Your Ultimate Guide to Sourcing Mini Stitch Backpack
Guide to Mini Stitch Backpack
- Introduction: Navigating the Global Market for mini stitch backpack
- Understanding mini stitch backpack Types and Variations
- Key Industrial Applications of mini stitch backpack
- Strategic Material Selection Guide for mini stitch backpack
- In-depth Look: Manufacturing Processes and Quality Assurance for mini stitch backpack
- Comprehensive Cost and Pricing Analysis for mini stitch backpack Sourcing
- Spotlight on Potential mini stitch backpack Manufacturers and Suppliers
- Essential Technical Properties and Trade Terminology for mini stitch backpack
- Navigating Market Dynamics, Sourcing Trends, and Sustainability in the mini stitch backpack Sector
- Frequently Asked Questions (FAQs) for B2B Buyers of mini stitch backpack
- Strategic Sourcing Conclusion and Outlook for mini stitch backpack
Introduction: Navigating the Global Market for mini stitch backpack
The mini stitch backpack has emerged as a vital product in the global market, appealing to a diverse range of consumers from urban professionals to outdoor enthusiasts. Its compact size, stylish design, and functionality make it an ideal choice for both personal use and corporate branding. For international B2B buyers, particularly those from Africa, South America, the Middle East, and Europe, understanding the intricacies of this product is essential for making informed sourcing decisions.
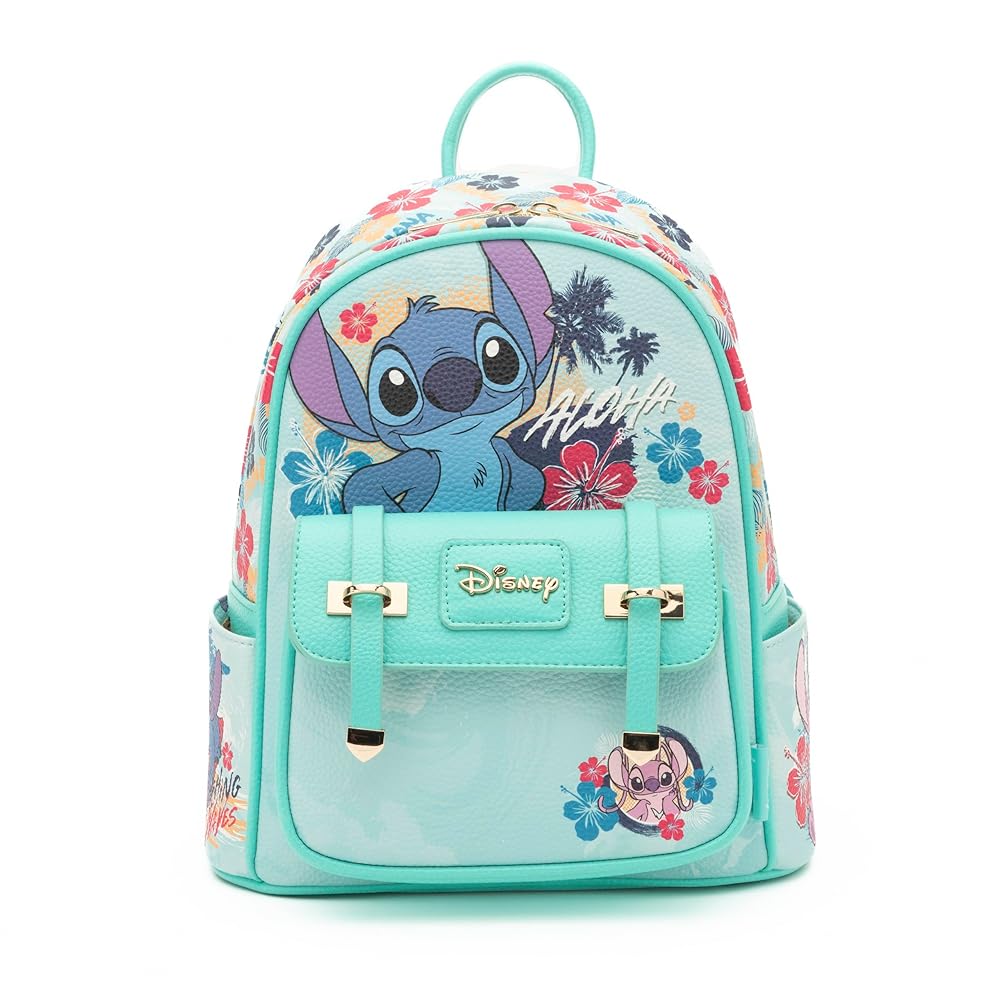
Illustrative Image (Source: Google Search)
This comprehensive guide will explore various aspects of the mini stitch backpack, including its different types and materials, manufacturing processes, quality control standards, and sourcing strategies. Buyers will gain insights into the best practices for selecting reliable suppliers, negotiating costs, and understanding market trends.
In addition, this guide addresses common questions and concerns that arise when sourcing mini stitch backpacks, empowering businesses to navigate the complexities of the global market with confidence. By leveraging the information presented here, B2B buyers can enhance their procurement strategies, ensuring that they not only meet consumer demands but also achieve competitive pricing and superior product quality.
