Your Ultimate Guide to Sourcing Internal Frame Backpack
Guide to Internal Frame Backpack
- Introduction: Navigating the Global Market for internal frame backpack
- Understanding internal frame backpack Types and Variations
- Key Industrial Applications of internal frame backpack
- Strategic Material Selection Guide for internal frame backpack
- In-depth Look: Manufacturing Processes and Quality Assurance for internal frame backpack
- Comprehensive Cost and Pricing Analysis for internal frame backpack Sourcing
- Spotlight on Potential internal frame backpack Manufacturers and Suppliers
- Essential Technical Properties and Trade Terminology for internal frame backpack
- Navigating Market Dynamics, Sourcing Trends, and Sustainability in the internal frame backpack Sector
- Frequently Asked Questions (FAQs) for B2B Buyers of internal frame backpack
- Strategic Sourcing Conclusion and Outlook for internal frame backpack
Introduction: Navigating the Global Market for internal frame backpack
Navigating the global market for internal frame backpacks presents a unique opportunity for international B2B buyers, particularly those operating in dynamic regions like Africa, South America, the Middle East, and Europe. These specialized backpacks are integral to various sectors, including outdoor recreation, travel, and urban commuting, providing comfort and functionality through their innovative design. As global demand continues to rise, understanding the nuances of sourcing high-quality internal frame backpacks is critical for maintaining a competitive edge.
This comprehensive guide delves into the essential aspects of internal frame backpack sourcing. It covers a wide array of topics, including the different types of backpacks available, the materials used in their construction, and the manufacturing processes that ensure quality control. Moreover, the guide will highlight reputable suppliers, provide insights into pricing structures, and analyze market trends that influence purchasing decisions.
By equipping B2B buyers with actionable insights and practical knowledge, this guide empowers them to make informed sourcing decisions. From understanding common quality issues to recognizing the importance of ergonomic designs, buyers will gain the expertise needed to enhance their product offerings. Ultimately, navigating the complexities of the internal frame backpack market can lead to improved customer satisfaction and sustained business growth.
Understanding internal frame backpack Types and Variations
Type Name | Key Distinguishing Features | Primary B2B Applications | Brief Pros & Cons for Buyers |
---|---|---|---|
Hiking Backpacks | Designed for long hikes; includes hydration systems | Outdoor retailers, adventure tours | Pros: Comfortable for long wear; Cons: May be heavier. |
Travel Backpacks | Versatile; often includes compartments for tech gear | E-commerce, travel gear retailers | Pros: Multi-functional; Cons: Can lack durability. |
Camping Backpacks | Larger capacity; built for carrying camping gear | Camping supply stores | Pros: High capacity; Cons: Bulky for daily use. |
Trekking Backpacks | Enhanced support for uneven terrain; adjustable frames | Adventure sports suppliers | Pros: Excellent load distribution; Cons: Pricey. |
Specialized Backpacks | Tailored for specific activities (e.g., climbing) | Niche outdoor shops | Pros: High performance for specific tasks; Cons: Limited use. |
Hiking Backpacks
Hiking backpacks are specifically engineered for long-distance trekking. They often feature integrated hydration systems and ample storage compartments for gear and supplies. B2B buyers should consider the comfort and support offered by these backpacks, especially for outdoor retailers catering to hiking enthusiasts. However, while they provide excellent comfort, they may also be heavier, which could deter some consumers.
Travel Backpacks
Travel backpacks are versatile and designed to accommodate a variety of travel needs. They typically include multiple compartments for easy organization of personal items and tech gear. E-commerce platforms and travel gear retailers can benefit from offering these backpacks due to their multi-functional nature. However, buyers should be aware that while these backpacks are convenient, they may not be as durable as more specialized options.
Camping Backpacks
Camping backpacks are built with larger capacities to hold extensive camping gear, making them ideal for outdoor supply stores. They often include features like reinforced bases and weather-resistant materials. B2B buyers should note that while these backpacks offer substantial space, they can be bulky and cumbersome for day-to-day use, which might limit their appeal to casual consumers.
Trekking Backpacks
Trekking backpacks provide enhanced support for navigating uneven terrains, making them suitable for adventure sports suppliers. They often feature adjustable frames and load distribution systems that improve comfort during strenuous activities. While they excel in performance, they tend to be more expensive, which could be a consideration for B2B buyers targeting budget-conscious customers.
