Master Sourcing Quality Butterfly Backpacks for Your B2B
Guide to Butterfly Backpack
- Introduction: Navigating the Global Market for butterfly backpack
- Understanding butterfly backpack Types and Variations
- Key Industrial Applications of butterfly backpack
- Strategic Material Selection Guide for butterfly backpack
- In-depth Look: Manufacturing Processes and Quality Assurance for butterfly backpack
- Comprehensive Cost and Pricing Analysis for butterfly backpack Sourcing
- Spotlight on Potential butterfly backpack Manufacturers and Suppliers
- Essential Technical Properties and Trade Terminology for butterfly backpack
- Navigating Market Dynamics, Sourcing Trends, and Sustainability in the butterfly backpack Sector
- Frequently Asked Questions (FAQs) for B2B Buyers of butterfly backpack
- Strategic Sourcing Conclusion and Outlook for butterfly backpack
Introduction: Navigating the Global Market for butterfly backpack
In today’s competitive landscape, the butterfly backpack has emerged as a popular choice for consumers seeking stylish yet functional solutions for everyday use. This unique design not only appeals to a diverse demographic but also serves various purposes, from casual outings to professional settings. For B2B buyers, understanding the significance of this product is paramount. As the demand for innovative and high-quality backpacks increases, sourcing the right products becomes a critical factor in maintaining market relevance and customer satisfaction.
This comprehensive guide delves into the essential aspects of butterfly backpack sourcing, covering types, materials, manufacturing quality control, supplier selection, cost considerations, and market insights. By addressing common challenges and quality issues in backpack production, we aim to equip international B2B buyers—particularly those from Africa, South America, the Middle East, and Europe—with actionable insights that streamline their sourcing processes.
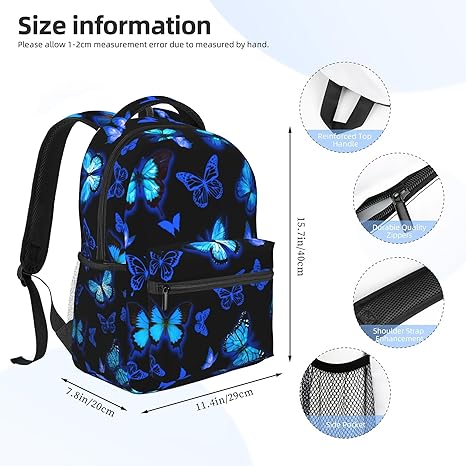
Illustrative Image (Source: Google Search)
By leveraging this guide, you will gain the expertise needed to make informed purchasing decisions that not only enhance your product offerings but also fortify your brand’s reputation in the global marketplace. From evaluating potential suppliers to understanding the nuances of quality checks, our insights will empower you to navigate the complexities of sourcing butterfly backpacks effectively, ensuring that your business thrives in an increasingly competitive environment.
Understanding butterfly backpack Types and Variations
Type Name | Key Distinguishing Features | Primary B2B Applications | Brief Pros & Cons for Buyers |
---|---|---|---|
Standard Butterfly Backpack | Flap closure, spacious main compartment, padded straps | Retail, outdoor activities, school supplies | Versatile design; may lack specialized features for niche markets |
Eco-Friendly Butterfly Backpack | Made from sustainable materials, recyclable components | Eco-conscious brands, promotional events | Appeals to green consumers; potentially higher production costs |
Tech-Savvy Butterfly Backpack | Dedicated compartments for electronics, USB charging ports | Corporate gifts, tech retailers | High functionality; may require premium pricing |
Fashion-Forward Butterfly Backpack | Trendy designs, vibrant colors, unique patterns | Fashion retailers, youth markets | Strong aesthetic appeal; may compromise on durability |
Multi-functional Butterfly Backpack | Convertible designs, additional pockets, and attachments | Travel, urban commuting | Highly adaptable; may be complex to manufacture |
Standard Butterfly Backpack
The Standard Butterfly Backpack is characterized by its practical flap closure and spacious main compartment, making it a popular choice for a variety of uses. It is ideal for retailers and outdoor activity providers, as it can easily accommodate school supplies or gear for hiking. When purchasing, consider the quality of materials and stitching, as these factors can greatly affect durability and customer satisfaction.
Eco-Friendly Butterfly Backpack
With growing consumer awareness of sustainability, the Eco-Friendly Butterfly Backpack has emerged as a key option for B2B buyers targeting environmentally conscious markets. These backpacks are constructed from sustainable materials and often feature recyclable components. They are ideal for brands looking to enhance their green credentials during promotional events. However, buyers should be mindful that the sourcing of eco-friendly materials may lead to higher production costs.
Tech-Savvy Butterfly Backpack
The Tech-Savvy Butterfly Backpack caters specifically to the needs of modern consumers who rely on electronic devices. This type features dedicated compartments for laptops and tablets, along with USB charging ports for convenience. It is a great choice for corporate gifts or tech retailers. B2B buyers should focus on ensuring that the materials used provide adequate protection for electronics, as well as assessing the overall comfort and usability for end-users.
