Master Sourcing the Best Tool Pouch Backpack for Your
Guide to Tool Pouch Backpack
- Introduction: Navigating the Global Market for tool pouch backpack
- Understanding tool pouch backpack Types and Variations
- Key Industrial Applications of tool pouch backpack
- Strategic Material Selection Guide for tool pouch backpack
- In-depth Look: Manufacturing Processes and Quality Assurance for tool pouch backpack
- Comprehensive Cost and Pricing Analysis for tool pouch backpack Sourcing
- Spotlight on Potential tool pouch backpack Manufacturers and Suppliers
- Essential Technical Properties and Trade Terminology for tool pouch backpack
- Navigating Market Dynamics, Sourcing Trends, and Sustainability in the tool pouch backpack Sector
- Frequently Asked Questions (FAQs) for B2B Buyers of tool pouch backpack
- Strategic Sourcing Conclusion and Outlook for tool pouch backpack
Introduction: Navigating the Global Market for tool pouch backpack
In today’s fast-paced global economy, the tool pouch backpack has emerged as an indispensable asset for professionals across various sectors, from construction to maintenance and engineering. This versatile product not only offers convenience and organization but also enhances productivity by allowing workers to carry essential tools securely and accessibly. As international B2B buyers, particularly from Africa, South America, the Middle East, and Europe, understanding the intricacies of sourcing tool pouch backpacks is critical for maximizing operational efficiency and profitability.
This comprehensive guide delves into the myriad aspects of the tool pouch backpack market, including types, materials, and manufacturing and quality control standards. Buyers will gain insights into reputable suppliers, cost structures, and current market trends, enabling them to make informed decisions that align with their specific needs.
Furthermore, the guide addresses frequently asked questions, providing clarity on critical considerations such as lead times, minimum order quantities, and compliance with international standards. By leveraging the knowledge presented in this guide, B2B buyers can navigate the complexities of global sourcing effectively, ensuring they select products that meet both quality and budgetary requirements. Empower yourself with the insights necessary to thrive in the competitive landscape of tool pouch backpacks, and elevate your procurement strategy today.
Understanding tool pouch backpack Types and Variations
Type Name | Key Distinguishing Features | Primary B2B Applications | Brief Pros & Cons for Buyers |
---|---|---|---|
Traditional Tool Backpack | Multiple compartments, padded for comfort | Construction, plumbing, electrical work | Pros: Durable, versatile; Cons: Can be bulky, heavier |
Multi-Pocket Organizer | Numerous pockets for small tools and accessories | HVAC, automotive repair, maintenance services | Pros: Great organization; Cons: Limited space for larger tools |
Heavy-Duty Tool Pouch | Reinforced materials, weather-resistant | Heavy machinery maintenance, outdoor work | Pros: Exceptional durability; Cons: Higher price point |
Compact Tool Carrier | Lightweight, ergonomic design | Landscaping, small repairs, DIY projects | Pros: Easy to carry; Cons: Limited storage capacity |
Specialized Tool Backpack | Designed for specific trades (e.g., electricians) | Specialized fields (e.g., IT, telecommunications) | Pros: Tailored features; Cons: May lack versatility |
Traditional Tool Backpack
The traditional tool backpack is characterized by its spacious interior and multiple compartments designed to hold a variety of tools securely. Ideal for sectors like construction, plumbing, and electrical work, these backpacks provide ample storage while ensuring comfort during transport. When purchasing, consider the material quality for durability, the number of compartments for organization, and weight, as heavier models can lead to fatigue.
Multi-Pocket Organizer
This type features numerous pockets and slots, specifically designed to hold small tools and accessories. It is particularly beneficial for industries such as HVAC, automotive repair, and maintenance services, where organization is crucial. Buyers should evaluate the size and arrangement of pockets, ensuring they meet the specific needs of their trade while also considering the backpack’s overall weight and ease of access.
Heavy-Duty Tool Pouch
Heavy-duty tool pouches are made from reinforced materials and are often weather-resistant, making them suitable for heavy machinery maintenance and outdoor work. Their robust construction ensures they can withstand demanding environments. B2B buyers should focus on material specifications, warranty options, and the pouch’s ability to protect tools from environmental factors when making a purchasing decision.
Compact Tool Carrier
Designed for easy portability, compact tool carriers are lightweight and ergonomically shaped. They are particularly advantageous for landscaping, small repairs, and DIY projects where mobility is essential. When sourcing these carriers, buyers should consider the balance between size and storage capacity, as well as the comfort of carrying straps, which can impact usability during extended use.
Specialized Tool Backpack
These backpacks are crafted with specific trades in mind, such as those needed for electricians or telecommunications professionals. They often include tailored features like built-in cable management or tool-specific compartments. For buyers in specialized fields, assessing the functional benefits versus the general utility of more versatile options is crucial. Additionally, consider the balance between price and the unique features that cater to specific job requirements.
