for employee recognition programs. They offer a unique blend of practicality and style, enhancing brand loyalty while providing employees with a fashionable accessory. Buyers in this sector should prioritize options for custom branding, ensuring that their company logo is prominently displayed. Timely delivery and attractive packaging also play a vital role in maintaining a positive corporate image.
Hospitality
Hotels and resorts can elevate guest experiences by providing Stoney Clover backpacks as part of their amenities. These backpacks can be filled with travel essentials or branded souvenirs, adding a personal touch to a guest’s stay. B2B buyers in the hospitality industry should consider sourcing high-quality materials that align with their brand image and comply with local regulations. This ensures both durability and an upscale perception, enhancing overall guest satisfaction.
Event Marketing
Stoney Clover backpacks are increasingly popular for promotional events and trade shows, where visibility and brand exposure are key. Their customizable features allow companies to create eye-catching designs that resonate with potential customers. B2B buyers focusing on event marketing need to be mindful of lead times for production and delivery, as well as the logistics of distributing these items at events. Customization options should be carefully selected to align with the target audience’s preferences, ensuring maximum impact.
Related Video: Uses of Metals and Non Metals
Strategic Material Selection Guide for stoney clover backpack
When sourcing materials for Stoney Clover backpacks, international B2B buyers must consider various factors that influence product performance, manufacturing complexity, and market suitability. This section analyzes four common materials used in the production of these backpacks: nylon, canvas, leather, and polyester. Each material presents unique properties, advantages, and challenges that can significantly impact the final product’s quality and marketability.
Nylon
Key Properties: Nylon is a synthetic fabric known for its excellent strength-to-weight ratio, water resistance, and durability. It can withstand high temperatures and has a good resistance to abrasion and tearing, making it suitable for everyday use.
Pros & Cons: The main advantages of nylon include its lightweight nature, cost-effectiveness, and versatility in design. However, it can be less eco-friendly than natural fibers and may require specific treatments to enhance UV resistance. Manufacturing complexity is moderate, as nylon can be easily dyed and printed.
Impact on Application: Nylon backpacks are ideal for active consumers, particularly in regions with humid climates, as they resist moisture and mold. However, buyers should consider the environmental impact of sourcing nylon and look for suppliers who adhere to sustainable practices.
Considerations for International Buyers: Buyers from Africa, South America, and Europe should ensure compliance with local regulations regarding synthetic materials. Standards like ASTM and ISO certifications may apply, particularly in markets like the EU, where eco-labeling is becoming increasingly important.
Canvas
Key Properties: Canvas is a heavy-duty fabric made from cotton or a cotton-polyester blend. It is breathable, durable, and offers a natural texture that appeals to eco-conscious consumers.
Pros & Cons: Canvas is highly customizable, allowing for vibrant prints and embroidery. Its main drawback is that it is heavier than synthetic alternatives and generally less water-resistant unless treated. The manufacturing process can be more complex due to the need for additional treatments.
Impact on Application: Canvas backpacks are particularly popular in boutique retail settings and among consumers seeking sustainable options. They are suitable for branding and promotional use, especially in markets focused on eco-friendliness.
Considerations for International Buyers: Buyers should verify that the canvas is sourced from certified organic or recycled materials to meet consumer demand and regulatory standards. In regions like Europe, compliance with sustainability certifications can enhance marketability.
Leather
Key Properties: Leather, whether genuine or synthetic, offers a luxurious aesthetic and excellent durability. It is resistant to wear and tear, making it suitable for high-end applications.
Pros & Cons: The key advantage of leather is its premium appeal, which can justify higher price points. However, it is more expensive to source and may involve longer lead times. Manufacturing complexity increases due to the need for specialized techniques in leather treatment and finishing.
Impact on Application: Leather-accented backpacks cater to upscale markets, including luxury retail and hospitality sectors. They are particularly popular in regions like the Middle East and Europe, where luxury goods are in high demand.
Considerations for International Buyers: Buyers must ensure compliance with regulations regarding animal products, particularly in the EU, where specific labeling requirements apply. Understanding the differences between genuine and synthetic leather is crucial for maintaining product integrity.