Specialized Backpacks
Specialized backpacks cater to specific activities such as climbing, skiing, or photography. These backpacks are designed with unique features tailored to enhance performance in their respective fields. Niche outdoor shops can find value in these products, as they meet the needs of particular consumer segments. However, the limited use of these backpacks may restrict their marketability, making it essential for buyers to understand their target audience before purchasing.
Related Video: Osprey Kestrel 38 Internal Frame Backpack
Key Industrial Applications of internal frame backpack
Industry/Sector | Specific Application of Internal Frame Backpack | Value/Benefit for the Business | Key Sourcing Considerations for this Application |
---|---|---|---|
Outdoor Recreation | Hiking and trekking gear | Enhanced comfort and weight distribution for users | Durability of materials, ergonomic design, waterproofing |
Military and Defense | Tactical operations and field missions | Reliability and durability under extreme conditions | Compliance with military specifications, rugged materials |
Education | School and college backpack programs | Functionality for students, promoting active lifestyles | Safety standards, comfort features, and customization |
Travel and Tourism | Adventure travel and eco-tourism | Lightweight and functional for long-distance travel | Portability, storage capacity, and weather resistance |
Emergency Services | Search and rescue operations | Quick access to essential gear and supplies | Robust construction, specialized compartments, and visibility |
Outdoor Recreation
In the outdoor recreation sector, internal frame backpacks are essential for hiking and trekking activities. They provide optimal weight distribution, making it easier for users to carry heavy loads over long distances. Buyers should prioritize durability and waterproofing to ensure the backpack withstands various weather conditions. Ergonomic design is also crucial to enhance user comfort, reducing fatigue during extensive outdoor activities.
Military and Defense
Internal frame backpacks are vital in military and defense applications, particularly for tactical operations and field missions. These backpacks are designed to endure harsh environments while providing reliable storage for essential gear. International B2B buyers must ensure that the backpacks comply with military specifications, focusing on rugged materials that can withstand extreme conditions. Additionally, features like modular compartments for easy access to equipment can significantly enhance functionality.
Education
In the education sector, internal frame backpacks are commonly used in school and college backpack programs. They offer students a practical solution for carrying books and supplies while promoting active lifestyles. Buyers should consider safety standards, as well as comfort features like padded straps and back panels. Customization options can also be beneficial, allowing schools to create branded backpacks that foster school spirit.
Travel and Tourism
For the travel and tourism industry, internal frame backpacks are ideal for adventure travel and eco-tourism. These backpacks are designed to be lightweight yet functional, accommodating travelers who require efficient packing for long-distance journeys. Key considerations for B2B buyers include portability, storage capacity, and weather resistance, ensuring that the backpacks can handle various travel conditions and provide easy access to essentials.
Emergency Services
In emergency services, internal frame backpacks play a critical role in search and rescue operations. They facilitate quick access to essential gear and supplies, which can be lifesaving in critical situations. Buyers in this sector should prioritize robust construction to withstand tough conditions, as well as specialized compartments for organizing gear efficiently. Visibility features, such as reflective materials, can enhance safety during operations in low-light environments.
Related Video: Deuter Aircontact 65 + 10 Internal Frame Backpack
Strategic Material Selection Guide for internal frame backpack
When selecting materials for internal frame backpacks, it is essential to consider their properties, advantages, disadvantages, and overall impact on performance. This guide will analyze four common materials used in the manufacturing of internal frame backpacks, providing actionable insights for international B2B buyers.
1. Nylon
Key Properties: Nylon is a synthetic polymer known for its high tensile strength and resistance to abrasion. It typically withstands temperatures ranging from -40°C to 120°C, making it suitable for various outdoor conditions.
Pros & Cons: Nylon is lightweight, durable, and resistant to mildew and UV light, which enhances its longevity. However, it can be more expensive than other materials, and its manufacturing process may involve complex treatments to enhance water resistance.
Impact on Application: Nylon’s compatibility with waterproof coatings makes it ideal for backpacks intended for wet environments. It is commonly used in both casual and technical backpacks.
Considerations for International Buyers: Buyers should ensure that nylon materials meet international standards such as ASTM D751 for fabric strength and durability. Additionally, sourcing from suppliers who comply with environmental regulations is crucial, especially in regions like Europe where sustainability is a priority.
2. Polyester
Key Properties: Polyester is another synthetic material known for its resistance to shrinking and stretching. It can endure temperatures up to 150°C and has good moisture-wicking properties.
Pros & Cons: Polyester is generally less expensive than nylon and offers good durability and color retention. However, it is not as strong as nylon and may not perform as well in extreme conditions.