Key Industrial Applications of tool pouch backpack
Industry/Sector | Specific Application of Tool Pouch Backpack | Value/Benefit for the Business | Key Sourcing Considerations for this Application |
---|---|---|---|
Construction | On-site tool organization | Enhanced efficiency and reduced downtime | Durability, weather resistance, and ergonomic design |
Electrical & Electronics | Cable and tool management | Improved safety and reduced risk of damage | Material quality, weight capacity, and compliance with standards |
Automotive Repair | Mobile tool access | Increased productivity and reduced tool loss | Customization options, material strength, and price competitiveness |
HVAC Services | Transport of specialized tools | Streamlined workflow and better job site organization | Vendor reliability, lead times, and warranty policies |
Landscaping & Gardening | Tool storage and transport | Enhanced mobility and organization on job sites | Quality of materials, water resistance, and size options |
Construction
In the construction industry, tool pouch backpacks are essential for on-site tool organization. Workers can carry multiple tools and accessories, ensuring that they have everything needed for the task at hand. This organization reduces downtime and increases efficiency, allowing projects to stay on schedule. Buyers should prioritize durability and weather resistance, as these backpacks will be exposed to harsh conditions. Ergonomic design is also crucial, as it enhances comfort during prolonged use.
Electrical & Electronics
In electrical and electronics sectors, tool pouch backpacks serve as effective cable and tool management systems. These backpacks provide organized compartments for various tools, reducing the risk of damage to sensitive equipment. By ensuring that tools are easily accessible, businesses can improve safety and efficiency. When sourcing, international buyers should look for high-quality materials that meet safety standards, as well as options that offer adequate weight capacity.
Automotive Repair
For automotive repair businesses, tool pouch backpacks facilitate mobile tool access, allowing mechanics to carry essential tools directly to the vehicle. This mobility leads to increased productivity and minimizes the risk of tool loss on the job site. Buyers in this sector should consider customization options that allow for specific tool storage needs. Material strength is also a key factor, as the bags must withstand frequent use and heavy loads while remaining competitively priced.
HVAC Services
HVAC technicians utilize tool pouch backpacks to transport specialized tools required for installation and maintenance. The ability to keep tools organized and accessible streamlines workflow and enhances job site organization. International buyers should focus on vendor reliability and lead times to ensure that their supplies are consistent and timely. Warranty policies can also provide added assurance regarding the quality of the products being sourced.
Landscaping & Gardening
In landscaping and gardening, tool pouch backpacks are invaluable for storing and transporting various tools. The enhanced mobility allows professionals to work more efficiently across different job sites. Buyers should pay attention to the quality of materials, especially water resistance, to ensure longevity in outdoor environments. Additionally, size options are crucial, as different jobs may require varying amounts of tools and equipment.
Related Video: ToughBuilt® Large Tool Tote
Strategic Material Selection Guide for tool pouch backpack
When selecting materials for tool pouch backpacks, international B2B buyers must consider several factors, including durability, cost, and application suitability. Below is an analysis of four common materials used in the manufacturing of tool pouch backpacks, highlighting their properties, advantages, disadvantages, and specific considerations for buyers in Africa, South America, the Middle East, and Europe.
1. Polyester
Key Properties:
Polyester is known for its excellent durability and resistance to stretching and shrinking. It has a high tensile strength and can withstand a wide range of temperatures, making it suitable for various environments.
Pros & Cons:
The material is lightweight and cost-effective, making it a popular choice for tool pouches. However, it may not be as breathable as other fabrics, which can lead to moisture retention. Additionally, while polyester is resistant to most chemicals, it can degrade under prolonged exposure to UV light.
Impact on Application:
Polyester is compatible with a variety of media, including tools and equipment that may have sharp edges, as it can resist tearing.
Considerations for International Buyers:
Buyers should ensure that the polyester used meets international standards such as ASTM D5034 for tearing strength. Additionally, sourcing from manufacturers who comply with environmental regulations is essential, especially in regions with strict sustainability policies.
2. Nylon
Key Properties:
Nylon is renowned for its exceptional strength and abrasion resistance. It has a high melting point and is resistant to mildew and rot, making it suitable for outdoor applications.
Pros & Cons:
While nylon offers superior durability and is lightweight, it can be more expensive than polyester. Its production process is also more complex, which may affect lead times and costs for buyers.
Impact on Application:
Nylon is particularly effective for tool pouches that require high resistance to wear and tear, making it ideal for heavy-duty use.
Considerations for International Buyers:
Nylon products should adhere to standards such as JIS L 1096 for fabric testing. Buyers should also be aware of the sourcing implications, as nylon production can involve significant environmental impacts.
3. Canvas
Key Properties:
Canvas is a heavy-duty fabric known for its durability and resistance to wear. It is typically made from cotton or a blend of cotton and synthetic fibers, offering good breathability and comfort.
Pros & Cons:
Canvas is highly durable and can withstand heavy loads, making it suitable for tool pouches. However, it is heavier than synthetic materials and may require more care to maintain its appearance over time.
Impact on Application:
Canvas is compatible with various tools and can provide a rugged aesthetic, appealing to buyers looking for both functionality and style.
Considerations for International Buyers:
Buyers should check for compliance with standards like DIN EN 12127 for water permeability, especially in regions with high humidity. The sourcing of organic cotton can also be a selling point in markets focused on sustainability.