Polyester
Key Properties: Polyester is a synthetic fiber known for its durability, resistance to shrinking and stretching, and quick-drying properties. It is often blended with other materials to enhance performance.
Pros & Cons: Polyester is generally less expensive than nylon and offers good color retention. However, it can be less breathable and may not perform as well in extreme conditions. The manufacturing process is relatively straightforward, making it a popular choice for mass production.
Impact on Application: Polyester backpacks are versatile and can be used in a variety of settings, from casual to professional. They are particularly suited for budget-conscious consumers who prioritize functionality.
Considerations for International Buyers: Buyers should be aware of the environmental implications of polyester production and consider sourcing recycled polyester to meet sustainability goals. Compliance with international standards for synthetic materials is also essential.
Summary Table
Material | Typical Use Case for stoney clover backpack | Key Advantage | Key Disadvantage/Limitation | Relative Cost (Low/Med/High) |
---|---|---|---|---|
Nylon | Everyday casual and active backpacks | Lightweight and durable | Less eco-friendly | Medium |
Canvas | Boutique and eco-friendly backpacks | Highly customizable | Heavier and less water-resistant | Medium |
Leather | Luxury and premium backpacks | Premium aesthetic and durability | Higher cost and longer lead times | High |
Polyester | Budget-friendly and versatile backpacks | Cost-effective and durable | Less breathable | Low |
This comprehensive analysis provides B2B buyers with actionable insights into material selection for Stoney Clover backpacks, enabling informed sourcing decisions that align with market demands and regulatory requirements.
In-depth Look: Manufacturing Processes and Quality Assurance for stoney clover backpack
In the competitive landscape of B2B sourcing, understanding the manufacturing processes and quality assurance standards for Stoney Clover backpacks is crucial for buyers. This knowledge not only helps in ensuring the authenticity and durability of the products but also aids in maintaining a strong market presence. Below is a detailed exploration of the typical manufacturing stages, key techniques, and quality assurance practices relevant to international B2B buyers.
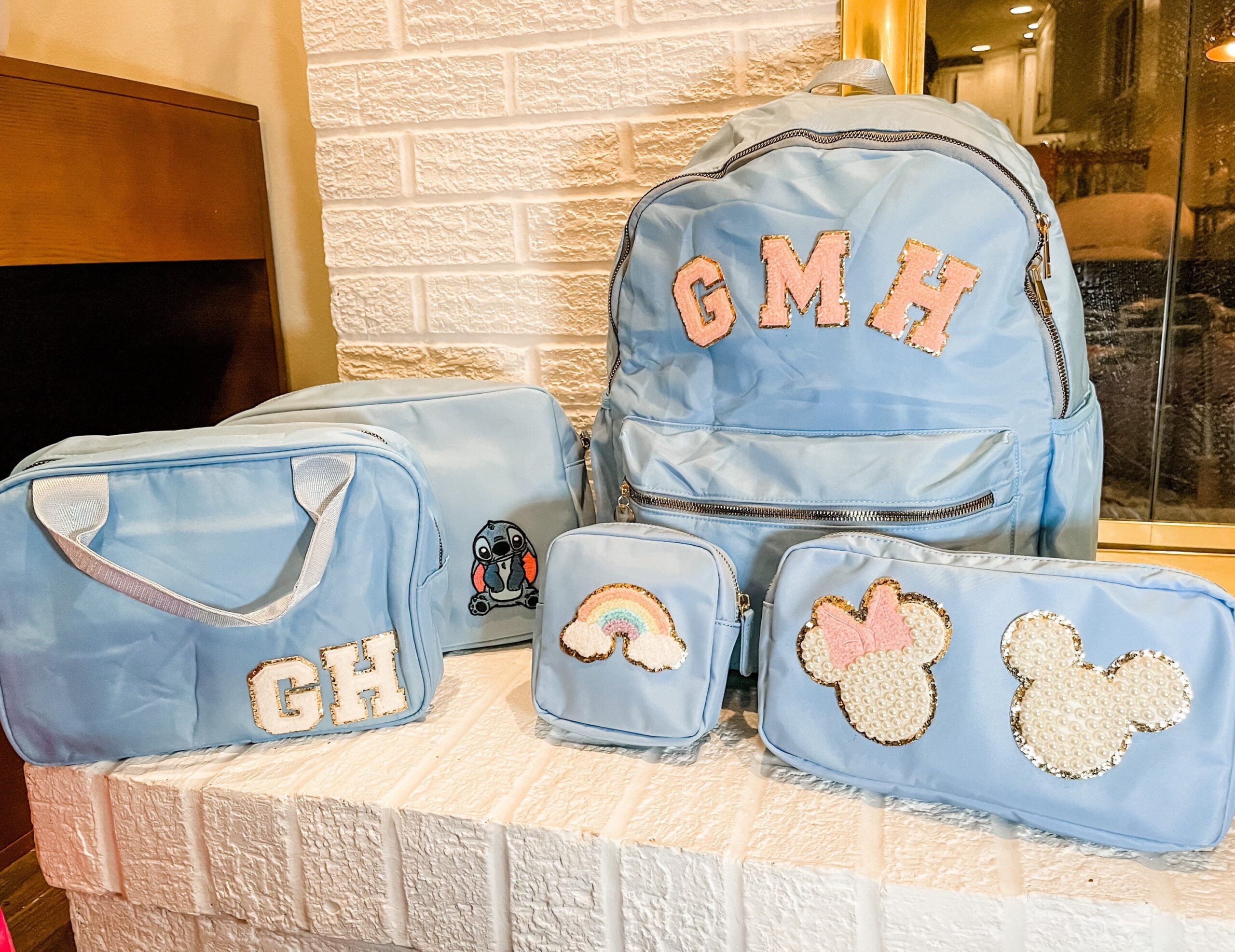
Illustrative Image (Source: Google Search)
Manufacturing Processes
1. Material Preparation