Fashion-Forward Butterfly Backpack
For businesses operating in the fashion retail sector, the Fashion-Forward Butterfly Backpack stands out with its trendy designs, vibrant colors, and unique patterns. This type of backpack appeals particularly to youth markets and fashion-conscious consumers. While it offers strong aesthetic appeal, buyers should be cautious about potential compromises in durability, especially if the backpack is intended for heavy use.
Multi-functional Butterfly Backpack
The Multi-functional Butterfly Backpack is designed for versatility, featuring convertible designs and additional pockets for various uses. It is particularly suited for travelers and urban commuters who require adaptability in their daily gear. While these backpacks are highly functional, B2B buyers should consider the complexity of manufacturing, as intricate designs may lead to higher production costs and longer lead times.
Related Video: Large Language Models (LLMs) – Everything You NEED To Know
Key Industrial Applications of butterfly backpack
Industry/Sector | Specific Application of Butterfly Backpack | Value/Benefit for the Business | Key Sourcing Considerations for this Application |
---|---|---|---|
Education | Student backpacks for schools | Enhances brand recognition among youth | Focus on durability, comfort, and design customization |
Outdoor Recreation | Hiking and camping gear | Attracts outdoor enthusiasts, boosting sales | Material resistance to weather, ergonomic design features |
Travel and Tourism | Luggage for tour operators | Provides reliable, stylish options for travelers | Lightweight materials, ample storage, and security features |
Corporate Gifts | Promotional backpacks for events | Increases brand visibility and customer loyalty | Custom branding options, quality assurance, and timely delivery |
Retail and E-commerce | Private label backpacks for retailers | Expands product line and differentiates brand | Competitive pricing, supplier reliability, and production speed |
Education
In the education sector, butterfly backpacks are commonly used as student backpacks in schools. These backpacks are designed to be lightweight yet durable, accommodating textbooks and supplies while ensuring comfort during daily commutes. For international B2B buyers, particularly from regions like Africa and South America, sourcing high-quality materials that can withstand daily wear is crucial. Buyers should look for suppliers that offer customizable designs to cater to local preferences and trends.
Outdoor Recreation
In the outdoor recreation industry, butterfly backpacks serve as essential gear for hiking and camping. They are designed to be rugged, weather-resistant, and ergonomic, making them ideal for adventurers. Buyers from the Middle East and Europe should prioritize suppliers that provide materials with high abrasion resistance and water repellency. Understanding the local outdoor culture can also inform design choices, such as color schemes and functionality, ensuring the product resonates with target customers.
Travel and Tourism
Butterfly backpacks are increasingly popular among tour operators as they provide reliable luggage options for travelers. These backpacks can be designed to include features like anti-theft compartments and easy access pockets, enhancing the travel experience. For B2B buyers in Europe and South America, it is essential to consider the lightweight nature of the materials used, along with ample storage space. Collaborating with manufacturers who specialize in travel gear can also ensure high-quality products that meet global standards.
Corporate Gifts
In the realm of corporate gifts, butterfly backpacks are an effective promotional item for events and conferences. They offer businesses a way to increase brand visibility while providing practical items to clients and employees. International buyers should focus on sourcing backpacks that can be easily customized with logos and branding elements. Ensuring quality assurance during production is vital to maintaining brand reputation, especially when distributing products at high-profile events.
Retail and E-commerce
For retailers and e-commerce businesses, butterfly backpacks can be produced as private label products, allowing companies to expand their product lines. This application not only helps in differentiating the brand but also attracts diverse customer segments. B2B buyers should seek suppliers that offer competitive pricing without compromising on quality. Additionally, understanding the production timelines and having clear communication with manufacturers can streamline the sourcing process, ensuring timely delivery to meet market demands.
Related Video: Farm tools and their uses
Strategic Material Selection Guide for butterfly backpack
When selecting materials for butterfly backpacks, international B2B buyers must consider various factors that impact product performance, durability, and cost-effectiveness. Below is an analysis of four common materials used in the production of butterfly backpacks, focusing on their properties, advantages, disadvantages, and specific considerations for buyers from regions like Africa, South America, the Middle East, and Europe.
1. Nylon
Key Properties: Nylon is known for its high tensile strength, resistance to abrasion, and lightweight nature. It can withstand temperatures up to 120°C and has good moisture-wicking properties, making it suitable for various weather conditions.
Pros & Cons:
– Advantages: Durable, lightweight, and resistant to mold and mildew. It is also relatively easy to dye, allowing for vibrant colors.
– Disadvantages: Can be more expensive than other materials like polyester. It is also less UV resistant, which may lead to fading over time.
Impact on Application: Nylon is ideal for outdoor and travel backpacks due to its strength and resistance to wear and tear. However, it may not be the best choice for environments with prolonged sun exposure.