4. Leather
Key Properties:
Leather is a natural material known for its strength, flexibility, and aesthetic appeal. It offers excellent durability and can withstand significant wear and tear.
Pros & Cons:
Leather provides a premium look and feel, making it a favored choice for high-end tool pouches. However, it is generally more expensive and requires special care to maintain its condition.
Impact on Application:
Leather is suitable for tools that need to be stored securely and can offer additional protection against impacts.
Considerations for International Buyers:
Buyers should ensure that leather products comply with environmental standards such as REACH in Europe. The sourcing of ethically produced leather is increasingly important in many markets.
Summary Table
Material | Typical Use Case for tool pouch backpack | Key Advantage | Key Disadvantage/Limitation | Relative Cost (Low/Med/High) |
---|---|---|---|---|
Polyester | General-purpose tool pouches for various tools | Lightweight and cost-effective | Less breathable, UV degradation | Low |
Nylon | Heavy-duty tool pouches for industrial use | Superior strength and abrasion resistance | Higher cost, complex manufacturing | Medium |
Canvas | Casual and rugged tool pouches for everyday use | Durable and aesthetically pleasing | Heavier, requires maintenance | Medium |
Leather | Premium tool pouches for high-end markets | Exceptional durability and style | Expensive, requires special care | High |
This material selection guide serves as a strategic resource for international B2B buyers, enabling them to make informed decisions based on their specific needs and market conditions.
In-depth Look: Manufacturing Processes and Quality Assurance for tool pouch backpack
Manufacturing a tool pouch backpack involves a series of well-defined processes and stringent quality assurance measures. Understanding these stages is essential for international B2B buyers, especially those from regions like Africa, South America, the Middle East, and Europe, to ensure they are sourcing high-quality products that meet industry standards.
Manufacturing Processes
1. Material Preparation
The first step in manufacturing a tool pouch backpack is the preparation of materials. Common materials include durable fabrics such as nylon, polyester, and canvas, along with high-quality zippers, buckles, and padding.
- Material Selection: B2B buyers should prioritize suppliers who use high-grade materials that provide strength and resistance to wear and tear.
- Cutting: After selection, materials are cut into specified shapes and sizes. This can be done using automated cutting machines or manual methods, depending on the production scale.
2. Forming
Forming involves shaping the cut materials into the components of the backpack. This includes creating the main body, pockets, and straps.
- Sewing Techniques: Various sewing techniques are used, such as double stitching for added durability and reinforced stitching at stress points.
- Heat Sealing: In some cases, heat sealing is employed for waterproofing seams, which is particularly important for tool pouches used in demanding environments.
3. Assembly
Once the components are formed, they are assembled into the final product. This stage combines all parts into a cohesive unit.
- Quality Control During Assembly: Implementing in-process quality control (IPQC) is vital during assembly to catch any defects early. This includes checking for correct alignment, seam strength, and overall assembly integrity.
- Ergonomic Design Considerations: B2B buyers should also consider ergonomics during assembly to ensure comfort for end-users, particularly for tool pouches that may be worn for extended periods.
4. Finishing
The final stage involves adding finishing touches to the backpack.
- Trimming and Cleaning: Excess threads are trimmed, and the backpack is cleaned to ensure a polished look.
- Final Inspection: Before packing, a final inspection is crucial. This includes checking for cosmetic defects, functionality of zippers and straps, and overall quality.
Quality Assurance
Ensuring quality in the manufacturing process is critical for maintaining product integrity and meeting customer expectations. B2B buyers should familiarize themselves with relevant international standards and quality control checkpoints.
International Standards
- ISO 9001: This standard outlines requirements for a quality management system (QMS) and is essential for suppliers to demonstrate their commitment to quality.
- CE Marking: For European buyers, CE marking indicates compliance with safety and environmental standards, which can be crucial for market access.
Quality Control Checkpoints
- Incoming Quality Control (IQC): This step involves inspecting raw materials upon arrival to ensure they meet specifications before production begins. Buyers should verify that suppliers have robust IQC processes in place.
- In-Process Quality Control (IPQC): Continuous monitoring during the manufacturing process helps catch defects early. This includes regular checks on stitching quality, material integrity, and assembly accuracy.
- Final Quality Control (FQC): The final inspection ensures that each backpack meets the specified quality standards before shipping. This includes functionality tests for zippers and buckles, as well as visual inspections for any cosmetic defects.
Common Testing Methods
B2B buyers should be aware of various testing methods that can be employed to ensure quality:
– Tensile Strength Testing: Measures the strength of materials under tension, ensuring they can withstand the weight of tools.
– Water Resistance Testing: Important for tool pouches that may be exposed to moisture; this testing assesses the effectiveness of waterproof materials and seals.
– Zipper Durability Testing: Checks the reliability of zippers under repeated use, ensuring they do not fail during operation.
Verifying Supplier Quality Control
To ensure that suppliers maintain high-quality standards, B2B buyers can adopt several strategies:
- Supplier Audits: Conduct regular audits of suppliers’ manufacturing facilities to assess their quality control processes and overall compliance with international standards.
- Quality Reports: Request detailed quality reports that outline the findings from IQC, IPQC, and FQC stages. These reports should provide insight into defect rates and corrective actions taken.