With a focus on actionable insights, this guide serves as a crucial resource for international buyers aiming to capitalize on the growing demand for mini stitch backpacks in their respective regions.
Understanding mini stitch backpack Types and Variations
Type Name | Key Distinguishing Features | Primary B2B Applications | Brief Pros & Cons for Buyers |
---|---|---|---|
Standard Mini Stitch | Compact design, single main compartment, lightweight | Retail, casual use | Pros: Easy to manufacture; Cons: Limited storage space. |
Waterproof Mini Stitch | Made with waterproof materials, sealed zippers | Outdoor activities, travel | Pros: Durable in wet conditions; Cons: Higher cost. |
Eco-friendly Mini Stitch | Crafted from recycled materials, sustainable practices | Eco-conscious brands, promotional use | Pros: Appeals to green consumers; Cons: May have higher MOQ. |
Fashion Mini Stitch | Trendy designs, often with embellishments or unique patterns | Fashion retail, brand collaborations | Pros: Attracts fashion-forward consumers; Cons: Higher design complexity. |
Functional Mini Stitch | Multiple pockets, ergonomic design for utility | Corporate giveaways, practical use | Pros: Versatile for various uses; Cons: Can be pricier due to features. |
Standard Mini Stitch
The Standard Mini Stitch backpack is characterized by its compact design and lightweight structure, making it an ideal choice for casual use and retail applications. This type typically features a single main compartment, which limits its storage capacity but simplifies manufacturing. For B2B buyers, this model is advantageous due to its cost-effectiveness and ease of production, although it may not satisfy those needing more storage or organizational features.
Waterproof Mini Stitch
Designed for outdoor activities, the Waterproof Mini Stitch backpack is made from specialized waterproof materials and includes sealed zippers to prevent water ingress. This type is particularly suited for travel and outdoor events, appealing to businesses targeting adventure-seeking consumers. While the durability in wet conditions is a significant advantage, buyers must consider the higher production costs associated with these materials.
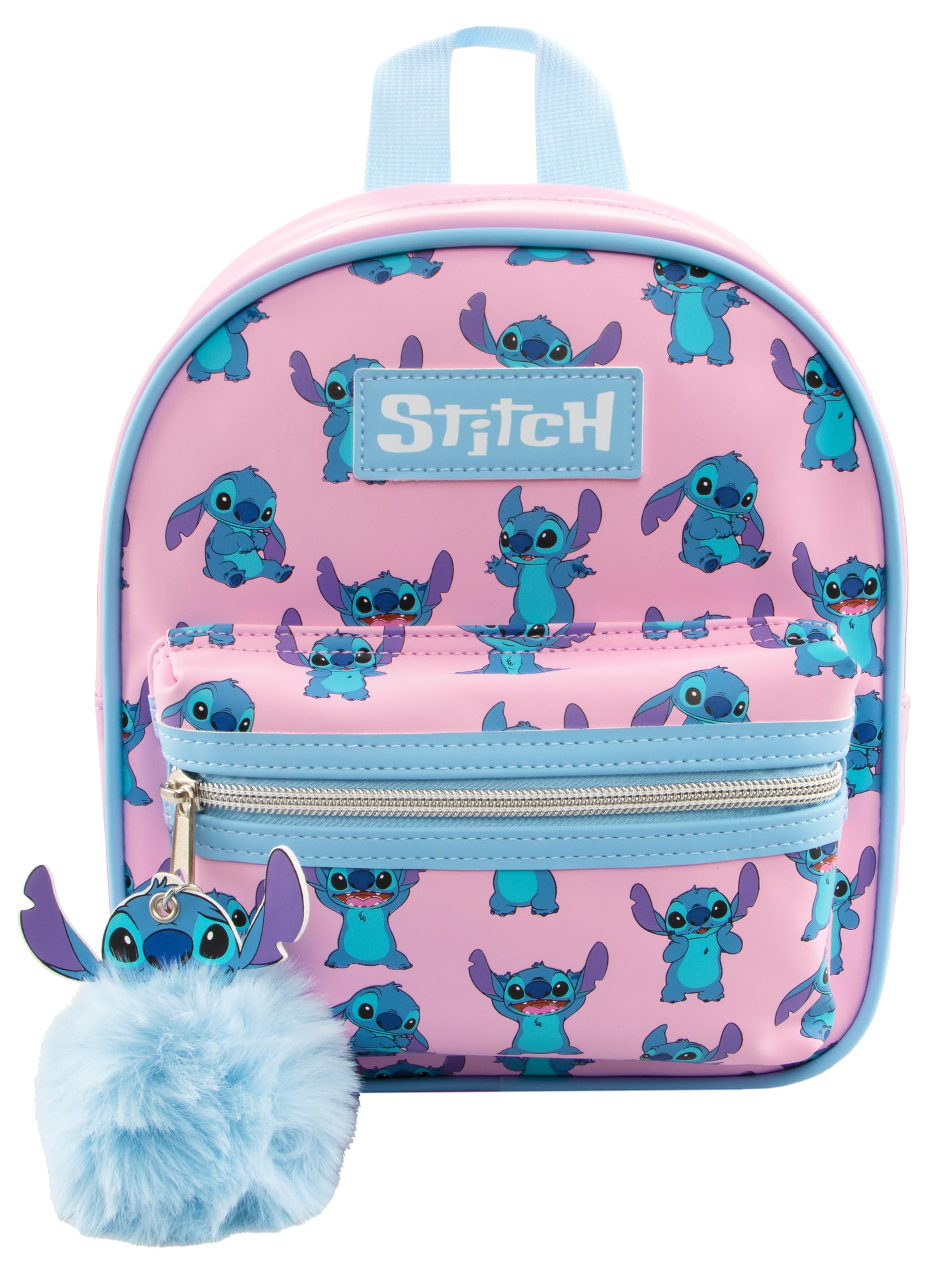
Illustrative Image (Source: Google Search)
Eco-friendly Mini Stitch
The Eco-friendly Mini Stitch backpack is crafted from recycled materials and employs sustainable manufacturing practices. This type caters to eco-conscious brands and companies looking to promote their sustainability efforts. While appealing to a growing market segment, buyers should be aware of the potential for higher minimum order quantities (MOQs) and costs associated with eco-friendly materials.
