Master Sourcing Top-Quality Welding Backpacks for Optimal
Guide to Welding Backpack
- Introduction: Navigating the Global Market for welding backpack
- Understanding welding backpack Types and Variations
- Key Industrial Applications of welding backpack
- Strategic Material Selection Guide for welding backpack
- In-depth Look: Manufacturing Processes and Quality Assurance for welding backpack
- Comprehensive Cost and Pricing Analysis for welding backpack Sourcing
- Spotlight on Potential welding backpack Manufacturers and Suppliers
- Essential Technical Properties and Trade Terminology for welding backpack
- Navigating Market Dynamics, Sourcing Trends, and Sustainability in the welding backpack Sector
- Frequently Asked Questions (FAQs) for B2B Buyers of welding backpack
- Strategic Sourcing Conclusion and Outlook for welding backpack
Introduction: Navigating the Global Market for welding backpack
Navigating the complexities of the global market for welding backpacks can be a daunting task for international B2B buyers, especially those operating in dynamic regions such as Africa, South America, the Middle East, and Europe. As essential gear for welders, these backpacks are designed to provide not only convenience but also safety, ensuring that tools and equipment are securely stored and easily accessible. The significance of a high-quality welding backpack cannot be overstated; it enhances productivity while safeguarding valuable tools from environmental hazards.
This guide serves as a comprehensive resource for buyers seeking to make informed sourcing decisions. It covers a wide array of topics, including the various types of welding backpacks available, the materials best suited for durability and functionality, and the critical manufacturing and quality control processes that ensure product reliability. Additionally, it addresses cost considerations, supplier selection, and prevalent market trends.
By equipping buyers with essential knowledge and actionable insights, this guide empowers stakeholders to navigate the complexities of sourcing welding backpacks effectively. From understanding the unique needs of different welding applications to evaluating supplier capabilities, readers will gain the tools necessary to optimize their purchasing strategies. This ensures that they are not only investing in quality products but also fostering long-term partnerships that can enhance their operational efficiency.
Understanding welding backpack Types and Variations
Type Name | Key Distinguishing Features | Primary B2B Applications | Brief Pros & Cons for Buyers |
---|---|---|---|
Heavy-Duty Welding Backpack | Reinforced stitching, durable materials, extra padding | Industrial welding, construction | Pros: High durability, suitable for heavy gear. Cons: Heavier and bulkier. |
Lightweight Welding Backpack | Compact design, lightweight materials, minimal padding | On-site repairs, mobile welding | Pros: Easy to carry, less fatigue. Cons: May lack protection for heavy tools. |
Multi-Compartment Welding Backpack | Multiple compartments for organization, specialized pockets | Educational institutions, workshops | Pros: Enhanced organization, versatile use. Cons: Can be more complex to manufacture. |
Waterproof Welding Backpack | Water-resistant materials, sealed zippers | Outdoor welding, marine applications | Pros: Protects contents from moisture. Cons: Often pricier due to specialized materials. |
Tactical Welding Backpack | MOLLE webbing, rugged design, customizable features | Military, emergency services | Pros: Highly customizable, durable. Cons: May be over-engineered for casual users. |
Heavy-Duty Welding Backpack
Heavy-duty welding backpacks are designed for industrial applications, featuring reinforced stitching and durable materials such as ballistic nylon. They often include extra padding to protect tools and equipment during transport. Ideal for construction sites and industrial welding environments, these backpacks can withstand harsh conditions. Buyers should consider the weight, as these backpacks can be bulkier, but their durability offers long-term value.
Lightweight Welding Backpack
Lightweight welding backpacks prioritize portability and ease of use, making them suitable for on-site repairs and mobile welding tasks. Constructed from lighter materials, they minimize fatigue during transport. While they are more convenient for daily use, buyers must assess whether the reduced protection for tools meets their operational needs, especially in environments where equipment durability is critical.
Multi-Compartment Welding Backpack
These backpacks feature multiple compartments and specialized pockets for organizing tools, equipment, and personal items. They are particularly useful in educational settings and workshops where organization is key. The versatility of multi-compartment designs allows for tailored storage solutions, but the complexity in manufacturing can lead to higher costs. Buyers should evaluate their specific organizational needs against budget constraints.
Waterproof Welding Backpack
Waterproof welding backpacks are constructed from water-resistant materials and feature sealed zippers to protect tools from moisture. They are ideal for outdoor welding and marine applications, ensuring that equipment remains dry even in adverse weather conditions. While these backpacks offer significant protection, buyers should be prepared for a higher price point due to the specialized materials used in their construction.