- Third-Party Inspections: Engage third-party inspection services to provide an unbiased assessment of product quality before shipment. This is particularly useful for buyers in regions where quality discrepancies are common.
QC and Certification Nuances for International Buyers
International buyers should be aware of specific nuances related to quality assurance and certification:
- Cultural Differences: Understanding cultural attitudes toward quality and business practices in regions like Africa and South America can help in negotiating terms and ensuring compliance.
- Local Regulations: Different countries may have specific regulations regarding product safety and environmental impact. Buyers should ensure that their suppliers are compliant with local laws to avoid potential legal issues.
- Communication: Effective communication with suppliers regarding quality expectations is crucial. Buyers should establish clear guidelines and expectations related to quality standards from the outset.
In conclusion, understanding the manufacturing processes and quality assurance measures for tool pouch backpacks is essential for international B2B buyers. By focusing on material quality, manufacturing techniques, and robust quality control systems, buyers can ensure they are sourcing high-quality products that meet their needs.
Related Video: How a Backpack is Made : Every Step on the Production Line
Comprehensive Cost and Pricing Analysis for tool pouch backpack Sourcing
When sourcing tool pouch backpacks, B2B buyers must navigate a complex cost structure that encompasses various components, each influencing the overall pricing. Understanding these components and the factors that affect pricing is essential for making informed purchasing decisions.
Cost Components
-
Materials: The choice of materials significantly impacts the cost. High-quality fabrics such as nylon or polyester may increase expenses but enhance durability. Additionally, eco-friendly materials can command a premium price due to their perceived value and sustainability certifications.
-
Labor: Labor costs vary by region. Countries like China and Vietnam offer competitive labor rates but may differ in the quality of craftsmanship. In contrast, sourcing from regions known for artisanal skills, such as India, may lead to higher labor costs but can provide superior craftsmanship.
-
Manufacturing Overhead: This includes factory operation costs such as utilities, rent, and administrative expenses. Efficient manufacturing plants can reduce overhead, impacting the final price favorably.
-
Tooling: Initial tooling costs can be significant, especially for custom designs. Buyers should consider these costs in relation to their order volumes, as higher volumes can amortize tooling expenses over more units, reducing the per-unit cost.
-
Quality Control (QC): Implementing stringent QC processes is essential to ensure product quality. However, these measures add to the overall cost. Buyers should evaluate the QC standards of potential suppliers to balance quality and cost.
-
Logistics: Shipping costs vary based on distance, shipping methods, and Incoterms. Choosing the right shipping terms (e.g., FOB, CIF) can significantly affect total costs. For international shipments, understanding local tariffs and customs fees is crucial to avoid unexpected expenses.
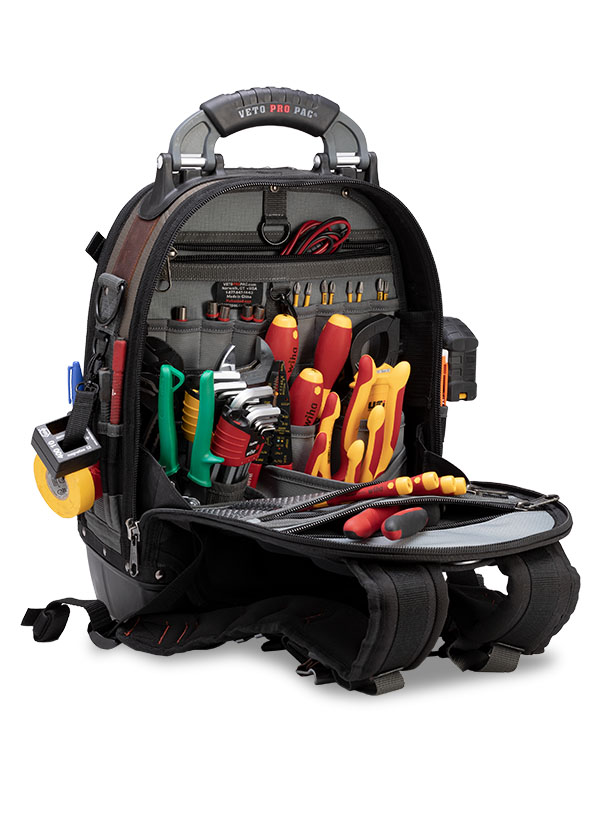
Illustrative Image (Source: Google Search)
- Margin: Suppliers typically include a profit margin in their pricing. This margin can vary widely based on the supplier’s market position, brand reputation, and the perceived value of the product.
Price Influencers
Several factors can influence the pricing of tool pouch backpacks:
-
Volume/MOQ: Larger order volumes often lead to reduced per-unit costs due to economies of scale. Negotiating minimum order quantities (MOQ) can help achieve better pricing.
-
Specifications/Customization: Custom designs or specific features can increase costs. Standardized products are generally more affordable.
-
Materials and Quality: Premium materials and certifications (e.g., ISO standards) can raise prices. Buyers should weigh the benefits of high-quality materials against their budget constraints.
-
Supplier Factors: Supplier reliability, communication efficiency, and historical performance can influence pricing. Establishing strong relationships with suppliers can lead to better pricing and service.