The journey of producing a Stoney Clover backpack begins with sourcing high-quality materials. The selection of fabric—whether it be nylon, canvas, or leather—directly influences the final product’s durability, weight, and aesthetic appeal.
- Sourcing Techniques: Buyers should visit reputable fabric markets or work with established suppliers who can provide certifications for the materials, such as organic or recycled options. This is particularly important for markets in Africa and South America, where eco-consciousness is on the rise.
- Material Testing: Before mass production, materials should undergo testing for strength, water resistance, and colorfastness to ensure they meet desired specifications.
2. Forming
Once materials are sourced, the next step is to create patterns and templates. This process involves drafting a blueprint for the backpack’s components.
- Pattern Making: Using CAD software, manufacturers can create precise templates that guide the cutting process. This technology minimizes waste and ensures accuracy in production.
- Cutting: The fabric is cut according to the templates, using either manual methods for smaller batches or automated cutting machines for larger orders. Precision at this stage is critical to avoid material wastage.
3. Assembly
The assembly phase is where the individual components come together to form the final product.
- Sewing Techniques: Skilled workers utilize industrial sewing machines to stitch the main body, pockets, and straps. It is common practice to sew the bags inside out to hide seams, enhancing the bag’s visual appeal and durability.
- Attachment of Accessories: This includes integrating zippers, buckles, and decorative elements, which can significantly affect the backpack’s functionality and marketability.
4. Finishing
The final touches on the backpack occur during the finishing stage. This includes inverting the bag, performing final inspections, and adding any last-minute branding elements such as embroidery or printing.
- Quality Checks: Each backpack undergoes an initial quality check to ensure all components are correctly assembled and meet design specifications.
Quality Assurance
Quality assurance is a pivotal aspect of the manufacturing process, ensuring that the final product not only meets but exceeds industry standards.
International Standards
For B2B buyers, understanding relevant international quality standards is essential. Key standards include:
- ISO 9001: This is a widely recognized standard for quality management systems, ensuring that manufacturers adhere to consistent quality processes.
- CE Marking: Particularly relevant in Europe, this certification indicates compliance with health, safety, and environmental protection standards.