Considerations for International Buyers: Buyers should ensure that the nylon used meets international standards such as ASTM and JIS for durability and safety. Additionally, sourcing from reputable suppliers who can provide certifications is crucial.
2. Polyester
Key Properties: Polyester offers good resistance to stretching and shrinking, as well as excellent UV resistance. It can tolerate temperatures up to 150°C and is generally resistant to mildew.
Pros & Cons:
– Advantages: More affordable than nylon, with good color retention and quick-drying properties. It is also resistant to wrinkles and can be easily cleaned.
– Disadvantages: While durable, it is less strong than nylon and may not perform as well under heavy loads.
Impact on Application: Polyester is suitable for everyday backpacks and school bags, where cost-effectiveness is a priority. However, it may not be the best option for high-performance outdoor activities.
Considerations for International Buyers: Buyers should look for suppliers who adhere to environmental standards, as polyester production can have a significant ecological impact. Certifications like Oeko-Tex can indicate safer practices.
3. Cordura Fabric
Key Properties: Cordura is a high-performance nylon fabric known for its exceptional durability and resistance to abrasions, tears, and scuffs. It can withstand extreme conditions and has a temperature tolerance similar to nylon.
Pros & Cons:
– Advantages: Extremely durable and long-lasting, making it ideal for heavy-duty backpacks. It also has water-resistant properties when treated.
– Disadvantages: Higher cost compared to standard nylon or polyester. It may also be heavier, which can affect the overall weight of the backpack.
Impact on Application: Cordura is perfect for tactical and outdoor backpacks that require maximum durability. Its robustness makes it less suitable for lightweight travel bags.
Considerations for International Buyers: Buyers should verify that Cordura fabrics are sourced from certified manufacturers to ensure quality. Compliance with standards such as ISO 9001 can provide assurance of manufacturing excellence.
4. Ripstop Nylon
Key Properties: Ripstop nylon is a lightweight fabric reinforced with a grid pattern of thicker threads, making it resistant to tearing and ripping. It can withstand temperatures up to 120°C and is generally water-resistant.
Pros & Cons:
– Advantages: Lightweight yet strong, making it ideal for backpacks designed for travel and hiking. It is also easy to pack and carry.
– Disadvantages: While it is strong, it may not be as durable as Cordura or standard nylon under extreme conditions.
Impact on Application: Ripstop nylon is well-suited for lightweight travel and hiking backpacks. However, it may not be ideal for heavy-duty applications.
Considerations for International Buyers: Buyers should ensure that ripstop nylon meets international safety and quality standards. Additionally, they should consider the environmental impact of production and seek suppliers with sustainable practices.
Summary Table
Material | Typical Use Case for butterfly backpack | Key Advantage | Key Disadvantage/Limitation | Relative Cost (Low/Med/High) |
---|---|---|---|---|
Nylon | Outdoor and travel backpacks | Durable and lightweight | More expensive than polyester | Medium |
Polyester | Everyday and school bags | Affordable with good color retention | Less strong than nylon | Low |
Cordura Fabric | Tactical and heavy-duty backpacks | Extremely durable and long-lasting | Higher cost and heavier | High |
Ripstop Nylon | Lightweight travel and hiking backpacks | Lightweight yet strong | Less durable under extreme conditions | Medium |
This analysis provides a comprehensive overview for international B2B buyers to make informed decisions regarding material selection for butterfly backpacks, ensuring they meet both quality standards and market demands.
In-depth Look: Manufacturing Processes and Quality Assurance for butterfly backpack
In the competitive world of backpack manufacturing, particularly for butterfly backpacks, understanding the manufacturing processes and quality assurance standards is essential for B2B buyers. This knowledge not only ensures that the products meet customer expectations but also protects brand reputation and reduces costs associated with returns and defects. Here’s an in-depth look at the typical manufacturing processes and quality assurance practices tailored for international B2B buyers.
Manufacturing Processes for Butterfly Backpacks
The manufacturing of butterfly backpacks typically involves several key stages, each critical to ensuring the final product meets quality and durability standards.
1. Material Preparation
The first stage involves selecting and preparing the materials. Common materials for butterfly backpacks include durable fabrics such as nylon, polyester, or canvas, along with various types of zippers and buckles.
- Material Selection: B2B buyers should prioritize high-quality materials that provide durability and resistance to wear and tear. For instance, fabrics like Cordura or ripstop nylon are known for their strength.
- Testing for Compliance: Before production, materials should undergo testing for abrasion resistance, tear strength, and colorfastness. Requesting samples from suppliers can help buyers assess quality firsthand.
2. Forming
This stage involves cutting and shaping the materials into the desired components of the backpack.
- Cutting Techniques: Precision cutting techniques, such as die-cutting, ensure that the fabric is shaped accurately, minimizing waste and ensuring uniformity.
- Layering: For butterfly backpacks, layering different materials (e.g., padded back panels) is essential for comfort and functionality. Buyers should confirm that the manufacturer uses appropriate layering techniques to enhance product ergonomics.