Tactical Welding Backpack
Tactical welding backpacks are designed for rugged use, often incorporating MOLLE webbing for customizable attachments. They are favored in military and emergency service applications where durability and adaptability are paramount. While these backpacks provide exceptional functionality and strength, they may be considered over-engineered for casual users. Buyers should assess whether the tactical features align with their specific needs and usage scenarios.
Related Video: Large Language Models (LLMs) – Everything You NEED To Know
Key Industrial Applications of welding backpack
Industry/Sector | Specific Application of Welding Backpack | Value/Benefit for the Business | Key Sourcing Considerations for this Application |
---|---|---|---|
Construction | On-site welding and repair | Improved mobility and efficiency for welders | Durability of materials, weight capacity, and comfort |
Oil & Gas | Maintenance of pipelines and rigs | Facilitates quick repairs in remote locations | Resistance to harsh environments, material compatibility |
Automotive | Bodywork and structural repairs | Enhanced organization of tools and equipment | Customizable compartments, weight distribution |
Manufacturing | Fabrication of metal components | Streamlined workflow and reduced downtime | Size and accessibility of pockets, ease of transport |
Shipbuilding | Welding and assembly of ship components | Increased productivity and safety for welders | Water resistance, heavy-duty materials, and ergonomic design |
Construction
In the construction industry, welding backpacks are invaluable for on-site welding and repair tasks. They allow welders to transport essential tools and materials efficiently, enhancing mobility and reducing downtime. Buyers in this sector should prioritize durability and comfort, as construction sites often involve rugged environments. Materials that withstand wear and tear while remaining lightweight are crucial for the effective use of welding backpacks in this context.
Oil & Gas
For the oil and gas sector, welding backpacks are essential for the maintenance of pipelines and rigs, often located in remote and challenging environments. These backpacks enable quick repairs and maintenance work, minimizing operational disruptions. International buyers should consider the backpacks’ resistance to harsh conditions, such as extreme temperatures and exposure to chemicals. Ensuring that materials are compatible with the specific media handled in this industry is also vital for operational safety.
Automotive
In the automotive industry, welding backpacks facilitate bodywork and structural repairs by providing welders with organized access to their tools and equipment. This organization helps reduce time spent searching for tools, thereby increasing productivity. Buyers should look for customizable compartments that cater to different tools and equipment sizes, as well as features that ensure proper weight distribution, making it easier to carry heavy loads without discomfort.
Manufacturing
Welding backpacks play a critical role in the manufacturing sector, particularly in the fabrication of metal components. They streamline workflow by allowing welders to carry necessary equipment and supplies directly to their workstations, thus reducing downtime. When sourcing, buyers should consider the size and accessibility of pockets, as well as the overall ease of transport. The ability to configure the backpack to individual needs can significantly enhance operational efficiency.
Shipbuilding
In shipbuilding, welding backpacks are used for welding and assembly of various ship components, which requires a high degree of precision and safety. These backpacks enhance productivity by keeping tools readily available and organized, allowing welders to focus on their tasks. Buyers should ensure that the backpacks are constructed from water-resistant and heavy-duty materials to withstand the marine environment. Ergonomic design is also crucial to support the physical demands of shipbuilding tasks.
Related Video: How a Backpack is Made : Every Step on the Production Line
Strategic Material Selection Guide for welding backpack
When selecting materials for welding backpacks, it is crucial to consider their specific properties and suitability for the intended applications. This guide analyzes several common materials used in the manufacturing of welding backpacks, focusing on their key properties, advantages, disadvantages, and implications for international B2B buyers.
1. Nylon
Key Properties:
Nylon is known for its high tensile strength and resistance to abrasion, making it an excellent choice for welding backpacks that undergo rigorous use. It typically has a melting point of around 220°C (428°F), which is suitable for environments where heat exposure is a concern.
Pros & Cons:
Nylon is lightweight, durable, and water-resistant, which enhances the usability of the backpack in various conditions. However, it can be more expensive than other materials and may require specialized manufacturing techniques to ensure heat resistance.
Impact on Application:
Nylon’s heat resistance makes it compatible with welding applications where sparks and spatter are common. It is also suitable for carrying welding tools and accessories due to its strength.
Considerations for International Buyers:
Buyers in regions such as Africa and the Middle East should ensure that the nylon used complies with local standards for flame resistance and durability. Familiarity with ASTM and ISO standards can facilitate compliance and quality assurance.
2. Polyester
Key Properties:
Polyester offers good resistance to UV rays, moisture, and abrasion, with a melting point of approximately 250°C (482°F). This makes it a versatile choice for outdoor and industrial applications.