Fashion Mini Stitch
Targeting the fashion market, the Fashion Mini Stitch backpack features trendy designs, often embellished with unique patterns or accessories. This type is ideal for fashion retail and brand collaborations, aiming to attract style-conscious consumers. However, the increased complexity in design may lead to higher production costs, which buyers need to factor into their pricing strategies.
Functional Mini Stitch
The Functional Mini Stitch backpack is designed with multiple pockets and an ergonomic structure to enhance utility. This type is suitable for corporate giveaways and practical applications, appealing to businesses that prioritize functionality. While its versatility is a key selling point, buyers should anticipate potentially higher prices due to the additional features and design considerations.
Related Video: A Practical Introduction to Large Language Models (LLMs)
Key Industrial Applications of mini stitch backpack
Industry/Sector | Specific Application of mini stitch backpack | Value/Benefit for the Business | Key Sourcing Considerations for this Application |
---|---|---|---|
Education | Student and teacher use for carrying books and supplies | Enhances mobility and organization for educational materials | Durability of materials, comfort of straps, capacity for books |
Outdoor Recreation | Hiking and camping gear for carrying essentials | Lightweight design facilitates long-distance travel | Weather resistance, material breathability, ergonomic design |
Corporate Events | Promotional giveaways for branding and marketing | Increases brand visibility and customer engagement | Customization options, quality of printing, delivery timelines |
Retail | Retail display for merchandise and accessories | Attracts customers and enhances shopping experience | Aesthetic appeal, material quality, pricing for bulk orders |
Logistics & Transport | Delivery and transport of goods in urban settings | Efficient handling and organization of products | Load capacity, reinforcement for heavy items, cost-effective sourcing |
Education
In the education sector, mini stitch backpacks are increasingly used by students and teachers for transporting books, stationery, and other educational materials. These backpacks provide a practical solution to the challenges of mobility and organization in a school environment. For international buyers, especially from regions like Africa and South America, it’s essential to consider durability, as these bags must withstand daily use. Additionally, comfort in carrying and adequate capacity for textbooks are critical factors that can influence purchasing decisions.
Outdoor Recreation
For outdoor enthusiasts, mini stitch backpacks serve as a reliable companion for hiking, camping, and other recreational activities. Their lightweight design makes them ideal for carrying essentials, such as water bottles, snacks, and first-aid kits, without adding unnecessary weight. B2B buyers in the Middle East and Europe should prioritize weather-resistant materials to ensure that the backpacks can endure various environmental conditions. Ergonomic designs that promote comfort during long treks are also important considerations for enhancing user experience.
Corporate Events
In the corporate sector, mini stitch backpacks are often utilized as promotional giveaways at events, conferences, and trade shows. They serve as an effective marketing tool by increasing brand visibility while providing attendees with a practical item they can use. For businesses in Europe and South America, it’s vital to explore customization options that allow for branding, including logo printing and color choices. Ensuring quality in printing and timely delivery is essential for maintaining a professional image.
Retail
Retailers frequently use mini stitch backpacks for displaying merchandise and accessories, enhancing the overall shopping experience. These backpacks can be positioned as stylish and functional items, attracting customers’ attention. For B2B buyers, particularly in Africa and the Middle East, aesthetic appeal and material quality are crucial when selecting backpacks for retail purposes. Pricing for bulk orders should also be considered to maximize profitability while ensuring that the product remains appealing to consumers.
Logistics & Transport
In the logistics and transport industry, mini stitch backpacks can be employed for the efficient delivery of goods, especially in urban settings. Their design allows for organized carrying of products, which can streamline operations and improve handling. International buyers from regions like Europe and South America should focus on load capacity and the reinforcement of materials to accommodate heavier items. Cost-effective sourcing will also play a significant role in optimizing supply chain efficiency.
Related Video: 10 Nifty Uses for Oscillating Multitool Saws
Strategic Material Selection Guide for mini stitch backpack
When selecting materials for a mini stitch backpack, international B2B buyers must consider various factors that influence product performance, durability, and marketability. Below is an analysis of four common materials used in the manufacturing of mini stitch backpacks, focusing on their properties, advantages, disadvantages, and specific considerations for buyers from regions such as Africa, South America, the Middle East, and Europe.