3. Assembly
Assembly is where the components come together to form the final product. This stage includes sewing the fabric pieces, attaching zippers, and adding other features like straps and pockets.
- Sewing Techniques: Strong stitching methods such as double-stitching and bar tacking at stress points enhance durability. B2B buyers should insist on inspecting production samples to ensure these techniques are applied effectively.
- Quality Control Points: Implementing inline inspections during assembly can catch defects early. Buyers can request that manufacturers provide documentation of these inspections.
4. Finishing
The finishing stage includes adding final touches, such as branding, labels, and any additional waterproofing treatments.
- Final Quality Checks: Before products are packaged, a thorough inspection should be conducted to ensure all features function correctly, such as zippers and buckles.
- Aesthetic Quality: Buyers should evaluate the visual appeal, ensuring that the colors and designs meet the specified standards.
Quality Assurance Practices
Quality assurance is crucial for maintaining product standards. Buyers should be aware of relevant international standards and industry-specific certifications that can help verify supplier quality.
International Standards
- ISO 9001: This standard focuses on quality management systems and is applicable across industries. It ensures that manufacturers maintain consistent quality in their processes.
- CE Marking: Relevant for products sold in the European market, CE marking indicates compliance with health, safety, and environmental protection standards.
- API Standards: For specialized applications, particularly in rugged environments, adherence to American Petroleum Institute (API) standards may be necessary.
Quality Control Checkpoints
Quality control checkpoints should be established at various stages of the manufacturing process:
- Incoming Quality Control (IQC): This involves inspecting raw materials upon receipt to ensure they meet specified standards.
- In-Process Quality Control (IPQC): Conducted during the manufacturing process, this ensures that each stage meets quality criteria.
- Final Quality Control (FQC): A comprehensive assessment before packaging, focusing on functionality and aesthetics.
Common Testing Methods
B2B buyers should familiarize themselves with common testing methods to ensure product reliability:
- Durability Testing: This can include stress tests for straps and zippers, as well as abrasion tests for fabrics.
- Water Resistance Testing: Essential for outdoor backpacks, this testing evaluates how well materials withstand water exposure.
- Comfort Testing: Ergonomic assessments should be conducted to ensure that the backpack is comfortable for extended wear.
Verifying Supplier Quality Control
To ensure that suppliers maintain high-quality standards, B2B buyers should consider the following approaches:
- Supplier Audits: Regular audits can help assess a supplier’s adherence to quality standards. Buyers can conduct these audits themselves or hire third-party services.
- Quality Assurance Reports: Requesting detailed quality assurance reports from suppliers can provide insights into their QC processes and outcomes.
- Third-Party Inspections: Engaging third-party inspection services during production can help verify that quality standards are met throughout the manufacturing process.
QC and Certification Nuances for International Buyers
For buyers from Africa, South America, the Middle East, and Europe, understanding the nuances of quality control and certification is vital:
- Regional Regulations: Be aware of specific regional regulations that may affect quality standards. For instance, EU regulations may differ significantly from those in African markets.
- Cultural Considerations: Different regions may have varying expectations regarding product quality and design. It is crucial to communicate these expectations clearly with suppliers.
- Logistics and Supply Chain: International shipping can complicate quality assurance. Establish clear terms regarding returns and inspections upon arrival to mitigate risks.
By focusing on these manufacturing processes and quality assurance practices, B2B buyers can make informed decisions when sourcing butterfly backpacks. This comprehensive understanding not only enhances product quality but also fosters long-term relationships with reliable suppliers, ultimately contributing to business success.
Related Video: How a Backpack is Made : Every Step on the Production Line
Comprehensive Cost and Pricing Analysis for butterfly backpack Sourcing
Understanding the cost structure and pricing dynamics of butterfly backpack sourcing is crucial for international B2B buyers looking to optimize their purchasing decisions. Below is a comprehensive analysis of the various cost components, pricing influencers, and actionable buyer tips that can guide you through this process.
Cost Components
-
Materials
The choice of materials significantly impacts the overall cost of the butterfly backpack. High-quality fabrics (like nylon or polyester), zippers, and buckles are essential for durability. Expect to pay more for eco-friendly materials or specialized fabrics that offer water resistance or enhanced durability. -
Labor
Labor costs vary by region and affect the overall pricing of the backpacks. Countries with higher labor costs, such as those in Europe, will naturally have higher production costs compared to regions like Southeast Asia or parts of Africa. When sourcing, consider the balance between labor cost and the quality of workmanship. -
Manufacturing Overhead
This includes the costs associated with running the manufacturing facility, such as utilities, rent, and equipment maintenance. Manufacturers with advanced machinery may charge higher overhead, but this often translates to better quality and efficiency. -
Tooling
Tooling costs relate to the setup needed for production, particularly if you are customizing designs. This can be a significant upfront investment, especially for small order quantities. Discuss tooling costs upfront to ensure you understand the implications for your budget. -
Quality Control (QC)
Investing in quality control is essential to avoid costly returns and brand damage. QC processes can add to the overall cost but are critical for ensuring that the products meet international standards. Consider including QC in your sourcing strategy to mitigate risks. -
Logistics
Shipping costs can vary widely depending on the mode of transport (air vs. sea), distance, and the chosen Incoterms. For international buyers, understanding these logistics costs is crucial for accurate pricing. -
Margin
Suppliers will add their profit margin to the base costs, which can vary significantly based on their market position and the value they provide. Always inquire about the margin to better understand the pricing structure.