Quality Control Checkpoints
Implementing robust quality control checkpoints throughout the manufacturing process is vital for maintaining product integrity:
- Incoming Quality Control (IQC): Inspecting raw materials upon arrival to ensure they meet specified standards.
- In-Process Quality Control (IPQC): Continuous monitoring during the manufacturing process to catch defects early.
- Final Quality Control (FQC): A comprehensive inspection of finished products to ensure they are free of defects and meet the agreed specifications.
Common Testing Methods
B2B buyers should be familiar with various testing methods employed to assess the quality of the backpacks:
- Material Testing: Tests for tensile strength, abrasion resistance, and water resistance.
- Functional Testing: Assessing zippers, straps, and overall usability of the backpack.
- Durability Testing: Simulating real-world usage to evaluate how the product holds up over time.
Verifying Supplier Quality Control
For international buyers, particularly from regions like Africa, South America, the Middle East, and Europe, verifying a supplier’s quality control measures is essential to mitigate risks.
- Supplier Audits: Conducting on-site audits can provide insights into the manufacturing processes and quality control systems in place. This is particularly important for establishing trust with suppliers in emerging markets.
- Requesting Quality Reports: Buyers should request documentation that outlines the supplier’s quality control processes and any certifications they hold.
- Third-Party Inspections: Engaging third-party inspection services can provide an unbiased assessment of the manufacturing quality and adherence to international standards.
Quality Control Nuances for International Buyers
B2B buyers must be aware of specific nuances that can affect quality control in international sourcing:
- Cultural Differences: Understanding local manufacturing practices and quality expectations can help in establishing effective communication with suppliers.
- Regulatory Compliance: Different regions may have varying regulations regarding materials and safety standards. Buyers should ensure that their suppliers comply with both local and international regulations to avoid legal complications.
Conclusion
For B2B buyers looking to source Stoney Clover backpacks, a comprehensive understanding of the manufacturing processes and quality assurance practices is imperative. By prioritizing supplier quality control, leveraging international standards, and being proactive in verifying manufacturing practices, businesses can enhance their sourcing strategies and ensure that they provide high-quality products to their customers. This not only safeguards their reputation but also helps in building long-lasting relationships with suppliers and customers alike.
Related Video: How a Backpack is Made : Every Step on the Production Line
Comprehensive Cost and Pricing Analysis for stoney clover backpack Sourcing
Understanding the cost structure and pricing dynamics of sourcing Stoney Clover backpacks is crucial for international B2B buyers aiming to optimize their procurement strategies. This section delves into the various cost components, price influencers, and practical tips for buyers from regions such as Africa, South America, the Middle East, and Europe.
Cost Components
-
Materials: The choice of materials significantly affects the overall cost. Common options include nylon, canvas, and leather, each with different price points. High-quality materials may incur higher initial costs but can lead to better margins due to increased customer satisfaction and brand loyalty.
-
Labor: Labor costs vary depending on the manufacturing location. For instance, countries with lower labor costs may offer competitive pricing, but buyers must ensure that quality standards are not compromised. Skilled labor is often required for intricate customizations and quality control.
-
Manufacturing Overhead: This encompasses the indirect costs associated with production, such as utilities, rent, and equipment maintenance. Buyers should inquire about these costs as they can significantly affect the final price.
-
Tooling: Custom tooling for specialized backpack features can add to upfront costs. However, investing in tooling can reduce unit costs in the long run, especially for large orders.
-
Quality Control (QC): Implementing strict QC measures is essential for maintaining brand reputation. Buyers may choose to incorporate QC costs into their pricing strategy, ensuring that only high-quality products reach the market.
-
Logistics: Shipping and handling can vary widely based on the origin of the goods and the destination market. Understanding Incoterms and choosing the right shipping methods can optimize costs.
-
Margin: Suppliers typically mark up their prices to ensure profitability. Understanding the expected margin in the market helps buyers negotiate better prices and terms.
Price Influencers
Several factors can influence the final pricing of Stoney Clover backpacks:
-
Volume/MOQ: Larger orders often lead to lower per-unit costs. Buyers should consider their capacity for inventory and negotiate minimum order quantities (MOQs) that align with their sales forecasts.