1. Nylon (e.g., Ripstop Nylon)
Key Properties:
Nylon is known for its high tensile strength, lightweight nature, and resistance to abrasion. Ripstop nylon, in particular, features a grid pattern that enhances its durability and tear resistance.
Pros & Cons:
– Pros: Durable and lightweight, water-resistant, and relatively low-cost compared to other synthetic fabrics. It is also easy to clean and maintain.
– Cons: Can be susceptible to UV degradation over time, which may reduce its lifespan if exposed to direct sunlight frequently.
Impact on Application:
Nylon is suitable for various backpack designs, offering flexibility in terms of color and texture. Its lightweight nature makes it ideal for mini backpacks that require portability.
Considerations for International Buyers:
Buyers should ensure compliance with local regulations regarding the use of synthetic materials. Common standards like ASTM D751 for fabric strength may apply. Additionally, sourcing high-quality nylon from reputable suppliers can mitigate risks associated with inferior products.
2. Polyester
Key Properties:
Polyester is a synthetic fabric known for its excellent resistance to shrinking, stretching, and wrinkling. It also has good moisture-wicking properties, making it suitable for active use.
Pros & Cons:
– Pros: Durable, resistant to mildew and fading, and generally more affordable than nylon. It also dries quickly, which is beneficial for backpacks used in various weather conditions.
– Cons: Less breathable than natural fibers, which may affect comfort during extended use.
Impact on Application:
Polyester is often used in budget-friendly backpacks and is compatible with various printing techniques for branding purposes.
Considerations for International Buyers:
Buyers should be aware of the environmental impact of polyester production and consider sourcing recycled polyester options. Compliance with standards such as Oeko-Tex can enhance product appeal in eco-conscious markets.
3. Canvas
Key Properties:
Canvas is a durable fabric made from cotton or a blend of cotton and synthetic fibers. It is known for its sturdiness and ability to withstand wear and tear.
Pros & Cons:
– Pros: Highly durable, offers a classic aesthetic, and is often more environmentally friendly than synthetic options. It can also be treated for water resistance.
– Cons: Heavier than synthetic materials and may require more care in terms of cleaning and maintenance.
Impact on Application:
Canvas is suitable for casual and lifestyle backpacks, appealing to consumers who prefer a more natural look and feel.
Considerations for International Buyers:
Buyers should consider the source of the cotton used in canvas production to ensure ethical practices. Compliance with standards like GOTS (Global Organic Textile Standard) can enhance marketability in regions with strict sustainability regulations.
4. Leather (e.g., Genuine Leather, PU Leather)
Key Properties:
Leather is a natural material known for its luxurious appearance and durability. Genuine leather offers excellent strength and a unique aesthetic, while PU leather provides a cost-effective alternative.
Pros & Cons:
– Pros: High durability, aesthetic appeal, and can develop a unique patina over time. PU leather is easier to clean and maintain.
– Cons: Genuine leather can be expensive and may require special care. PU leather, while cheaper, may not offer the same longevity.
Impact on Application:
Leather is often used in premium mini stitch backpacks, targeting a market segment that values quality and craftsmanship.
Considerations for International Buyers:
Buyers must be aware of the regulations surrounding animal products in their markets. Compliance with standards such as REACH (Registration, Evaluation, Authorisation, and Restriction of Chemicals) is crucial for leather products.
Summary Table
Material | Typical Use Case for mini stitch backpack | Key Advantage | Key Disadvantage/Limitation | Relative Cost (Low/Med/High) |
---|---|---|---|---|
Nylon (e.g., Ripstop Nylon) | Lightweight, durable backpacks for daily use | Durable, water-resistant | Susceptible to UV degradation | Medium |
Polyester | Budget-friendly backpacks for casual use | Affordable, quick-drying | Less breathable | Low |
Canvas | Casual and lifestyle backpacks | Highly durable, eco-friendly | Heavier, requires care | Medium |
Leather (Genuine/PU) | Premium mini stitch backpacks | Luxurious aesthetic, durable | Expensive (genuine), less longevity (PU) | High |
This guide provides a comprehensive overview of material options for mini stitch backpacks, helping international B2B buyers make informed decisions that align with their market needs and compliance requirements.
In-depth Look: Manufacturing Processes and Quality Assurance for mini stitch backpack
Manufacturing Processes for Mini Stitch Backpacks
The manufacturing of mini stitch backpacks involves several key stages, each crucial for ensuring the final product meets quality standards and consumer expectations. Below are the primary stages of production, along with the techniques employed at each phase.
1. Material Preparation
The first step in manufacturing mini stitch backpacks is material selection. Common materials include:
- Fabrics: High-denier nylon, polyester, and canvas are popular for their durability and lightweight properties.
- Lining: Waterproof or moisture-wicking materials may be used to enhance comfort and usability.
- Trims and Accessories: Zippers, buckles, and straps must be selected based on strength and functionality.
Once selected, materials undergo preparation, which may include cutting to size, treating for water resistance, or pre-shrinking to prevent future dimensional changes.
2. Forming
The forming stage involves shaping the materials into the components of the backpack. This typically includes:
- Cutting: Using automated cutting machines for precision to ensure each component is uniform.