Price Influencers
-
Volume/MOQ
The minimum order quantity (MOQ) can affect pricing significantly. Larger orders typically benefit from economies of scale, reducing the per-unit cost. Negotiate MOQs that suit your business needs without overcommitting. -
Specifications/Customization
Customized designs will generally incur additional costs related to design adjustments, tooling, and production time. Ensure that any customization requests are clearly communicated to avoid unexpected costs. -
Materials and Quality Certifications
Higher-quality materials and certifications (like eco-friendly labels or safety standards) can drive up costs. However, they can also enhance product appeal and marketability, justifying the investment.
-
Supplier Factors
Supplier reputation, experience, and relationship can influence pricing. Established suppliers may charge a premium for their reliability, while newer manufacturers might offer lower prices to attract business. -
Incoterms
The chosen Incoterms (e.g., FOB, CIF) can greatly affect logistics costs and responsibilities. Familiarize yourself with these terms to negotiate better deals and understand the total cost of ownership.
Buyer Tips
-
Negotiate Wisely: Always negotiate pricing, considering both quality and cost. Building a strong relationship with suppliers can lead to better deals and flexibility.
-
Consider Total Cost of Ownership (TCO): Look beyond the purchase price. Include factors like shipping, duty, and potential returns in your calculations to understand the complete financial impact.
-
Adapt to Local Markets: For buyers in Africa or South America, consider sourcing locally to reduce logistics costs and support regional economies. This can also enhance brand loyalty among local consumers.
-
Stay Informed on Pricing Nuances: Global economic factors, currency fluctuations, and trade policies can influence pricing. Keeping abreast of these factors will help you make informed purchasing decisions.
Disclaimer
Prices can vary widely based on numerous factors including supplier relationships, market conditions, and specific requirements. Always request detailed quotes from multiple suppliers to ensure you are getting a competitive price.
Spotlight on Potential butterfly backpack Manufacturers and Suppliers
This section offers a look at a few manufacturers active in the ‘butterfly backpack’ market. This is a representative sample for illustrative purposes; B2B buyers must conduct their own extensive due diligence before any engagement. Information is synthesized from public sources and general industry knowledge.
Essential Technical Properties and Trade Terminology for butterfly backpack
Key Technical Properties of Butterfly Backpacks
When sourcing butterfly backpacks, understanding their technical properties is crucial for ensuring product quality and customer satisfaction. Here are some essential specifications that B2B buyers should consider:
-
Material Grade
– Definition: This refers to the type and quality of materials used in the construction of the backpack, such as nylon, polyester, or canvas.
– Importance: Higher-grade materials typically offer better durability, water resistance, and overall performance. Investing in quality materials can reduce returns and enhance brand reputation. -
Load Capacity
– Definition: The maximum weight the backpack can safely carry, often measured in liters or kilograms.
– Importance: Understanding load capacity is vital for targeting specific markets (e.g., hiking, school, travel). Products that fail to meet expectations in this area can lead to customer dissatisfaction and damage to your brand. -
Tolerance Levels
– Definition: The permissible limits of variation in the dimensions and specifications of the backpack components.
– Importance: Ensuring tight tolerances is critical for maintaining product consistency and fit. Poor tolerances can result in misaligned zippers, buckles, and overall functionality, leading to customer complaints. -
Stitching Quality
– Definition: The method and quality of stitching used in the assembly of the backpack, including the number of stitches per inch and types of stitches (e.g., double-stitching, bar tacks).
– Importance: Strong and consistent stitching is crucial for durability, especially at stress points. High-quality stitching minimizes the risk of seams coming apart, which is a common failure point in backpacks. -
Water Resistance Rating
– Definition: A measure of the backpack’s ability to repel water, often indicated by a waterproof rating (e.g., IPX4).
– Importance: As outdoor and travel gear, the ability to withstand rain or spills is a significant selling point. Products with inadequate water resistance can lead to damage of contents and dissatisfied customers. -
Weight
– Definition: The total weight of the backpack itself, usually measured in grams or pounds.
– Importance: A lighter backpack is often preferred for comfort and ease of transport. Buyers should balance weight with durability to meet the needs of their target market.
Common Trade Terminology
Navigating the trade landscape requires familiarity with specific jargon. Here are several key terms relevant to B2B buyers of butterfly backpacks:
-
OEM (Original Equipment Manufacturer)
– Definition: A company that produces parts or equipment that may be marketed by another manufacturer.