Pros & Cons:
The material is cost-effective and relatively easy to manufacture, making it a popular choice for budget-conscious buyers. However, polyester is less durable than nylon and may not perform as well under extreme heat.
Impact on Application:
Polyester’s properties make it suitable for welding backpacks that are used in less demanding environments. It can effectively protect tools from moisture and UV damage but may not withstand high temperatures as well as nylon.
Considerations for International Buyers:
In Europe, compliance with EN standards for safety and durability is essential. Buyers should also consider the environmental impact of polyester production and seek suppliers that prioritize sustainable practices.
3. Canvas
Key Properties:
Canvas is a heavy-duty fabric that is typically made from cotton or a cotton-polyester blend. It is known for its durability and resistance to wear and tear, with a melting point that varies based on the specific blend used.
Pros & Cons:
Canvas is extremely durable and provides a classic aesthetic, making it a preferred choice for heavy-duty applications. However, it is heavier than nylon and polyester, which may affect the overall weight of the backpack.
Impact on Application:
Canvas is suitable for welding backpacks that require robust protection for tools and equipment. Its thickness offers excellent abrasion resistance, but it may not be as water-resistant unless treated.
Considerations for International Buyers:
Buyers should be aware of local regulations regarding the use of natural fibers and their fire resistance. In regions like South America, sourcing canvas that meets local agricultural and environmental standards can be beneficial.
4. Ballistic Nylon
Key Properties:
Ballistic nylon is a type of nylon that is specifically designed to resist abrasion and impact. It has a high melting point, typically around 300°C (572°F), making it ideal for high-heat applications.
Pros & Cons:
This material is exceptionally durable and resistant to tearing, which makes it suitable for heavy-duty welding backpacks. However, it is more expensive and may require more complex manufacturing processes.
Impact on Application:
Ballistic nylon is ideal for welding backpacks used in high-risk environments where maximum protection is necessary. Its superior strength ensures that tools and equipment are well-protected from damage.
Considerations for International Buyers:
Buyers should ensure that ballistic nylon products comply with international safety standards. In the Middle East, understanding local regulations regarding materials used in industrial applications is essential for compliance.
Summary Table
Material | Typical Use Case for welding backpack | Key Advantage | Key Disadvantage/Limitation | Relative Cost (Low/Med/High) |
---|---|---|---|---|
Nylon | High-temperature welding environments | Lightweight, durable, water-resistant | Higher cost, specialized manufacturing | High |
Polyester | General use in moderate environments | Cost-effective, UV resistant | Less durable under extreme heat | Medium |
Canvas | Heavy-duty applications | Extremely durable, classic aesthetic | Heavier, may require treatment for water resistance | Medium |
Ballistic Nylon | High-risk industrial applications | Superior durability and tear resistance | High cost, complex manufacturing | High |
This guide provides a comprehensive overview of material options for welding backpacks, enabling international B2B buyers to make informed decisions based on their specific needs and compliance requirements.
In-depth Look: Manufacturing Processes and Quality Assurance for welding backpack
Manufacturing Processes for Welding Backpacks
The manufacturing of welding backpacks requires a meticulous approach to ensure durability, functionality, and safety. Below is a detailed overview of the main stages in the manufacturing process, along with key techniques employed throughout.
Main Stages of Manufacturing
-
Material Preparation
– Material Selection: High-quality materials are essential for welding backpacks. Common choices include heavy-duty nylon, polyester, and specialized heat-resistant fabrics. For added durability and water resistance, manufacturers may opt for ballistic nylon or coated fabrics.
– Cutting: Materials are cut into various shapes and sizes according to the design specifications. Precision cutting ensures that all components fit together seamlessly during assembly. -
Forming
– Shaping Components: This stage involves the creation of structural elements such as pockets, straps, and reinforcement areas. Techniques such as heat molding may be employed to give the backpack its final shape, particularly around areas requiring additional rigidity.
– Sewing: The cut pieces are sewn together using heavy-duty stitching methods. Reinforcement stitching is particularly important in stress points, such as where straps attach to the main body of the backpack.