-
Specifications/Customization: Custom features, such as unique prints or embroidery, can increase costs. Buyers must evaluate whether the added value justifies the expense.
-
Materials and Quality Certifications: High-quality materials and certifications (e.g., eco-friendly or fair-trade labels) can enhance product appeal but may also raise costs. Buyers should assess market demand for such features.
-
Supplier Factors: The reliability, reputation, and location of the supplier can affect pricing. It’s essential to conduct thorough due diligence and build relationships with trustworthy suppliers.
-
Incoterms: Understanding shipping terms can help buyers manage logistics costs and responsibilities effectively. Choosing the right Incoterm can minimize unexpected expenses.
Buyer Tips
-
Negotiation: Engage in active negotiation with suppliers. Presenting data on market trends, competitor pricing, and potential order volumes can strengthen your position.
-
Cost-Efficiency: Calculate the Total Cost of Ownership (TCO), which includes all costs associated with the purchase, not just the unit price. This approach helps in making informed decisions.
-
Pricing Nuances: International buyers should be aware of currency fluctuations, tariffs, and import duties that may impact the final cost. Establish clear communication with suppliers regarding pricing adjustments based on these factors.
-
Market Research: Conduct thorough market research to understand competitor pricing and consumer preferences. This knowledge will assist in setting competitive pricing strategies for your offerings.
Disclaimer
The prices and cost components discussed are indicative and may vary based on specific supplier agreements, market conditions, and regional factors. Buyers should conduct their own research and obtain tailored quotes for accurate budgeting.
By understanding the intricacies of cost and pricing dynamics in sourcing Stoney Clover backpacks, B2B buyers can make informed decisions that enhance profitability and competitiveness in their respective markets.
Spotlight on Potential stoney clover backpack Manufacturers and Suppliers
This section offers a look at a few manufacturers active in the ‘stoney clover backpack’ market. This is a representative sample for illustrative purposes; B2B buyers must conduct their own extensive due diligence before any engagement. Information is synthesized from public sources and general industry knowledge.
Essential Technical Properties and Trade Terminology for stoney clover backpack
Understanding the technical properties and trade terminology associated with Stoney Clover backpacks is essential for international B2B buyers. This knowledge not only facilitates informed sourcing decisions but also helps in negotiating better terms with suppliers. Below are critical specifications and industry jargon relevant to these fashionable backpacks.
Key Technical Properties
-
Material Grade
The material grade refers to the quality and type of fabric used in the backpack’s construction. Common materials include nylon, canvas, and leather. Higher-grade materials often provide better durability, resistance to wear and tear, and aesthetic appeal. For B2B buyers, understanding material grades ensures that they select products that meet their target market’s expectations, balancing quality and cost. -
Water Resistance
This property indicates the backpack’s ability to repel water, which is crucial for outdoor use or in regions with high humidity. Buyers should verify the water resistance rating (e.g., water-resistant vs. waterproof) to ensure the product meets customer needs. For instance, a higher water resistance rating may justify a premium price point in markets prone to rain.
-
Load Capacity
Load capacity defines the maximum weight the backpack can safely carry. This specification is vital for buyers targeting specific consumer segments, such as students or outdoor enthusiasts. Ensuring that the backpacks can handle the expected load without compromising comfort or durability can enhance customer satisfaction and reduce return rates. -
Stitching Tolerance
This refers to the precision of stitching used in the backpack’s assembly. Tighter stitching tolerances often indicate higher quality, leading to improved durability and performance. B2B buyers should inquire about the stitching standards employed by manufacturers to ensure that the product can withstand rigorous use, especially in the youth and outdoor markets. -
Colorfastness
Colorfastness measures the ability of the backpack’s fabric to retain its color after exposure to washing, light, or other environmental factors. High colorfastness is essential for maintaining aesthetic appeal over time, which is particularly important for products aimed at fashion-conscious consumers. Buyers should seek suppliers who provide detailed testing results for colorfastness.