-
Incoterms: Understanding and negotiating Incoterms can significantly impact logistics costs and delivery timelines. Terms like DDP (Delivered Duty Paid) might simplify cost structures by including duties in the price.
Buyer Tips
For international B2B buyers, particularly from Africa, South America, the Middle East, and Europe, consider the following strategies:
-
Negotiation: Leverage your purchasing power by negotiating pricing based on volume, payment terms, and delivery schedules. Building a long-term relationship with suppliers can also lead to favorable terms.
-
Cost-Efficiency: Evaluate the total cost of ownership (TCO), which includes not just the purchase price but also shipping, duties, and potential returns. This holistic approach can reveal more cost-effective options.
-
Pricing Nuances: Be aware of regional pricing trends. For example, sourcing from countries with favorable trade agreements may yield better pricing. Additionally, understanding local market conditions can aid in price negotiations.
-
Disclaimer on Indicative Prices: Pricing can fluctuate based on market conditions, supplier changes, and geopolitical factors. Always seek current quotes and verify costs before finalizing purchases.
By understanding these components and factors, international B2B buyers can make strategic decisions that enhance their sourcing processes and optimize costs when purchasing tool pouch backpacks.
Spotlight on Potential tool pouch backpack Manufacturers and Suppliers
This section offers a look at a few manufacturers active in the ‘tool pouch backpack’ market. This is a representative sample for illustrative purposes; B2B buyers must conduct their own extensive due diligence before any engagement. Information is synthesized from public sources and general industry knowledge.
Essential Technical Properties and Trade Terminology for tool pouch backpack
When sourcing tool pouch backpacks for B2B purposes, understanding essential technical properties and industry terminology is crucial for making informed purchasing decisions. Below is a breakdown of key specifications and trade terms that every buyer should be familiar with.
Key Technical Properties
-
Material Grade
– Definition: The type of fabric or material used in the construction of the backpack, such as nylon, polyester, or canvas.
– Importance: Material grade affects durability, weight, water resistance, and overall quality. For heavy-duty applications, selecting a high-grade material ensures longevity and performance under challenging conditions. -
Capacity (Volume)
– Definition: The total volume the tool pouch backpack can hold, typically measured in liters.
– Importance: Buyers must assess the capacity based on the tools and equipment they intend to carry. A backpack with insufficient capacity can limit functionality, while one that is too large can lead to unnecessary bulk and weight.
-
Weight Tolerance
– Definition: The maximum weight the backpack is designed to carry without compromising structural integrity, often specified in kilograms or pounds.
– Importance: Understanding weight tolerance is critical for ensuring that the backpack can handle the intended load, thus preventing potential failures and ensuring user safety. -
Stitching Quality
– Definition: The type and density of stitching used in the construction of the backpack.
– Importance: High-quality stitching enhances the strength and durability of the backpack. Double-stitched or reinforced seams are preferable for heavy-duty use, as they reduce the risk of tearing. -
Zipper and Hardware Quality
– Definition: The quality of zippers, buckles, and other hardware components used in the backpack.
– Importance: Reliable zippers and hardware are essential for ease of use and longevity. Buyers should look for corrosion-resistant materials and smooth operation to ensure the backpack remains functional over time. -
Water Resistance Rating
– Definition: The level of water resistance provided by the materials and construction methods, often rated in millimeters (mm) of water column.
– Importance: For outdoor or industrial applications, water resistance is vital to protect tools and equipment from moisture damage. Buyers should assess the water resistance rating to match their specific environmental needs.
Common Trade Terms
-
OEM (Original Equipment Manufacturer)
– Definition: A company that produces parts or equipment that may be marketed by another manufacturer under its own brand name.
– Importance: Understanding OEM relationships can help buyers identify potential suppliers and ensure that they are sourcing from reputable manufacturers. -
MOQ (Minimum Order Quantity)
– Definition: The smallest quantity of a product that a supplier is willing to sell.
– Importance: Knowing the MOQ helps buyers plan their inventory and budget. It can also influence negotiations and relationships with suppliers, particularly for new entrants in the market. -
RFQ (Request for Quotation)
– Definition: A formal document issued by a buyer to solicit price quotes from suppliers for specific products or services.
– Importance: An RFQ enables buyers to compare pricing, terms, and capabilities from multiple suppliers, facilitating informed decision-making.