- Sewing: Employing industrial sewing machines equipped with specialized feet for stitching thick materials. Techniques such as double-stitched seams are used for added durability.
- Reinforcement: Areas subject to stress, like straps and zippers, are reinforced through bar-tacking or additional stitching.
3. Assembly
In the assembly phase, individual components are brought together to form the complete backpack. This process includes:
- Joining Components: Utilizing various stitching techniques (e.g., zigzag, straight stitch) to attach pieces securely.
- Inserting Linings and Padding: Adding comfort features such as foam padding in straps or back panels for ergonomics.
- Quality Checks: Conducting inline inspections to ensure that stitching is consistent and components are securely attached.
4. Finishing
The final stage of manufacturing focuses on the aesthetic and functional aspects of the backpack. Key activities include:
- Trimming: Removing excess threads and checking for any defects in the fabric.
- Branding: Adding labels, tags, or printing logos as per customer specifications.
- Final Inspection: Conducting a comprehensive review of the finished product to ensure it meets design specifications and quality standards.
Quality Assurance in Mini Stitch Backpack Manufacturing
Quality assurance (QA) is vital in ensuring that mini stitch backpacks not only meet production standards but also fulfill international quality requirements. Here are the essential components of QA in this industry.
International Standards
B2B buyers should be familiar with the following international quality standards:
- ISO 9001: A widely recognized standard for quality management systems that ensures consistent product quality and customer satisfaction.
- CE Marking: A certification indicating that products meet EU safety, health, and environmental protection standards.
- API Standards: Relevant for backpacks intended for specific industries, such as those used in outdoor activities or military applications.
QC Checkpoints
Quality Control (QC) typically involves multiple checkpoints throughout the manufacturing process:
- Incoming Quality Control (IQC): Ensures that raw materials meet specified standards before production begins.
- In-Process Quality Control (IPQC): Ongoing checks during manufacturing to catch defects early. This includes monitoring sewing accuracy and material integrity.
- Final Quality Control (FQC): A comprehensive review of the finished products to ensure they meet all specifications before shipment.
Common Testing Methods
B2B buyers should inquire about the testing methods employed to ensure product quality:
- Tensile Strength Testing: Measures the strength of seams and straps.
- Waterproof Testing: Assesses the effectiveness of waterproof materials and treatments.
- Color Fastness Testing: Ensures that colors do not fade or bleed during washing or exposure to sunlight.
Verifying Supplier Quality Control
For international B2B buyers, particularly from Africa, South America, the Middle East, and Europe, verifying a supplier’s quality control processes is essential. Here are several strategies:
-
Audits: Conducting factory audits to assess the manufacturer’s capabilities, quality control processes, and compliance with international standards.
-
Quality Reports: Requesting documentation that outlines the results of quality checks and any corrective actions taken.
-
Third-Party Inspections: Engaging third-party inspection services to conduct independent assessments of production quality before shipment.
-
Certifications: Verifying that suppliers hold relevant certifications (ISO, CE, etc.) that demonstrate their commitment to quality.
QC and Certification Nuances for International Buyers
Understanding the nuances of quality control and certification is crucial for B2B buyers engaging with manufacturers in different regions, particularly in emerging markets like Vietnam and Thailand:
-
Cultural Differences: Be aware that approaches to quality may vary by region. Establishing clear communication about quality expectations is essential.
-
Regulatory Compliance: Different regions may have specific regulations affecting product quality. Ensure that your supplier is compliant with the regulations of the markets you intend to sell in.
-
Lead Times: International buyers should consider that the time taken for quality checks and certifications can affect lead times. Plan accordingly to avoid delays.
By comprehensively understanding the manufacturing processes and quality assurance protocols, B2B buyers can make informed decisions and foster successful partnerships with manufacturers of mini stitch backpacks. This proactive approach will not only enhance product quality but also improve overall business success in the competitive backpack market.
Related Video: How a Backpack is Made : Every Step on the Production Line
Comprehensive Cost and Pricing Analysis for mini stitch backpack Sourcing
When sourcing mini stitch backpacks, understanding the comprehensive cost structure and pricing dynamics is essential for international B2B buyers. This analysis will break down the key cost components, identify pricing influencers, and provide actionable tips to enhance your sourcing strategy.
Cost Components
- Materials: The choice of materials significantly impacts the overall cost. Common materials for mini stitch backpacks include:
– Fabric: Options like ripstop nylon, polyester, or canvas vary in price based on durability and weather resistance.
– Hardware: Zippers, buckles, and straps can range in cost, especially if opting for high-quality or branded components.