Common Trade Terminology
-
OEM (Original Equipment Manufacturer)
OEM refers to companies that produce parts and equipment that may be marketed by another manufacturer. In the context of backpacks, an OEM might produce Stoney Clover backpacks for a retailer under a private label. Understanding OEM relationships can help buyers identify potential partners and negotiate better terms. -
MOQ (Minimum Order Quantity)
MOQ is the smallest quantity of a product that a supplier is willing to sell. It is crucial for B2B buyers to know the MOQ when planning inventory and managing cash flow. A higher MOQ may lead to lower per-unit costs but could also result in excess inventory if demand forecasts are inaccurate. -
RFQ (Request for Quotation)
An RFQ is a document sent to suppliers to request pricing and other terms for specified products. For buyers, effectively crafting an RFQ ensures they receive comprehensive and comparable quotes, facilitating informed decision-making. -
Incoterms (International Commercial Terms)
Incoterms are a set of predefined international trade terms that clarify the responsibilities of buyers and sellers regarding shipping, insurance, and tariffs. Familiarity with Incoterms is essential for B2B buyers to avoid misunderstandings and to clearly define shipping responsibilities, especially when importing from different regions. -
Lead Time
Lead time refers to the time taken from placing an order until it is delivered. Understanding lead times is critical for inventory management and meeting market demands. Buyers should consider the lead time when negotiating with suppliers to ensure they can respond quickly to market opportunities.
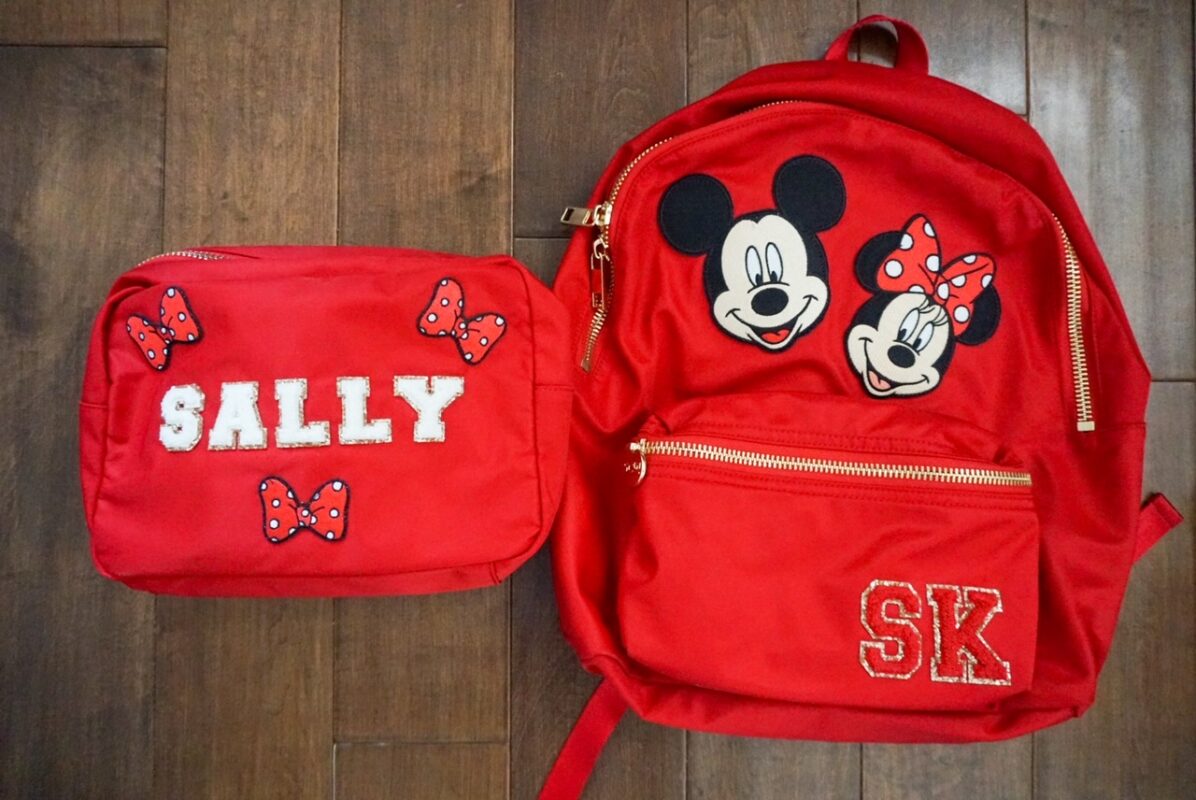
Illustrative Image (Source: Google Search)
By grasping these technical properties and trade terms, B2B buyers can enhance their sourcing strategies, optimize their inventory, and ultimately increase their competitive advantage in the market for Stoney Clover backpacks.