Impact on Application: Polyester is suitable for everyday backpacks and is often used in urban settings due to its aesthetic appeal and variety of colors. It is less ideal for heavy-duty outdoor applications.
Considerations for International Buyers: Buyers should look for suppliers who can provide certifications for UV resistance and colorfastness, particularly for markets in Africa and South America, where sun exposure is significant.
3. Cordura Fabric
Key Properties: Cordura is a brand of durable nylon fabric known for its resistance to abrasions, tears, and scuffs. It typically has a temperature tolerance similar to nylon.
Pros & Cons: The primary advantage of Cordura is its exceptional durability, making it suitable for heavy-duty backpacks. However, it is often more expensive and can be heavier than standard nylon or polyester fabrics.
Impact on Application: Cordura is ideal for tactical and outdoor backpacks that require high durability and resistance to wear and tear. It is favored by military and outdoor enthusiasts.
Considerations for International Buyers: Buyers should confirm that Cordura fabrics meet relevant military specifications (MIL-SPEC) and other local standards, especially in the Middle East and Africa where rugged conditions are common.
4. Ripstop Nylon
Key Properties: Ripstop nylon features a grid pattern of reinforced threads that prevent tearing and ripping. It is lightweight and can handle temperatures similar to regular nylon.
Pros & Cons: This material is highly durable while remaining lightweight, making it suitable for backpacking. However, it may not be as water-resistant unless treated, and the manufacturing process can be more complex.
Impact on Application: Ripstop nylon is particularly useful for lightweight backpacks designed for hiking and travel. Its tear-resistant nature makes it a preferred choice for outdoor enthusiasts.
Considerations for International Buyers: Buyers should ensure that ripstop nylon complies with international standards for strength and durability. Additionally, sourcing from manufacturers that prioritize eco-friendly practices can enhance brand reputation, especially in European markets.
Summary Table
Material | Typical Use Case for internal frame backpack | Key Advantage | Key Disadvantage/Limitation | Relative Cost (Low/Med/High) |
---|---|---|---|---|
Nylon | General-purpose backpacks for outdoor use | High durability and abrasion resistance | More expensive than some alternatives | Medium |
Polyester | Everyday urban backpacks | Cost-effective and color retention | Less durable than nylon | Low |
Cordura Fabric | Tactical and heavy-duty backpacks | Exceptional durability | Higher cost and weight | High |
Ripstop Nylon | Lightweight hiking and travel backpacks | Lightweight and tear-resistant | May require additional water treatment | Medium |
This strategic material selection guide provides valuable insights for B2B buyers seeking to source high-quality internal frame backpacks that meet their specific market needs. Understanding the properties and implications of each material will aid in making informed purchasing decisions that align with customer expectations and regional standards.
In-depth Look: Manufacturing Processes and Quality Assurance for internal frame backpack
The manufacturing process and quality assurance of internal frame backpacks are crucial for B2B buyers seeking reliable and durable products. Understanding these aspects can significantly impact purchasing decisions, ensuring that sourced products meet market demands and quality expectations. Below is a detailed overview of the typical manufacturing stages and quality control measures involved in producing internal frame backpacks.
Manufacturing Process of Internal Frame Backpacks
1. Material Preparation
The foundation of a high-quality internal frame backpack begins with the selection of appropriate materials. Key components include:
- Fabrics: Common choices are ripstop nylon, polyester, and Cordura, known for their durability and resistance to wear and tear.
- Frame Materials: Aluminum and composite materials are often used for the internal frame, providing strength while keeping the weight manageable.
- Foams and Padding: High-density foams are utilized for back panels and shoulder straps to enhance comfort.
Key Techniques:
– Material Testing: Before production begins, materials undergo rigorous testing for abrasion resistance, tensile strength, and weather resistance to ensure they meet specified standards.
2. Forming
Once materials are prepared, the next step is forming the components of the backpack.
- Cutting: Fabrics are cut into specific patterns using precision cutting tools or automated cutting machines to minimize waste and ensure accuracy.
- Shaping the Frame: The internal frame components are shaped and pre-assembled, ensuring they fit correctly within the backpack structure.
Key Techniques:
– Computer-Aided Design (CAD): CAD software is often used to create precise patterns and designs, allowing for accurate cutting and assembly.
3. Assembly
The assembly process involves stitching and combining all components into a finished product.
- Sewing: High-strength threads are used to sew together the fabric components. Double-stitching is commonly employed at stress points, such as strap attachments and zippers.
- Frame Integration: The internal frame is inserted into the backpack and secured, ensuring it does not shift during use.