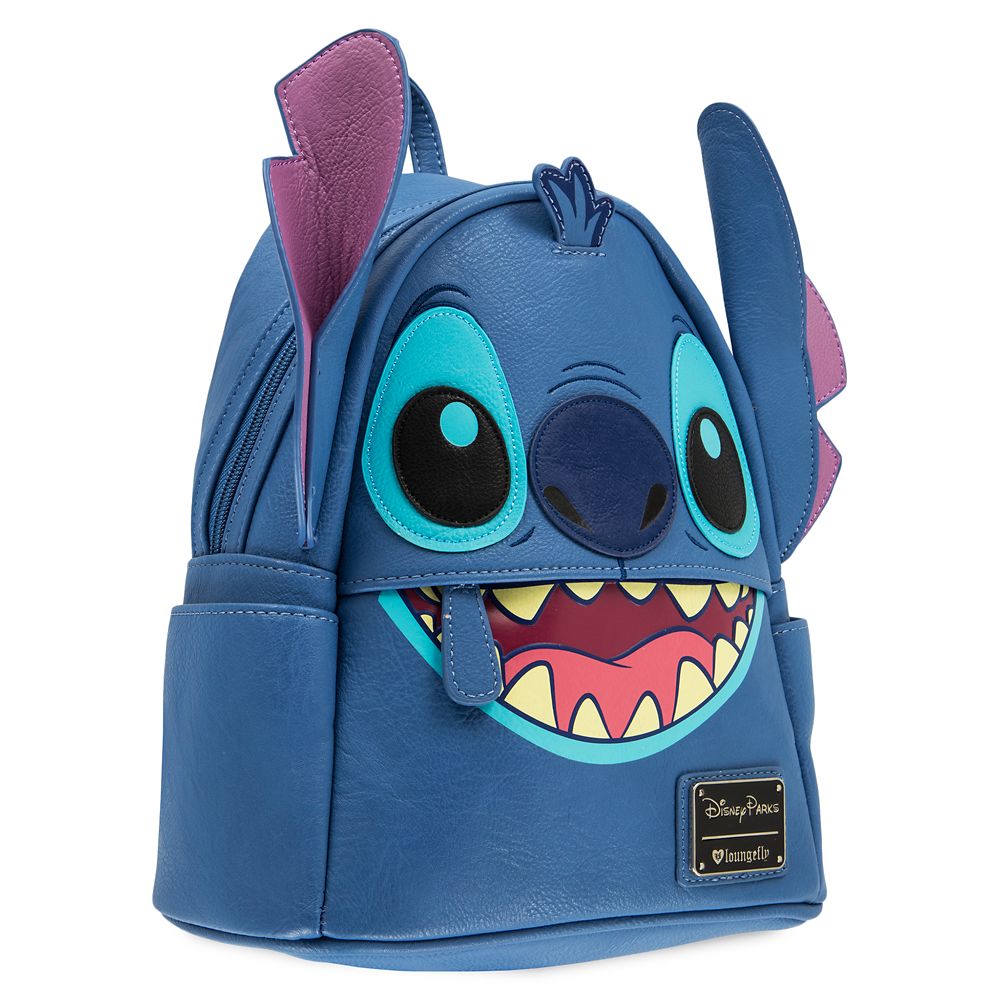
Illustrative Image (Source: Google Search)
-
Labor: Labor costs will depend on the manufacturing location. Countries like Vietnam and Thailand may offer lower labor costs compared to Europe, but the trade-off could be in quality or delivery timelines. Skilled labor is essential for ensuring that stitching and assembly meet quality standards.
-
Manufacturing Overhead: This includes factory operational costs such as utilities, rent, and equipment maintenance. Overhead is usually factored into the per-unit cost, so it’s crucial to understand how a supplier calculates this.
-
Tooling: Initial setup costs for molds, dies, or custom patterns can be significant, particularly for unique designs. These costs are typically amortized over the production run, which means larger orders can help reduce the per-unit tooling cost.
-
Quality Control (QC): Implementing a robust QC process is essential to ensure product standards. Costs associated with inspection, testing, and compliance certifications can add up but are vital for maintaining quality and avoiding costly returns or replacements.
-
Logistics: Shipping costs, including freight, insurance, and handling, can vary widely depending on the shipping method (air vs. sea) and destination. Understanding Incoterms is crucial here, as they dictate who bears the cost and risk at various stages of the shipping process.
-
Margin: Suppliers will typically include a profit margin, which can range from 10% to 30% depending on the market and competition. This margin is influenced by the brand positioning and perceived value of the backpack.
Price Influencers
Several factors can influence the final price of mini stitch backpacks:
-
Volume/MOQ: Minimum order quantities (MOQ) can vary by supplier. Larger orders generally lead to lower per-unit costs, making it economically beneficial for buyers planning to scale.
-
Specifications/Customization: Custom features such as unique designs or specific materials can increase costs. Buyers should balance the desire for customization with the associated price increase.
-
Quality/Certifications: Higher quality materials and adherence to international safety standards (like ISO certifications) can elevate costs but are often necessary for markets with stringent regulations.
-
Supplier Factors: The reputation and capabilities of the supplier can influence pricing. Established suppliers may command higher prices due to their reliability and quality assurance processes.
Buyer Tips
-
Negotiation: Always negotiate prices and terms. Suppliers often have flexibility in pricing, especially for larger orders or long-term partnerships.
-
Cost-Efficiency: Evaluate total cost of ownership rather than just the purchase price. Consider factors such as durability, maintenance, and potential return on investment.
-
Pricing Nuances: Be aware of regional pricing differences. For example, sourcing from Asian countries may yield lower prices, but consider shipping times and costs associated with international logistics.
-
Understanding Incoterms: Familiarize yourself with shipping terms to avoid unexpected costs. Terms like FOB (Free On Board) or CIF (Cost, Insurance, Freight) dictate who pays for what during shipping.