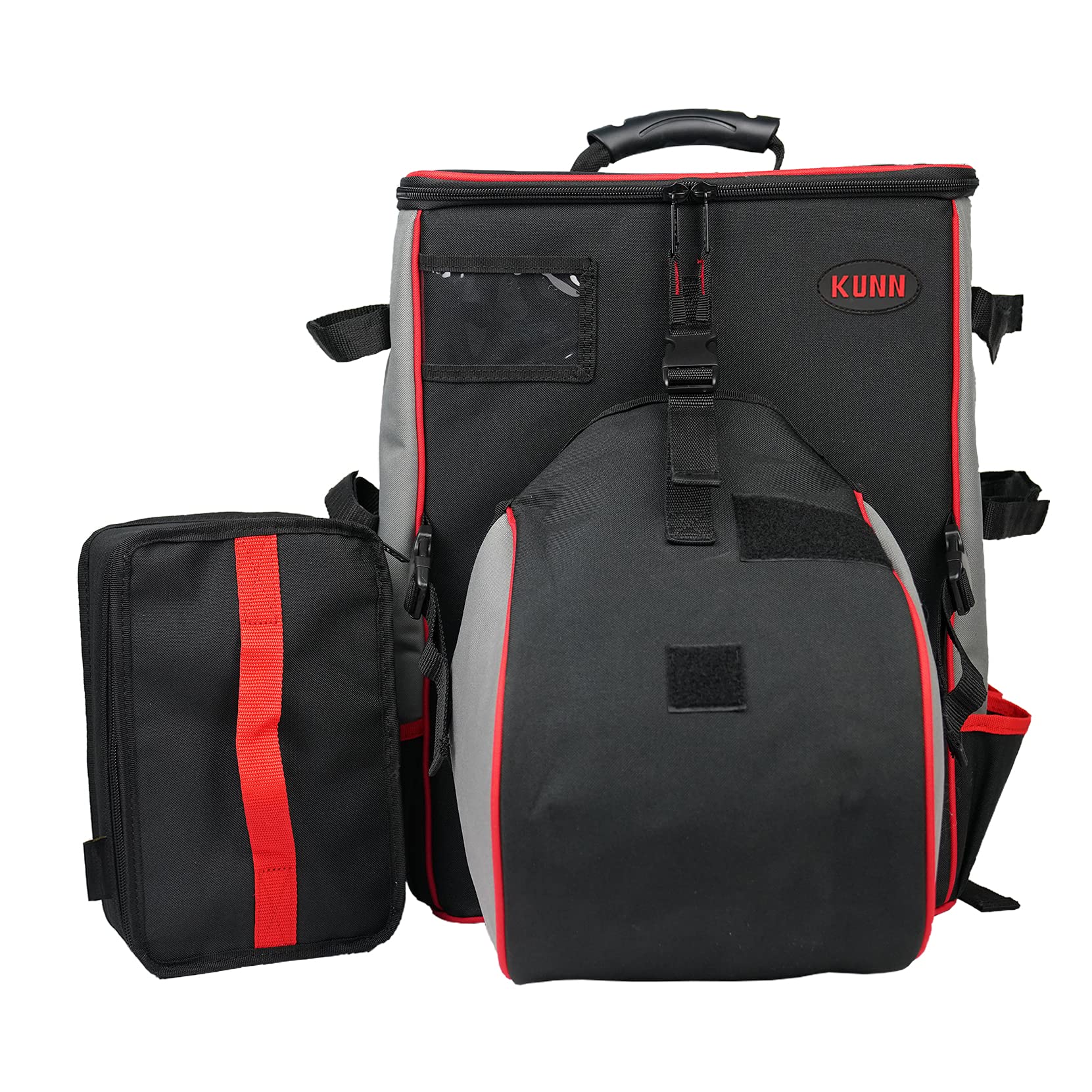
Illustrative Image (Source: Google Search)
-
Assembly
– Component Integration: This involves combining all the elements, including zippers, buckles, and any additional accessories. Manufacturers may utilize automated sewing machines for efficiency, while also ensuring that skilled workers oversee critical assembly tasks.
– Waterproofing: Many welding backpacks require waterproof seams. Techniques such as heat sealing or the application of waterproof coatings are commonly used to prevent moisture ingress. -
Finishing
– Final Touches: After assembly, backpacks undergo a finishing process where they are inspected for visual defects, and branding elements like logos are added. This may involve screen printing, embroidery, or heat transfer methods.
– Packaging: Finally, the backpacks are carefully packaged for shipment, ensuring that they are protected from damage during transportation.
Quality Assurance in Welding Backpack Manufacturing
Quality assurance (QA) is a critical component of the manufacturing process, ensuring that welding backpacks meet both safety standards and customer expectations. Below are key aspects of QA relevant to international B2B buyers.
International and Industry-Specific Standards
-
ISO 9001: This international standard focuses on quality management systems. Compliance with ISO 9001 demonstrates a manufacturer’s commitment to quality and continuous improvement.
-
CE Marking: In Europe, CE marking indicates that a product meets EU safety, health, and environmental protection standards. For welding backpacks, this is especially important to ensure compliance with safety regulations.