– Importance: Understanding OEM relationships can help buyers leverage existing designs and capabilities, ensuring they receive products that meet their specifications without starting from scratch. -
MOQ (Minimum Order Quantity)
– Definition: The smallest amount of product that a supplier is willing to sell.
– Importance: Knowing the MOQ helps buyers plan their budgets and inventory levels. Suppliers with low MOQs may be ideal for startups or those testing new products. -
RFQ (Request for Quotation)
– Definition: A document sent to suppliers requesting a quote for specific products or services.
– Importance: An effective RFQ can streamline the sourcing process, allowing buyers to compare prices and terms from multiple suppliers efficiently. -
Incoterms (International Commercial Terms)
– Definition: A series of predefined commercial terms published by the International Chamber of Commerce (ICC) that clarify the responsibilities of buyers and sellers.
– Importance: Familiarity with Incoterms is essential for understanding shipping costs and responsibilities. Terms like FOB (Free On Board) or CIF (Cost, Insurance, and Freight) impact total landed costs. -
Lead Time
– Definition: The amount of time from placing an order to receiving the product.
– Importance: Knowing lead times is critical for inventory management and planning. Longer lead times can affect sales strategies and customer satisfaction. -
Quality Assurance (QA)
– Definition: A systematic process to ensure that products meet specified requirements and standards.
– Importance: Implementing robust QA processes helps prevent defects and ensures that the products delivered meet the quality expectations of buyers and end consumers.
Understanding these properties and terms will empower B2B buyers to make informed decisions when sourcing butterfly backpacks, ensuring they choose products that align with their business goals and customer needs.
Navigating Market Dynamics, Sourcing Trends, and Sustainability in the butterfly backpack Sector
Market Overview & Key Trends
The global butterfly backpack market is experiencing significant growth, driven by increasing consumer demand for versatile and stylish bags suitable for various occasions. This trend is particularly prominent in regions such as Africa, South America, the Middle East, and Europe, where urbanization and a growing middle class are creating new opportunities for retailers and wholesalers. B2B buyers should note the rise of e-commerce, which is reshaping how backpacks are marketed and sold. Online platforms facilitate direct-to-consumer sales, allowing brands to reach a broader audience and reduce dependency on traditional retail channels.
Emerging technologies are also influencing sourcing trends. Digital platforms like Sourcify and Alibaba are simplifying the process of finding reliable manufacturers, reducing lead times, and optimizing costs. B2B buyers can leverage these platforms to compare suppliers, request samples, and negotiate pricing effectively. Additionally, the rise of data analytics in supply chain management helps buyers make informed decisions based on consumer behavior and market trends. As competition intensifies, suppliers that offer customization options and quick turnaround times are becoming increasingly attractive to international buyers.
Understanding regional dynamics is essential. For instance, buyers in Africa may face unique challenges related to logistics and infrastructure, while those in Europe might prioritize sustainability and ethical sourcing. Recognizing these market nuances will enable B2B buyers to tailor their strategies effectively and build long-lasting supplier relationships.
Sustainability & Ethical Sourcing in B2B
Sustainability has become a cornerstone of modern backpack manufacturing, with increasing pressure on brands to minimize their environmental footprint. The butterfly backpack sector is no exception, as consumers increasingly favor products made from eco-friendly materials and produced through sustainable practices. B2B buyers should prioritize suppliers who demonstrate a commitment to sustainable sourcing, such as using recycled materials and adopting waste-reduction strategies in production.
Ethical supply chains are equally important. Buyers must ensure that their suppliers comply with labor laws and provide fair working conditions. This not only mitigates reputational risks but also aligns with the growing consumer preference for brands that prioritize social responsibility. Certifications such as Global Organic Textile Standard (GOTS) and OEKO-TEX® can serve as reliable indicators of a supplier’s commitment to sustainability and ethical practices.
Investing in sustainable materials, such as organic cotton or recycled polyester, can enhance a brand’s image and appeal to environmentally conscious consumers. B2B buyers should actively seek out suppliers who can provide documentation of their sustainable practices and materials, ensuring that their sourcing aligns with both market trends and consumer values.