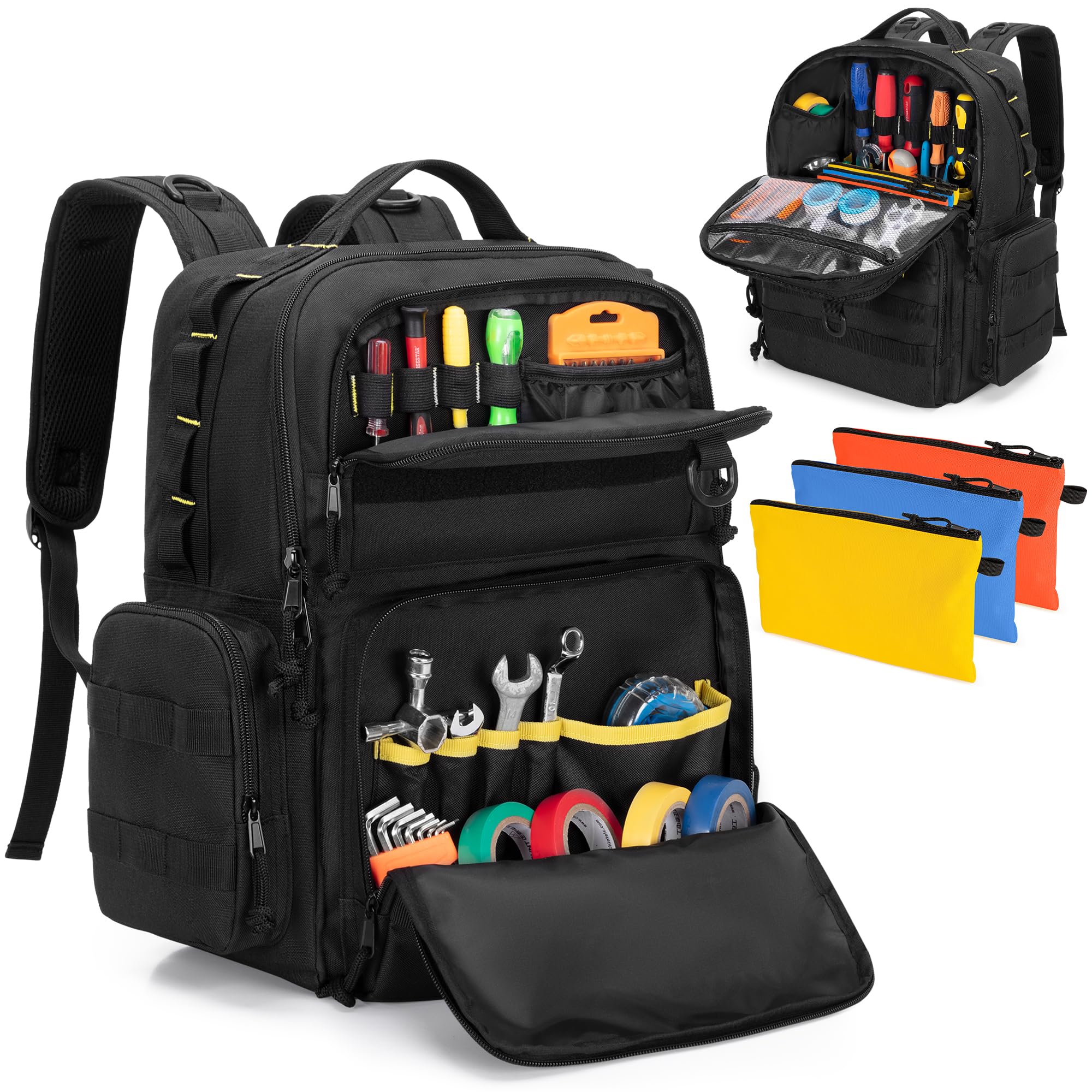
Illustrative Image (Source: Google Search)
-
Incoterms (International Commercial Terms)
– Definition: A series of predefined commercial terms published by the International Chamber of Commerce (ICC) that clarify the responsibilities of buyers and sellers in international transactions.
– Importance: Familiarity with Incoterms helps buyers understand shipping responsibilities, costs, and risks associated with transportation, ensuring smoother international transactions. -
Lead Time
– Definition: The amount of time from when an order is placed until it is delivered.
– Importance: Understanding lead times is essential for planning inventory and ensuring that products are available when needed. Buyers should consider lead times in their supply chain management strategies. -
Durability Testing
– Definition: A series of tests conducted to assess the strength and longevity of a product under various conditions.
– Importance: Buyers should inquire about durability testing standards to ensure that the tool pouch backpack will meet performance expectations in real-world applications.
By grasping these technical properties and trade terms, B2B buyers can navigate the complexities of sourcing tool pouch backpacks more effectively, ensuring they select products that meet their operational needs while maximizing value.
Navigating Market Dynamics, Sourcing Trends, and Sustainability in the tool pouch backpack Sector
Market Overview & Key Trends
The global tool pouch backpack market is experiencing significant growth, propelled by the increasing demand for durable and multifunctional storage solutions in various sectors, including construction, engineering, and outdoor activities. With a market projected to reach over $85 billion by 2030, international B2B buyers must navigate evolving trends that influence sourcing decisions. A crucial driver is the shift towards diversified sourcing strategies. Buyers are increasingly adopting the “China Plus One” approach, whereby they maintain relationships with Chinese suppliers while exploring alternatives in regions such as Vietnam, India, and Bangladesh. This diversification minimizes risk and enhances supply chain resilience.
Another emerging trend is the integration of smart technology into tool pouch backpacks. Features such as built-in charging ports, GPS tracking, and RFID protection are becoming more prevalent, appealing to tech-savvy consumers and professionals. Buyers should consider suppliers who offer these innovative designs while ensuring they align with the latest safety and quality standards.