Key Techniques:
– Bar Tacking: This reinforcement technique is applied at critical stress points to enhance durability.
4. Finishing
The final stage of production involves adding finishing touches to ensure the backpack is ready for the market.
- Quality Checks: Each backpack undergoes a thorough inspection to check for defects in stitching, alignment of zippers, and overall appearance.
- Packaging: Finished backpacks are carefully packed to prevent damage during shipping and handling.
Key Techniques:
– Visual Inspection: A final visual inspection is conducted to ensure that all components are properly aligned and functioning.
Quality Assurance Measures
Quality assurance is essential in the manufacturing of internal frame backpacks to meet international standards and fulfill buyer expectations. Here are the key aspects of quality assurance:
Relevant International Standards
- ISO 9001: This standard focuses on quality management systems and is crucial for ensuring that manufacturers consistently meet customer requirements and enhance satisfaction.
- CE Marking: For products sold in Europe, CE marking indicates compliance with health, safety, and environmental protection standards.
- API Standards: Depending on the application (e.g., outdoor or tactical), specific API standards may apply to ensure product safety and reliability.
Quality Control Checkpoints
- Incoming Quality Control (IQC): This involves inspecting raw materials and components upon arrival at the manufacturing facility to verify they meet specifications.
- In-Process Quality Control (IPQC): Throughout the manufacturing process, random inspections are conducted to ensure quality standards are maintained at every stage.
- Final Quality Control (FQC): A comprehensive evaluation of the finished product is performed before packaging and shipping.
Common Testing Methods
- Tensile Testing: Measures the strength of fabrics and straps under tension.
- Abrasion Resistance Testing: Assesses the durability of materials against wear.
- Water Resistance Testing: Ensures that materials can withstand exposure to moisture without failing.
Verification of Supplier Quality Control
B2B buyers must implement strategies to verify the quality control processes of potential suppliers effectively. Here are actionable steps:
- Supplier Audits: Conduct regular audits of suppliers to assess their manufacturing practices and quality control measures. Look for certifications such as ISO 9001.
- Request Quality Reports: Ask suppliers for documentation of their quality control processes, including test results and inspection records.
- Third-Party Inspections: Engage independent quality assurance firms to conduct inspections of the manufacturing facility and products, providing an unbiased assessment of quality standards.
Quality Control and Certification Nuances for International Buyers
For buyers in regions such as Africa, South America, the Middle East, and Europe, understanding regional regulations and certification requirements is crucial:
- Local Compliance: Ensure that products comply with local regulations in target markets, which may differ from international standards.
- Cultural Considerations: Recognize that consumer preferences can vary significantly across regions, which may affect the quality standards expected by end-users.
- Logistical Challenges: Be aware of potential supply chain disruptions that can impact quality, particularly when sourcing from distant manufacturers.
By understanding the manufacturing processes and quality assurance measures for internal frame backpacks, B2B buyers can make informed decisions, ensuring they partner with reliable suppliers who deliver high-quality products. This knowledge not only minimizes risks associated with poor-quality goods but also enhances brand reputation in competitive markets.
Related Video: How a Backpack is Made : Every Step on the Production Line
Comprehensive Cost and Pricing Analysis for internal frame backpack Sourcing
When sourcing internal frame backpacks, understanding the comprehensive cost structure and pricing analysis is essential for B2B buyers. The costs can be broken down into several key components, each contributing to the final price.
Cost Components
-
Materials: The choice of materials significantly impacts the overall cost. High-quality fabrics, such as ripstop nylon or Cordura, typically command higher prices due to their durability and performance characteristics. Additionally, the cost of zippers, buckles, and other hardware should be factored in, as premium components can enhance product longevity.
-
Labor: Labor costs vary by region and can influence total expenses. For instance, manufacturing in countries with lower labor costs may seem attractive but can lead to quality issues if not managed properly. It’s crucial to evaluate the skill level of workers and the labor practices of potential suppliers.
-
Manufacturing Overhead: This includes factory utilities, equipment maintenance, and other operational costs. Overhead can vary widely based on the efficiency of the manufacturing facility and the technology used. A more efficient factory might offer better pricing due to lower overhead per unit.
-
Tooling: Initial tooling costs for creating custom designs or specific features can be substantial. Buyers should consider these upfront costs when negotiating prices, as they can significantly influence the overall pricing structure.
-
Quality Control (QC): Investing in robust QC processes helps mitigate risks associated with product defects, which can be costly in terms of returns and brand reputation. High-quality control measures might lead to higher initial costs but can save money in the long run by reducing returns and customer dissatisfaction.