Disclaimer
Prices can fluctuate based on market conditions, material availability, and supplier pricing strategies. It is advisable to conduct thorough market research and obtain multiple quotes to ensure competitive pricing when sourcing mini stitch backpacks.
Spotlight on Potential mini stitch backpack Manufacturers and Suppliers
This section offers a look at a few manufacturers active in the ‘mini stitch backpack’ market. This is a representative sample for illustrative purposes; B2B buyers must conduct their own extensive due diligence before any engagement. Information is synthesized from public sources and general industry knowledge.
Essential Technical Properties and Trade Terminology for mini stitch backpack
Key Technical Properties of the Mini Stitch Backpack
Understanding the essential technical properties of a mini stitch backpack is crucial for B2B buyers to ensure product quality and suitability for their target markets. Here are several critical specifications:
-
Material Grade
The material grade refers to the quality and type of fabric used in the backpack, such as ripstop nylon or polyester. Higher-grade materials offer enhanced durability, resistance to wear, and water repellency, which are essential for longevity, especially in rugged environments. For buyers, selecting the right material grade is vital to meet customer expectations and market demands. -
Stitching Quality
This property includes the type of stitching and the stitch count per inch. A higher stitch count typically indicates stronger seams, which is crucial for durability. For B2B buyers, ensuring high stitching quality can prevent product failures, reduce returns, and enhance brand reputation. -
Weight Tolerance
Weight tolerance defines how much load the backpack can carry without compromising its structure. This is particularly important for outdoor and travel backpacks, which may be subject to heavy usage. Buyers should consider weight tolerance to ensure the product meets specific user needs, such as those of hikers or students. -
Capacity (Volume)
Measured in liters, capacity refers to the amount of space available in the backpack. Understanding volume helps buyers align their offerings with consumer needs, whether for casual use, school, or outdoor activities. A well-defined capacity can also aid in marketing strategies, appealing to target demographics effectively. -
Ergonomic Design
This involves features such as padded straps, back support, and adjustable components. Ergonomic design is crucial for user comfort, especially when the backpack is worn for extended periods. For B2B buyers, highlighting ergonomic properties can differentiate products in competitive markets. -
Water Resistance Rating
This specification indicates the degree to which the backpack can repel water. Ratings such as IPX or hydrostatic head measurements are commonly used. For buyers, understanding water resistance is essential to cater to consumers in wet climates or those engaging in outdoor activities.
Common Trade Terminology in the Backpack Industry
Familiarity with industry jargon can significantly enhance communication and negotiation effectiveness for B2B buyers. Here are some common terms:
-
OEM (Original Equipment Manufacturer)
This term refers to a company that produces parts or products that are then sold by another company under their brand name. Understanding OEM relationships is vital for buyers looking to customize products while leveraging established manufacturing capabilities. -
MOQ (Minimum Order Quantity)
MOQ indicates the smallest quantity of a product that a supplier is willing to sell. This is crucial for buyers to understand as it affects inventory costs and cash flow. Negotiating favorable MOQs can enable startups or smaller businesses to manage their budgets effectively. -
RFQ (Request for Quotation)
An RFQ is a document sent to suppliers requesting pricing and other details for a specific product. For B2B buyers, crafting an effective RFQ ensures they receive comprehensive proposals that facilitate informed decision-making. -
Incoterms (International Commercial Terms)
These are standardized terms used in international trade to define responsibilities for shipping, insurance, and tariffs. Familiarity with Incoterms can help buyers understand the logistics of their transactions and avoid potential disputes regarding delivery responsibilities. -
Lead Time
This refers to the amount of time from placing an order to receiving the product. Understanding lead time is essential for inventory planning and meeting customer demands, especially in fast-paced markets. -
Sourcing
Sourcing involves identifying and engaging suppliers to procure goods. Effective sourcing strategies can lead to cost savings and improved product quality, making it a critical focus for B2B buyers seeking competitive advantages.
By mastering these technical properties and trade terms, international B2B buyers can make informed decisions, foster better supplier relationships, and enhance their overall purchasing strategies in the competitive backpack market.
Navigating Market Dynamics, Sourcing Trends, and Sustainability in the mini stitch backpack Sector
Global drivers influencing the mini stitch backpack market include increasing urbanization, a growing emphasis on sustainability, and rising consumer demand for functional yet stylish accessories. As urban dwellers seek versatile bags for daily commuting, the demand for mini stitch backpacks, which combine compact design with practicality, is surging. Notably, the rise of remote work and hybrid lifestyles has led to an increase in demand for bags suitable for both professional and casual settings.
In terms of B2B tech and sourcing trends, digital platforms are transforming how manufacturers connect with suppliers and buyers. Tools such as virtual sampling, augmented reality (AR) for product visualization, and blockchain for transparency in supply chains are becoming essential. For international buyers, especially in regions like Africa and South America, leveraging these technologies can streamline sourcing processes and enhance collaboration with manufacturers across the globe. Moreover, trade shows and online marketplaces are pivotal for discovering new suppliers and keeping abreast of emerging trends, such as customizable and modular designs, which are increasingly popular in the mini stitch backpack segment.