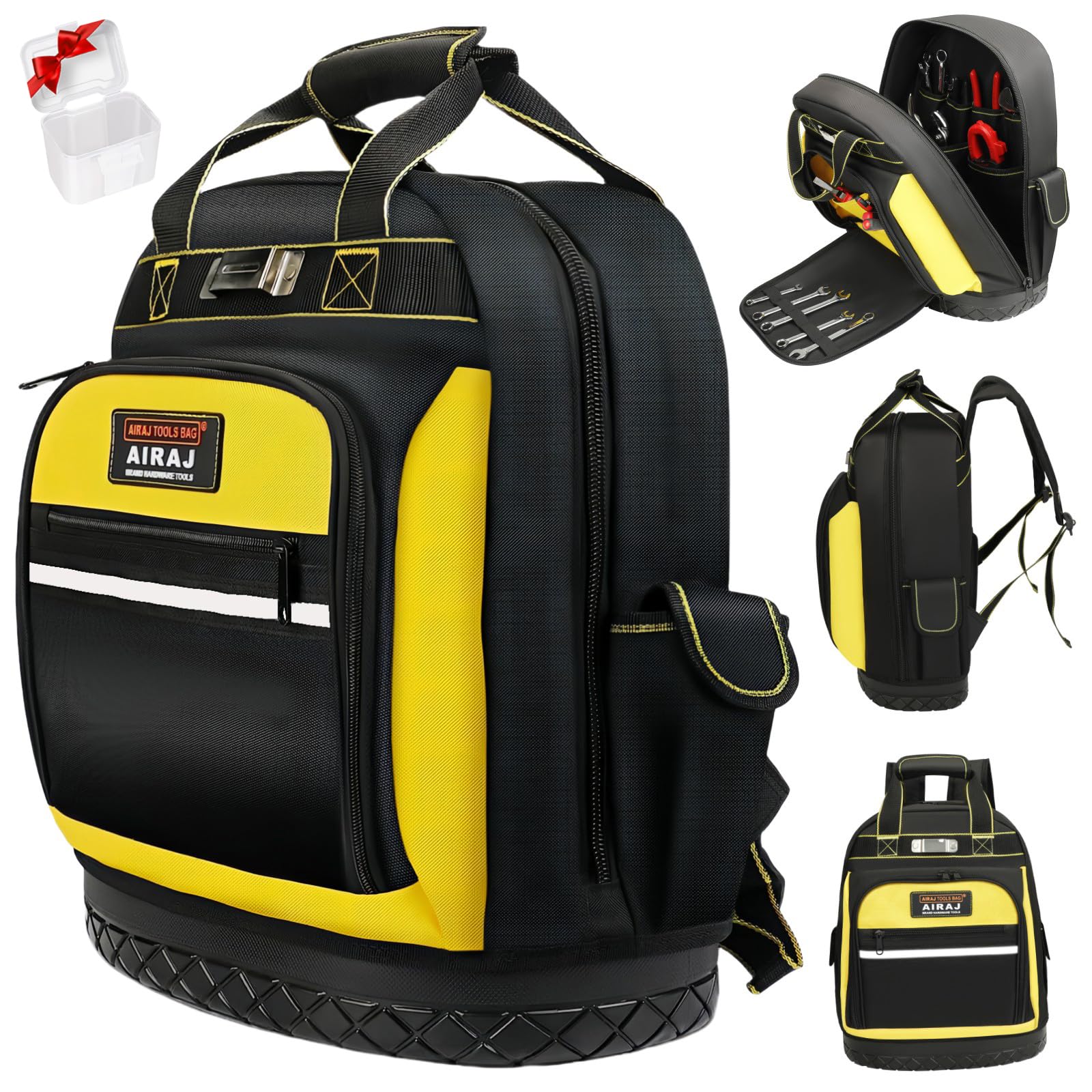
Illustrative Image (Source: Google Search)
Furthermore, sustainability is no longer an optional consideration; it is becoming a central aspect of product development and sourcing strategies. International B2B buyers are encouraged to prioritize suppliers committed to eco-friendly practices, from material sourcing to production processes. This focus on sustainability not only meets consumer demand but also enhances brand reputation in increasingly environmentally conscious markets.
Sustainability & Ethical Sourcing in B2B
Sustainability plays a pivotal role in the sourcing of tool pouch backpacks. The environmental impact of traditional manufacturing processes, including high carbon emissions and waste generation, has led to a push for ethical supply chains. Buyers must prioritize suppliers who demonstrate a commitment to sustainability through the use of eco-friendly materials, such as recycled fabrics or organic cotton, and those who comply with international labor standards.
Certifications such as Global Organic Textile Standard (GOTS) and OEKO-TEX are essential indicators of sustainability and ethical practices. These certifications ensure that materials used in production are environmentally friendly and that manufacturers adhere to fair labor practices. By sourcing from certified suppliers, B2B buyers not only mitigate risks associated with unethical practices but also appeal to a growing segment of consumers who prioritize sustainability in their purchasing decisions.
In addition, the adoption of circular economy principles is gaining traction within the industry. This approach encourages the design of products that are easily recyclable or can be repurposed, thus reducing waste. Buyers should actively seek partnerships with manufacturers that embrace these principles, as they are likely to be more adaptable to changing market demands and regulatory requirements.