-
Logistics: Shipping costs should be carefully evaluated, especially for international transactions. Factors such as Incoterms, distance, and transportation method can add significantly to the cost. Understanding the total logistics cost is crucial for accurate pricing.
-
Margin: Suppliers will typically add a profit margin to cover their costs and generate a profit. This margin can vary based on market demand, competition, and the perceived value of the product.
Price Influencers
-
Volume/MOQ: Minimum order quantities (MOQ) often dictate pricing. Higher volumes generally lead to lower per-unit costs due to economies of scale. Buyers should negotiate for favorable terms based on their purchasing forecasts.
-
Specifications/Customization: Custom features or specifications can increase costs significantly. Buyers should weigh the benefits of customization against the added expenses.
-
Materials and Quality Certifications: High-quality materials and certifications (e.g., ISO, CE) can enhance product value but also increase costs. Buyers should assess whether the additional expense aligns with their brand positioning and customer expectations.
-
Supplier Factors: The reliability, reputation, and location of suppliers can influence pricing. Established suppliers with a track record of quality may charge more, but they often provide better service and reliability.
-
Incoterms: Understanding Incoterms is vital for managing risks and costs associated with international shipping. These terms define responsibilities for shipping, insurance, and tariffs, directly affecting the total cost of ownership.
Buyer Tips
-
Negotiation: Engage in thorough negotiations with suppliers to secure the best possible prices. Building a relationship based on transparency can lead to better terms.
-
Cost-Efficiency: Consider the Total Cost of Ownership (TCO), which includes all costs associated with the product over its lifecycle, not just the purchase price. This approach helps in evaluating the long-term value of sourcing decisions.
-
Pricing Nuances for International Buyers: Be aware of regional pricing differences, tariffs, and import duties that may affect overall costs. Local market conditions in Africa, South America, the Middle East, and Europe can lead to variations in pricing strategies.
Disclaimer
Prices in the backpack industry can fluctuate based on market conditions, supplier negotiations, and raw material availability. Buyers are advised to conduct thorough market research and supplier assessments to obtain the most accurate pricing information.
Spotlight on Potential internal frame backpack Manufacturers and Suppliers
This section offers a look at a few manufacturers active in the ‘internal frame backpack’ market. This is a representative sample for illustrative purposes; B2B buyers must conduct their own extensive due diligence before any engagement. Information is synthesized from public sources and general industry knowledge.
Essential Technical Properties and Trade Terminology for internal frame backpack
When sourcing internal frame backpacks, understanding the technical properties and common trade terminology is essential for making informed purchasing decisions. This section outlines critical specifications and industry terms that will aid B2B buyers, particularly those from Africa, South America, the Middle East, and Europe.
Key Technical Properties
-
Material Grade
– Definition: Refers to the quality and type of fabric used in the construction of the backpack, such as nylon or polyester.
– B2B Importance: High-grade materials enhance durability, water resistance, and overall performance, which are critical for customer satisfaction and brand reputation. -
Weight Capacity
– Definition: The maximum load the backpack can safely carry, often indicated in kilograms or pounds.
– B2B Importance: Understanding weight capacity helps buyers select backpacks suited for specific activities, such as hiking or travel, ensuring they meet user requirements. -
Frame Construction
– Definition: The design and material of the internal frame, which provides structure and support.
– B2B Importance: Different frame materials (e.g., aluminum, plastic) affect weight, comfort, and load distribution. Knowing the frame type can influence the product’s appeal to target markets. -
Tolerances
– Definition: The allowable variation in measurements and specifications during manufacturing, such as strap length or compartment size.
– B2B Importance: Tight tolerances ensure consistency in product quality, reducing the likelihood of defects and enhancing the backpack’s usability.
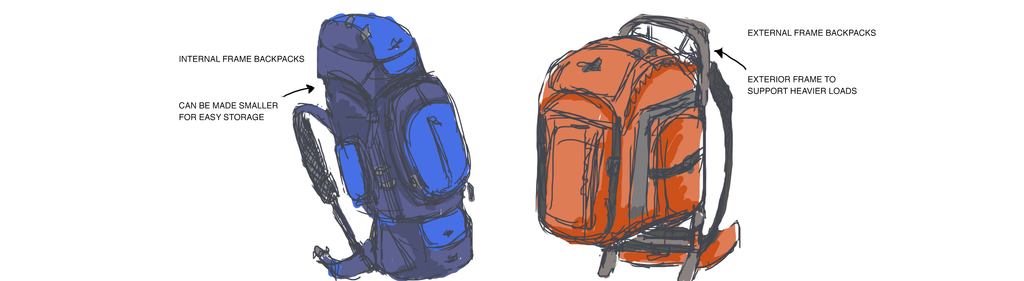
Illustrative Image (Source: Google Search)
-
Padding Thickness
– Definition: The amount of cushioning in areas like shoulder straps and back panels.