Sustainability & Ethical Sourcing in B2B
The environmental impact of bag manufacturing is a critical concern for B2B buyers today. The mini stitch backpack sector is no exception, as the production process often involves materials that can contribute to pollution and waste. Ethically sourced materials and sustainable practices are essential for minimizing environmental footprints. Buyers should prioritize manufacturers that utilize recycled or organic materials, as well as those who implement waste-reduction strategies in their production processes.
Establishing ethical supply chains is not only a moral imperative but also a market differentiator. Certifications such as Global Organic Textile Standard (GOTS), OEKO-TEX, and Fair Trade can enhance a brand’s reputation and appeal to eco-conscious consumers. Buyers should actively seek suppliers who provide such certifications, ensuring that their products align with sustainable practices. Additionally, considering local sourcing options can reduce carbon footprints and support regional economies, making it a win-win for businesses and communities alike.
Brief Evolution/History
The mini stitch backpack has evolved significantly from its utilitarian origins to become a staple in modern fashion. Initially designed for functionality, these backpacks now blend style with practicality, catering to a diverse demographic. The rise of streetwear and the influence of social media have further propelled the popularity of mini stitch backpacks, as consumers seek items that reflect their personal style while serving practical purposes. For B2B buyers, understanding this evolution is crucial in selecting designs and materials that resonate with contemporary market demands and consumer preferences.
Related Video: International Trade Explained
Frequently Asked Questions (FAQs) for B2B Buyers of mini stitch backpack
-
What should I consider when vetting suppliers for mini stitch backpacks?
When vetting suppliers, prioritize their experience in producing mini stitch backpacks. Check their production capabilities, quality control processes, and past client reviews. Request samples to evaluate product quality firsthand. Additionally, verify their compliance with international standards and certifications that pertain to textile products, such as ISO or OEKO-TEX, to ensure safety and quality. -
Can I customize mini stitch backpacks to meet my brand’s specifications?
Yes, many manufacturers offer customization options, including materials, colors, and branding elements like logos. It’s essential to communicate your specific requirements clearly during the initial discussions. Be prepared to provide design sketches or prototypes to facilitate the customization process. Ensure the supplier has experience with custom orders to avoid potential pitfalls. -
What are the typical minimum order quantities (MOQ) for mini stitch backpacks?
MOQs can vary significantly by supplier and depend on factors like materials and complexity of design. Generally, for mini stitch backpacks, MOQs can range from 100 to 1,000 units. It’s advisable to discuss your needs with potential suppliers to negotiate MOQs that align with your business objectives, especially if you’re a startup or testing a new market. -
How long does it typically take to produce mini stitch backpacks?
Lead times can vary based on the supplier’s capacity, order size, and customization requirements. On average, production can take anywhere from 4 to 12 weeks. To avoid delays, confirm the timeline during negotiations and factor in additional time for shipping, especially for international orders. Establishing a clear timeline helps in planning your inventory and marketing strategies effectively. -
What quality assurance measures should I expect from suppliers?
A reputable supplier should have robust quality assurance (QA) protocols in place, including regular inspections during production and final quality checks before shipping. Ask about their QA certifications and whether they follow international quality standards. Consider requesting a pre-production sample to evaluate the quality and functionality of the mini stitch backpacks before full-scale production. -
What certifications should I look for when sourcing mini stitch backpacks?
Look for certifications that ensure compliance with safety and environmental standards, such as ISO 9001 for quality management and OEKO-TEX for non-toxic materials. Certifications can also include Fair Trade or ethical manufacturing practices, which are particularly important for buyers in Europe and North America. These certifications not only enhance product credibility but also appeal to environmentally conscious consumers. -
What logistics considerations should I keep in mind when importing mini stitch backpacks?
When importing, consider shipping methods, customs duties, and potential delays. Work with suppliers who have experience in international shipping and can assist with necessary documentation. It’s beneficial to engage a freight forwarder to navigate logistics complexities, especially when shipping to diverse regions like Africa or South America. Ensure you understand the total landed cost, including shipping and tariffs, to avoid budget overruns. -
How should disputes with suppliers be handled?
Establish clear communication channels and a dispute resolution process in your contract with suppliers. Consider including clauses for mediation or arbitration to resolve issues amicably. Document all agreements and communications to support your position if a dispute arises. If necessary, involve legal counsel familiar with international trade laws to navigate complex situations effectively.
Strategic Sourcing Conclusion and Outlook for mini stitch backpack
Strategic sourcing for the mini stitch backpack is pivotal for international B2B buyers looking to enhance their product offerings in competitive markets. By leveraging effective supplier relationships, buyers can ensure access to high-quality materials and innovative designs that resonate with diverse consumer preferences across regions like Africa, South America, the Middle East, and Europe.
Key takeaways include the importance of thorough market research to identify reputable manufacturers and the necessity of clear communication regarding product specifications and quality standards. Establishing a partnership approach with manufacturers not only fosters trust but also facilitates smoother production processes and timely delivery.
As the demand for stylish and functional backpacks continues to rise, international buyers are encouraged to stay ahead of trends by prioritizing sustainable materials and advanced manufacturing techniques. This focus not only aligns with consumer expectations but also positions businesses for future growth.
In conclusion, as the market evolves, now is the time to invest in strategic sourcing practices that will enable your business to thrive. Engage with manufacturers, explore innovative designs, and embrace sustainability to secure a competitive edge in the backpack industry.