Navigating Market Dynamics, Sourcing Trends, and Sustainability in the stoney clover backpack Sector
Global drivers influencing the Stoney Clover backpack market include a surge in consumer demand for personalized and high-quality products. As lifestyle and fashion trends evolve, international B2B buyers are increasingly drawn to customizable options that resonate with diverse demographics. This trend is particularly pronounced in regions such as Africa and South America, where young consumers seek unique, expressive products. Additionally, the rise of e-commerce platforms has facilitated broader access to global suppliers, enabling buyers to source products efficiently.
Emerging technologies are also reshaping sourcing practices. For instance, advanced analytics and AI tools allow B2B buyers to predict consumer preferences and optimize inventory management. Blockchain technology is gaining traction for enhancing transparency in the supply chain, crucial for maintaining product authenticity and traceability. The ability to track raw materials and production processes is especially relevant for buyers in Europe and the Middle East, where regulations on product origins are stringent.
Market dynamics are further influenced by fluctuating raw material costs, which can significantly impact pricing strategies. Buyers must remain vigilant regarding global supply chain disruptions, especially in light of recent geopolitical tensions and environmental challenges. Engaging in strategic partnerships and diversifying supplier bases can mitigate risks and enhance resilience in the face of these market fluctuations.
Sustainability & Ethical Sourcing in B2B
Sustainability has become a pivotal concern in the Stoney Clover backpack sector, driven by increasing consumer awareness of environmental issues. B2B buyers are prioritizing suppliers who demonstrate a commitment to sustainable practices, including the use of eco-friendly materials and ethical manufacturing processes. The environmental impact of traditional materials, such as synthetic fabrics, has prompted a shift toward sustainable alternatives like organic cotton and recycled polyester.
Ethical supply chains are crucial for maintaining brand integrity and meeting consumer expectations. Buyers should seek suppliers who provide transparency regarding their sourcing practices, labor conditions, and environmental policies. Certifications such as Global Organic Textile Standard (GOTS) and OEKO-TEX can serve as benchmarks for evaluating the sustainability of materials and production processes.
Incorporating sustainable practices not only meets regulatory requirements but also enhances brand loyalty among environmentally conscious consumers. As markets in Africa, South America, the Middle East, and Europe continue to evolve, integrating sustainability into sourcing strategies will be essential for long-term success.
Brief Evolution/History
The Stoney Clover brand has evolved significantly since its inception, initially focusing on customizable accessories that appealed primarily to younger consumers. Over the years, the brand has expanded its product line, incorporating innovative designs and diverse materials to cater to a broader audience. The growing emphasis on personalization and quality has propelled the Stoney Clover backpack into a prominent position within the lifestyle and fashion accessories market. Today, it stands as a symbol of individuality and creativity, making it a compelling option for B2B buyers looking to capitalize on emerging trends in consumer preferences.
Related Video: International Trade Explained
Frequently Asked Questions (FAQs) for B2B Buyers of stoney clover backpack
-
What criteria should I use for supplier vetting when sourcing Stoney Clover backpacks?
When vetting suppliers for Stoney Clover backpacks, consider their experience in the industry, production capabilities, and quality certifications (such as ISO or BSCI). Request references from past clients and verify their compliance with international labor laws. It’s also beneficial to conduct factory visits or third-party audits to assess their operational standards. Look for suppliers who can provide samples to evaluate material quality and craftsmanship, ensuring they can meet your specific requirements. -
Can I customize Stoney Clover backpacks, and what options are available?