– B2B Importance: Adequate padding improves comfort during use, making the product more attractive to end-users, especially for long treks or travel. -
Water Resistance Rating
– Definition: A measurement of how well the material can withstand water exposure, often indicated by a hydrostatic head test.
– B2B Importance: Buyers need to ensure the backpacks can perform in various weather conditions, which is crucial for outdoor and travel markets.
Common Trade Terminology
-
OEM (Original Equipment Manufacturer)
– Definition: A company that produces parts or equipment that may be marketed by another manufacturer.
– Usage: Essential for buyers looking to customize designs or brands, as they often work with OEMs for tailored products. -
MOQ (Minimum Order Quantity)
– Definition: The smallest quantity of a product that a supplier is willing to sell.
– Usage: Understanding MOQ is vital for budgeting and inventory planning, especially for smaller businesses or startups. -
RFQ (Request for Quotation)
– Definition: A document that solicits quotes from suppliers for specific goods or services.
– Usage: RFQs help buyers compare prices and terms from multiple suppliers, facilitating better negotiation outcomes. -
Incoterms (International Commercial Terms)
– Definition: A series of predefined commercial terms published by the International Chamber of Commerce (ICC) that clarify the responsibilities of buyers and sellers.
– Usage: Familiarity with Incoterms ensures clarity on shipping, insurance, and delivery responsibilities, reducing disputes during international trade. -
Lead Time
– Definition: The amount of time between placing an order and receiving it.
– Usage: Buyers need to account for lead time in their supply chain management to meet market demands and avoid stockouts. -
Sample Approval
– Definition: The process of reviewing and approving a prototype or sample of the product before bulk production begins.
– Usage: Ensures that the final product meets quality and design expectations, minimizing risks associated with large orders.
Incorporating these technical properties and trade terms into your sourcing strategy will enhance your ability to make informed decisions when purchasing internal frame backpacks, ultimately leading to better product offerings and customer satisfaction.
Navigating Market Dynamics, Sourcing Trends, and Sustainability in the internal frame backpack Sector
The internal frame backpack market is experiencing robust growth driven by several global trends. The rise in outdoor recreational activities, coupled with an increasing emphasis on travel and adventure tourism, significantly fuels demand. In regions such as Africa and South America, where trekking and exploration are becoming more mainstream, the internal frame backpack serves as a vital accessory. Additionally, the popularity of eco-tourism is prompting buyers to seek sustainable options, leading to a shift in sourcing preferences.
Emerging B2B technologies, such as blockchain for supply chain transparency and AI for demand forecasting, are transforming sourcing practices. Buyers are increasingly leveraging these technologies to ensure product authenticity and streamline procurement processes. As a result, international buyers are focusing on suppliers who can demonstrate not just quality but also operational efficiency and technological adoption.
Key market dynamics include the growing competition among manufacturers, which encourages innovation in design and functionality. Furthermore, the rise of direct-to-consumer sales models is changing traditional distribution channels, making it imperative for B2B buyers to adapt their strategies. Understanding these dynamics allows international buyers to make informed sourcing decisions that align with both market demands and consumer preferences.
Sustainability & Ethical Sourcing in B2B
The environmental impact of backpack production is a pressing concern for today’s B2B buyers. The sourcing of materials such as nylon and polyester, commonly used in internal frame backpacks, poses significant ecological challenges, including plastic pollution and high carbon emissions. Consequently, buyers must prioritize ethical sourcing practices that minimize environmental harm.
A focus on sustainability can be achieved by selecting suppliers who utilize recycled materials and environmentally friendly production processes. Certifications such as Global Recycled Standard (GRS) and OEKO-TEX® can serve as indicators of a supplier’s commitment to sustainability. Moreover, ensuring that suppliers adhere to ethical labor practices is crucial, as consumers increasingly favor brands that demonstrate social responsibility. By emphasizing sustainability in sourcing, international buyers can enhance their brand reputation and meet the growing consumer demand for eco-conscious products.