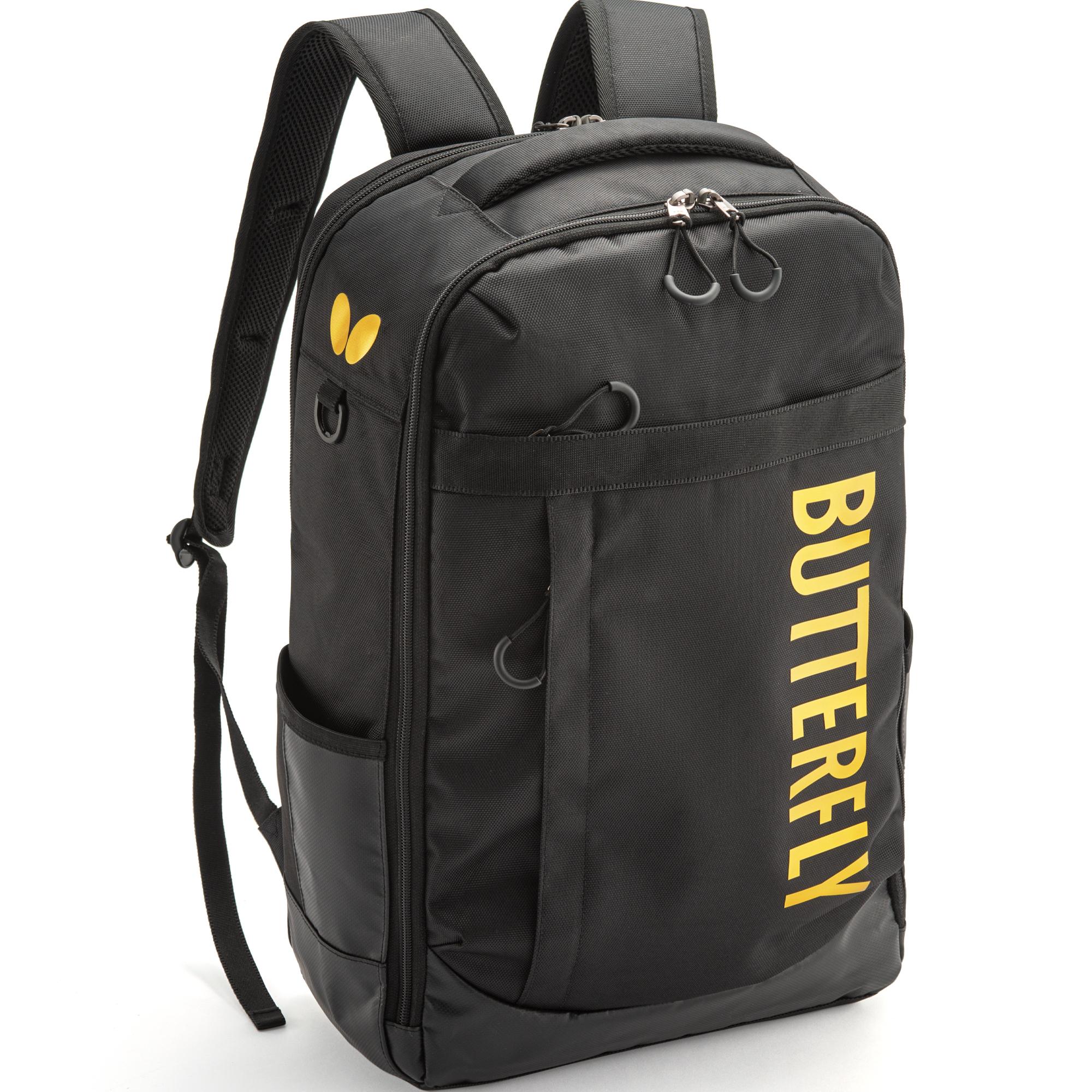
Illustrative Image (Source: Google Search)
Brief Evolution/History
The butterfly backpack has evolved from simple, utilitarian designs to fashionable accessories that reflect personal style and functionality. Initially popularized by outdoor enthusiasts, the design has gained traction in urban environments, driven by the need for practical yet stylish solutions for daily commuting and travel. The rise of social media and influencer marketing has also played a pivotal role in shaping consumer perceptions and driving demand for unique, eye-catching designs.
In recent years, the focus has shifted towards customization and personalization, with brands offering options that cater to individual preferences. This evolution has opened new avenues for B2B buyers, allowing them to source diverse products that meet the specific needs of their target markets. As the butterfly backpack continues to adapt to changing consumer preferences, B2B buyers must stay attuned to these trends to remain competitive in the marketplace.
Related Video: International Trade 101 | Economics Explained
Frequently Asked Questions (FAQs) for B2B Buyers of butterfly backpack
-
How can I effectively vet suppliers for butterfly backpacks?
Vetting suppliers is crucial to ensure product quality and reliability. Start by researching potential suppliers through platforms like Alibaba or Sourcify, focusing on their experience, customer reviews, and product range. Request samples to assess material quality and craftsmanship. Additionally, verify certifications such as ISO and compliance with international quality standards. Consider visiting factories, if feasible, to conduct in-person evaluations. Engaging with industry peers for recommendations can also provide valuable insights into trustworthy suppliers. -
What customization options are available for butterfly backpacks?
Many manufacturers offer a range of customization options for butterfly backpacks, including fabric choices, colors, sizes, and design features. When discussing customization, provide clear specifications and design prototypes to the supplier. Ensure that the manufacturer has the capacity and expertise to accommodate your requests. It’s also beneficial to inquire about the minimum order quantities (MOQs) for customized products, as this can vary significantly between suppliers. -
What are the typical minimum order quantities (MOQ) and lead times for butterfly backpacks?