Yes, Stoney Clover backpacks offer various customization options, including fabric choices, colors, and additional features like embroidery or patches. Depending on the supplier, you may also be able to request special editions or limited runs. Ensure you communicate your branding needs clearly, and inquire about the cost implications and minimum order quantities (MOQs) for customized products. Always review samples to confirm that the final product aligns with your expectations. -
What are typical lead times and minimum order quantities (MOQs) for Stoney Clover backpacks?
Lead times for Stoney Clover backpacks generally range from 4 to 12 weeks, depending on the complexity of the order and the supplier’s production capacity. MOQs vary by supplier; however, they typically start at around 100 units for standard designs and can increase for customized options. Discuss these factors upfront with potential suppliers to avoid delays and ensure they can accommodate your timeline and volume needs. -
What payment terms should I negotiate with suppliers?
Common payment terms in the B2B space include a deposit (often 30-50%) upon order confirmation, with the balance due before shipment. Consider negotiating payment milestones linked to production stages to mitigate risk. It’s advisable to use secure payment methods, such as letters of credit or escrow services, especially when dealing with new suppliers. Always clarify terms regarding refunds or disputes to ensure protection against potential issues. -
How can I ensure quality assurance and compliance with certifications?
To ensure quality assurance, request detailed product specifications and compliance certifications from your supplier. Look for certifications relevant to your market, such as CE marking in Europe or ASTM standards in the U.S. Establish a quality control process, including pre-shipment inspections, to verify that products meet your standards. Collaborating with third-party inspection services can also provide an unbiased assessment of product quality before shipping. -
What logistics considerations should I keep in mind when sourcing internationally?
When sourcing Stoney Clover backpacks internationally, consider shipping methods, customs regulations, and potential tariffs. Decide between air freight for speed or sea freight for cost-effectiveness based on your timeline and budget. Partner with a reliable freight forwarder familiar with the regulations in your target market. Ensure that all documentation, such as invoices and packing lists, is accurate to avoid customs delays or additional fees. -
How should I handle disputes with suppliers?
To effectively manage disputes with suppliers, establish clear communication channels and document all agreements in writing. If a dispute arises, attempt to resolve it through direct negotiation first. If unsuccessful, consider mediation or arbitration as a next step, referencing the terms outlined in your contract. Having a clear dispute resolution process can help maintain a professional relationship and minimize disruption to your supply chain. -
What market trends should I be aware of when selling Stoney Clover backpacks?
Stay informed about current market trends such as sustainability, personalization, and the rise of e-commerce in the fashion accessories sector. Consumers increasingly prefer eco-friendly materials and practices, so sourcing backpacks made from sustainable fabrics can enhance your brand appeal. Additionally, leveraging social media and influencer marketing can drive demand, particularly among younger demographics. Regularly review consumer feedback and competitor offerings to adapt your strategies accordingly.
Strategic Sourcing Conclusion and Outlook for stoney clover backpack
The strategic sourcing of Stoney Clover backpacks presents an exciting opportunity for international B2B buyers aiming to tap into the lucrative lifestyle and accessories market. Key takeaways emphasize the importance of understanding the diverse types of backpacks available, from classic nylon to premium leather-accented options, each catering to different market segments and consumer preferences. Buyers should prioritize supplier vetting, ensuring that manufacturing partners adhere to high-quality standards and ethical practices.
In addition, being aware of global pricing factors and material sourcing can significantly optimize costs and enhance profit margins. As demand for customizable and high-quality products continues to grow, strategic sourcing becomes essential for staying competitive in diverse regions such as Africa, South America, the Middle East, and Europe.
Looking ahead, now is the time to act. By leveraging the insights provided in this guide, buyers can position themselves advantageously in the marketplace, ensuring they meet evolving consumer demands and capitalize on emerging trends. Engage with trusted suppliers, explore innovative customization options, and strengthen your brand’s presence—your next successful sourcing endeavor awaits!