Brief Evolution/History
The evolution of the internal frame backpack can be traced back to the mid-20th century when outdoor enthusiasts began to seek more efficient designs for carrying gear. Early models utilized external frames, but the introduction of internal frames provided greater stability and comfort, revolutionizing backpack design. As the outdoor market expanded in the 1980s and 1990s, manufacturers began to innovate with lighter materials and ergonomic designs, making internal frame backpacks the preferred choice for serious hikers and travelers. Today, this segment continues to evolve, with advancements in technology and materials driving new designs that cater to diverse consumer needs. Understanding this historical context can help B2B buyers appreciate the craftsmanship and innovation behind modern internal frame backpacks, enhancing their sourcing strategies.
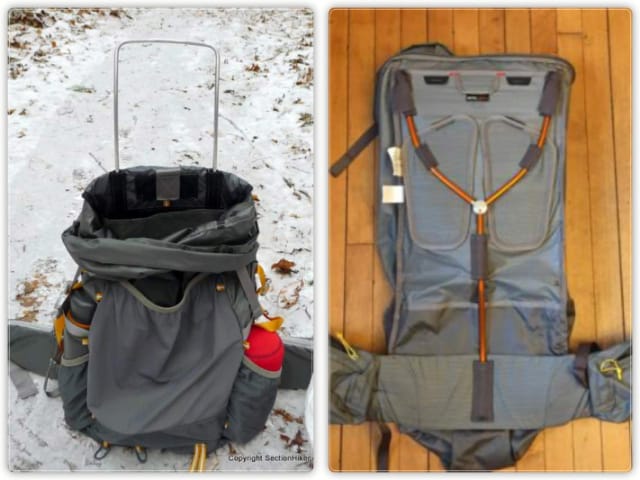
Illustrative Image (Source: Google Search)
Frequently Asked Questions (FAQs) for B2B Buyers of internal frame backpack
-
What criteria should I use to vet suppliers for internal frame backpacks?
When vetting suppliers, focus on their manufacturing capabilities, experience in producing internal frame backpacks, and adherence to quality standards. Request references from previous clients and check for certifications such as ISO 9001 for quality management. Conduct factory visits, if possible, to assess working conditions and production processes. Additionally, inquire about their material sourcing practices to ensure they use high-quality, durable fabrics suitable for your market needs. -
Can I customize the design of internal frame backpacks?
Yes, many manufacturers offer customization options. Discuss your specific requirements, such as size, color, branding, and features (like pockets or hydration systems), during the initial negotiations. Provide detailed design specifications and, if possible, prototypes or sketches. Be aware that extensive customization may affect lead times and costs, so clarify these aspects upfront with your supplier. -
What are typical minimum order quantities (MOQ) and lead times for internal frame backpacks?
MOQs can vary significantly by supplier and may range from 100 to 1,000 units, depending on the complexity of the design and materials used. Lead times typically range from 4 to 12 weeks after order confirmation, influenced by factors like production capacity and material availability. It’s prudent to discuss these details early in the negotiation process to align with your inventory planning and market demands.
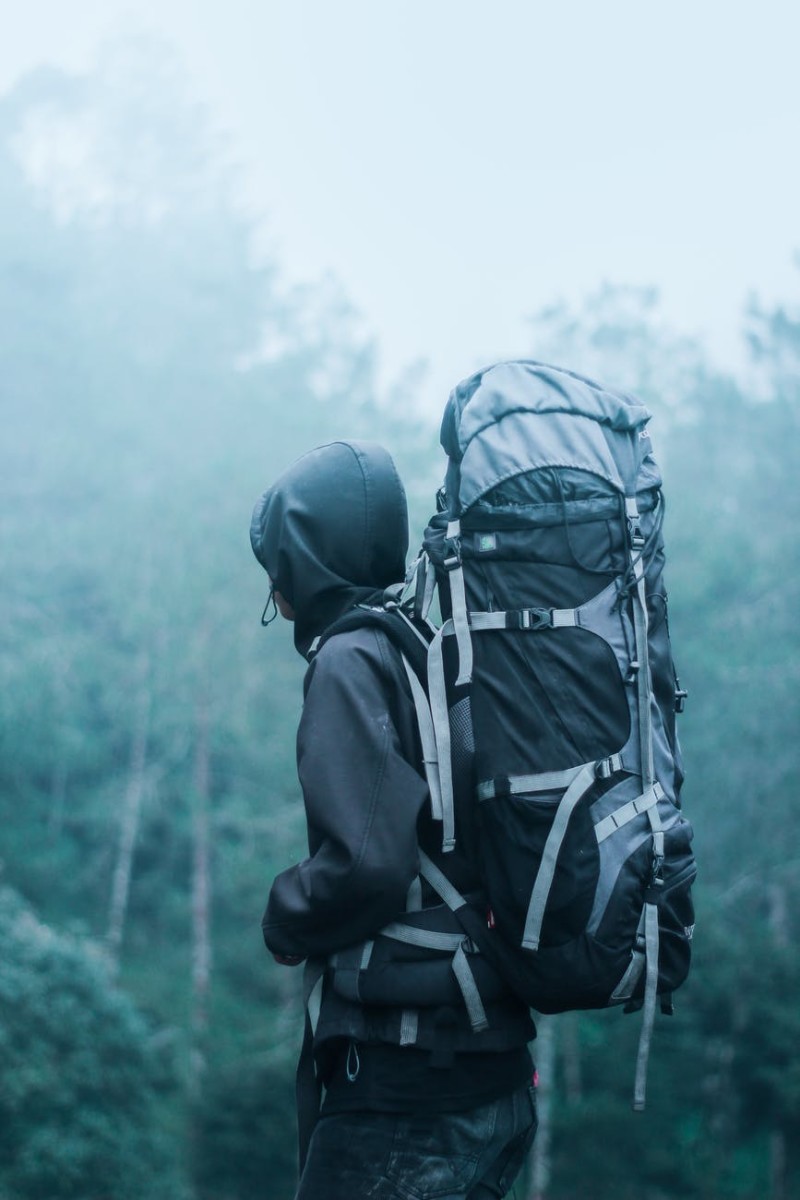
Illustrative Image (Source: Google Search)
-
What quality assurance practices should I expect from suppliers?
A reputable supplier should implement rigorous quality assurance (QA) protocols, including material inspections, in-process checks, and final product evaluations. Request documentation of their QA process and any relevant certifications, such as SGS testing or compliance with international safety standards. Additionally, consider requesting production samples before full-scale manufacturing to verify quality and functionality. -
How should I handle payment terms with suppliers?