Brief Evolution/History
The tool pouch backpack has evolved significantly from its early utilitarian designs to today’s multifunctional and stylish variants. Initially developed for manual laborers and tradespeople, these backpacks have transformed into essential tools for various professions and outdoor enthusiasts. The introduction of advanced materials and ergonomic designs has enhanced functionality and comfort, making them popular among diverse user groups.
Over the years, the market has seen the rise of brands that focus on niche segments, such as eco-conscious consumers or tech-savvy professionals, reflecting broader societal trends toward sustainability and innovation. As a result, B2B buyers today have access to a wide range of options that combine practicality with modern aesthetics, underscoring the importance of adaptability in sourcing strategies.
Related Video: Exim Trade Conclave 2025 LIVE | Finance Minister Nirmala Sitharaman Delivers Keynote Address | N18L
Frequently Asked Questions (FAQs) for B2B Buyers of tool pouch backpack
-
What should I consider when vetting suppliers for tool pouch backpacks?
When vetting suppliers, prioritize their experience and reputation in the industry. Check for certifications that align with international quality standards, such as ISO or specific safety certifications relevant to tool pouches. Request references from previous clients and assess their production capabilities to ensure they can meet your demand. Additionally, consider their geographic location for logistics efficiency, communication responsiveness, and cultural compatibility, which can influence the overall partnership. -
Can I customize tool pouch backpacks to fit my brand needs?
Yes, many manufacturers offer customization options for tool pouch backpacks, including materials, colors, sizes, and branding elements like logos. When considering customization, inquire about the minimum order quantities (MOQs) for customized products, as these can differ from standard offerings. Discuss your specific requirements with potential suppliers to ensure they can deliver your vision while maintaining quality and functionality. -
What are typical minimum order quantities (MOQs) and lead times for tool pouch backpacks?
MOQs for tool pouch backpacks can vary widely based on the manufacturer and product specifications, ranging from 500 to 5,000 units. Lead times typically depend on the complexity of the order and the supplier’s location, generally falling between 4 to 12 weeks. It’s crucial to confirm these details during negotiations to align your production schedules and avoid potential delays in meeting your market demands. -
What payment terms should I expect when sourcing tool pouch backpacks internationally?
Payment terms can vary significantly among suppliers, but common practices include advance payments of 30-50% with the balance due upon completion or before shipment. For larger orders, some suppliers may offer more flexible terms, such as letters of credit or payment upon delivery. Always clarify payment methods, currency considerations, and any associated fees to avoid unexpected costs and ensure financial security in the transaction. -
How can I ensure quality assurance for tool pouch backpacks?
To ensure quality assurance, request samples before placing bulk orders. Establish clear quality control standards and inspection processes, including on-site inspections or third-party quality checks. Discuss the supplier’s quality management systems and certifications, and ensure they understand your specific quality requirements. Consider including quality clauses in your contract to protect your interests and maintain product consistency. -
What certifications should I look for when sourcing tool pouch backpacks?
Look for certifications that demonstrate compliance with international safety and quality standards, such as ISO 9001 for quality management and ISO 14001 for environmental management. Additionally, check for any industry-specific certifications relevant to tool accessories, such as ANSI or CE marking, which can indicate adherence to safety regulations. These certifications can enhance your brand’s credibility and assure customers of product reliability. -
What logistics considerations should I keep in mind when importing tool pouch backpacks?
When importing tool pouch backpacks, consider shipping methods (air vs. sea), costs, customs duties, and the timeframes for delivery. Collaborate with logistics providers experienced in international shipping to navigate complexities such as tariffs and import regulations. Ensure that your supplier is familiar with shipping documentation requirements to prevent delays and complications during customs clearance. -
How can disputes with suppliers be effectively managed?
To manage disputes effectively, establish clear communication channels and protocols before any issues arise. Include dispute resolution clauses in your contracts, specifying mediation or arbitration processes. Keep detailed documentation of agreements, communications, and transactions to support your case if disputes occur. Building a strong relationship with your supplier can also facilitate amicable resolutions and foster long-term collaboration.
Strategic Sourcing Conclusion and Outlook for tool pouch backpack
In conclusion, effective strategic sourcing for tool pouch backpacks is essential for international B2B buyers looking to optimize their supply chains and enhance product offerings. The insights shared throughout this guide underline the importance of evaluating potential suppliers based on quality, reliability, and cost-effectiveness. Emphasizing a multi-country sourcing strategy allows businesses to leverage the unique strengths of different regions, whether it’s the manufacturing capabilities of China, the craftsmanship of India, or the cost advantages of Bangladesh.
As the market for tool pouch backpacks continues to grow, driven by rising demand in various sectors, it is crucial for buyers in Africa, South America, the Middle East, and Europe to remain proactive. Investing in relationships with reputable suppliers and understanding local market dynamics can significantly improve competitive positioning.
Looking ahead, the focus on sustainability and compliance with international standards will only intensify. Buyers are encouraged to seek out partners that prioritize ethical practices and environmental responsibility, ensuring long-term success and brand integrity. Start exploring your sourcing options today to capitalize on the evolving landscape of the tool pouch backpack market.