MOQs for butterfly backpacks can range from as low as 100 units to several thousand, depending on the manufacturer and the complexity of the design. Lead times typically range from 30 to 90 days, influenced by factors like production capacity and order volume. Always confirm these details upfront to align your inventory management with the supplier’s timelines. For urgent needs, some suppliers may offer expedited production for an additional fee.
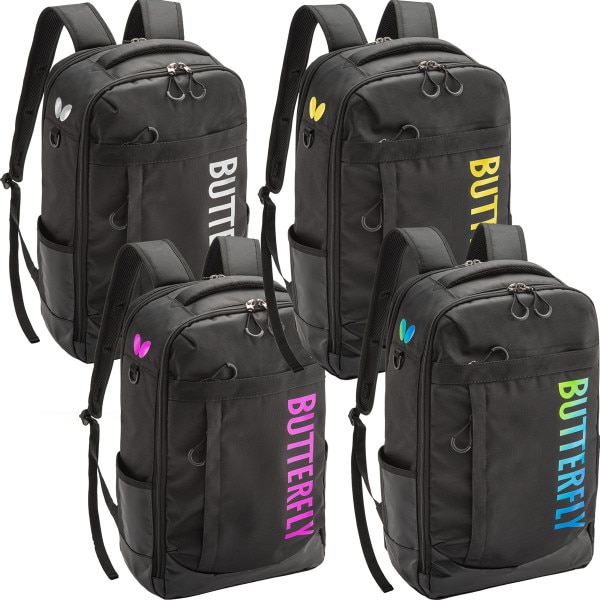
Illustrative Image (Source: Google Search)
-
What payment terms should I expect when sourcing butterfly backpacks?
Payment terms can vary widely among suppliers. Common practices include a 30% deposit upfront with the balance due before shipment, or payment in full upon delivery. Utilize secure payment methods such as PayPal or letters of credit to mitigate risks. Ensure that the payment terms are clearly outlined in the contract to avoid disputes later. Negotiating favorable terms can also be beneficial, especially for repeat orders. -
How can I ensure quality assurance and certification for the backpacks?
To ensure quality assurance, request detailed quality control procedures from your supplier. This should include pre-production samples, inline inspections, and final inspections before shipping. Certifications like ISO 9001 or compliance with specific safety standards (e.g., REACH, CPSIA) can further assure you of the product’s quality. Consider hiring third-party inspection services to verify compliance and quality before shipment, especially for large orders. -
What logistics considerations should I be aware of when importing butterfly backpacks?
Logistics is a critical aspect of sourcing. Consider shipping methods (air vs. sea), as air freight is faster but more expensive, while sea freight is cost-effective for larger shipments. Familiarize yourself with import duties and taxes applicable in your region to avoid unexpected costs. Work with a reliable freight forwarder who can handle customs clearance and provide tracking throughout the shipping process. This will help ensure timely delivery and compliance with local regulations. -
How should I handle disputes with suppliers?
Disputes can arise over quality issues, delays, or payment terms. To handle disputes effectively, maintain clear and documented communication throughout the sourcing process. If issues arise, address them promptly and directly with the supplier, referencing your contract and any agreed-upon quality standards. If resolution is not achieved, consider mediation or arbitration as stipulated in your agreement. Establishing a positive working relationship from the outset can also help mitigate conflicts. -
What are the trends influencing the butterfly backpack market internationally?
The butterfly backpack market is influenced by trends such as sustainability, with a growing demand for eco-friendly materials and ethical manufacturing processes. Consumers are also increasingly looking for multifunctional designs that offer versatility for various uses. Additionally, the rise of e-commerce is driving demand for unique and customizable products. B2B buyers should stay informed about these trends to align their offerings with market demands and enhance their competitive edge.
Strategic Sourcing Conclusion and Outlook for butterfly backpack
The strategic sourcing of butterfly backpacks presents a unique opportunity for international B2B buyers, particularly in regions like Africa, South America, the Middle East, and Europe. Key takeaways include the importance of selecting high-quality materials, ensuring robust stitching, and prioritizing ergonomic design to meet consumer expectations. By being proactive in quality assurance—through rigorous testing and supplier assessments—buyers can mitigate risks associated with poor product performance and enhance their brand reputation.
The value of strategic sourcing cannot be overstated. Not only does it streamline production processes, but it also allows businesses to capitalize on cost efficiencies while maintaining product quality. Engaging directly with reputable manufacturers, rather than intermediaries, can further reduce lead times and improve communication.
As the global market for backpacks continues to evolve, now is the time for B2B buyers to leverage these insights and make informed sourcing decisions. Act now to connect with reliable suppliers and position your brand for success in a competitive landscape. Embrace the future of backpack sourcing with confidence, ensuring your offerings resonate with consumers and stand out in the marketplace.