Establish clear payment terms early in the negotiation process. Common practices include a deposit (often 30-50%) upon order confirmation, with the balance due before shipment. Consider using secure payment methods like letters of credit or escrow services to mitigate risks. Ensure that payment terms are documented in the contract to avoid disputes later on. -
What logistics considerations should I keep in mind when sourcing from international suppliers?
When sourcing from international suppliers, consider shipping costs, customs duties, and delivery times. Engage with logistics companies experienced in handling international shipments to ensure efficient transport. Discuss with your supplier whether they can manage logistics on their end or if you need to arrange it yourself. Additionally, familiarize yourself with the regulations and requirements for importing goods into your country to avoid delays. -
How can I resolve disputes with suppliers effectively?
Establish clear communication channels and documentation practices to minimize disputes. If issues arise, address them promptly through direct discussions with the supplier. If resolution is not achieved, consider mediation or arbitration as alternatives to litigation, as they are often less costly and time-consuming. Always have a well-drafted contract that outlines dispute resolution processes, including jurisdiction and governing law. -
What certifications or compliance should I look for in internal frame backpacks?
Look for certifications that ensure product safety and quality, such as ISO standards, REACH compliance (for chemical safety in the EU), and EN standards (for ergonomic design). Additionally, inquire about any sustainability certifications, especially if your target market values eco-friendly products. These certifications can enhance your brand’s reputation and appeal to consumers increasingly concerned about sustainability and ethical sourcing.
Strategic Sourcing Conclusion and Outlook for internal frame backpack
In conclusion, strategic sourcing of internal frame backpacks is vital for ensuring product quality and brand reputation in the competitive B2B landscape. By understanding common quality issues—such as material defects, stitching problems, and ergonomic design flaws—buyers can mitigate risks and enhance customer satisfaction. Engaging with reputable suppliers who prioritize rigorous testing and quality control processes is essential for securing durable and functional products that meet market demands.
International B2B buyers from Africa, South America, the Middle East, and Europe should focus on building strong relationships with suppliers who demonstrate transparency and commitment to quality. Conducting thorough due diligence, including requesting samples and production audits, will empower buyers to make informed decisions that align with their business objectives.
As the market for outdoor and travel gear continues to evolve, staying ahead of trends and consumer preferences will be crucial. By investing in strategic sourcing practices today, businesses can not only enhance their product offerings but also position themselves for future growth. Take action now to secure partnerships that will drive success in the dynamic world of internal frame backpacks.