-
API Standards: For welding backpacks used in industrial settings, adherence to API standards can be crucial, particularly if the backpacks are intended for use in oil and gas or other high-risk industries.
QC Checkpoints
-
Incoming Quality Control (IQC): Upon receiving raw materials, manufacturers conduct IQC to ensure that all materials meet specified quality criteria. This includes checking for defects, material composition, and compliance with safety standards.
-
In-Process Quality Control (IPQC): During the manufacturing process, IPQC checkpoints are established to monitor the production at various stages. This helps identify any issues early on, allowing for timely corrections.
-
Final Quality Control (FQC): After assembly, a thorough inspection is performed before packaging. This includes checking for stitching integrity, functionality of zippers, and overall aesthetic quality.
Common Testing Methods
- Durability Tests: These tests simulate wear and tear to ensure that the backpack can withstand the rigors of daily use, particularly in challenging environments.
- Water Resistance Tests: Assessing the waterproof capabilities of the materials and seams is crucial, especially for welding backpacks exposed to moisture.
- Safety Compliance Testing: This may involve checking materials for harmful substances, ensuring they meet regulatory requirements for safety.
Verifying Supplier QC
B2B buyers can take several steps to verify the quality assurance processes of potential suppliers:
-
Supplier Audits: Conducting on-site audits can provide insights into a manufacturer’s QC processes, production capabilities, and adherence to standards.
-
Quality Reports: Requesting detailed quality reports can help buyers understand the manufacturing process, including defect rates and improvements made over time.
-
Third-Party Inspections: Engaging third-party inspection services can add an extra layer of assurance, ensuring that the products meet specified quality standards before shipment.
QC and Certification Nuances for International B2B Buyers
- Cultural Considerations: Buyers from Africa, South America, the Middle East, and Europe may encounter different practices and expectations regarding quality assurance. Understanding these cultural nuances can aid in effective communication with suppliers.
- Regulatory Compliance: Buyers must be aware of local regulations that may affect the importation and use of welding backpacks. This includes understanding any specific certifications required in their home markets.
- Sustainability Practices: Increasingly, buyers are looking for manufacturers that prioritize sustainable practices. Suppliers who employ eco-friendly materials and processes may have a competitive advantage.
In summary, understanding the manufacturing processes and quality assurance measures for welding backpacks is crucial for international B2B buyers. By focusing on material selection, production techniques, and stringent quality controls, buyers can ensure they procure high-quality products that meet their operational needs.
Comprehensive Cost and Pricing Analysis for welding backpack Sourcing
When sourcing welding backpacks for international markets, understanding the comprehensive cost structure and pricing dynamics is crucial for B2B buyers. The costs associated with these specialized backpacks can be broken down into several key components, each influenced by various factors that buyers should consider.
Cost Components
-
Materials: The choice of materials significantly impacts the overall cost. High-quality fabrics such as ballistic nylon or heavy-duty polyester, which offer durability and water resistance, may increase the price. Additionally, specialized features like reinforced stitching or waterproof zippers can also elevate material costs.
-
Labor: Labor costs vary significantly depending on the manufacturing location. Countries with lower labor costs may offer competitive pricing, but this can come at the expense of quality. Buyers should consider the skill level required for the assembly of welding backpacks, as skilled labor may demand higher wages.
-
Manufacturing Overhead: This includes expenses related to the factory’s operational costs such as utilities, rent, and equipment maintenance. Efficient manufacturers may pass on lower overhead costs to buyers, making it an essential factor to evaluate.
-
Tooling: If custom tooling or molds are required for specific designs, this can add to the initial investment. Buyers should factor in these costs, especially if they are ordering unique designs or large quantities.
-
Quality Control (QC): Implementing a robust QC process ensures that the final product meets industry standards. However, stringent QC measures can increase production costs. Buyers should inquire about the QC processes of potential suppliers to understand their implications on pricing.
-
Logistics: Shipping and handling costs vary based on the origin of production, destination, and chosen Incoterms. For instance, DDP (Delivered Duty Paid) terms may include higher costs due to customs duties and taxes, which should be considered in the total cost calculation.
-
Margin: Suppliers will typically add a profit margin to their costs. This margin can vary based on the supplier’s brand reputation, market demand, and the complexity of the product.
Price Influencers
Several factors can influence the final price of welding backpacks:
-
Volume/MOQ: Higher order volumes can lead to lower per-unit prices due to economies of scale. Buyers should negotiate minimum order quantities (MOQ) that align with their budget and demand.
-
Specifications and Customization: Custom features or specifications will often increase costs. Buyers should clearly define their needs to avoid unexpected expenses.
-
Quality and Certifications: Products that meet specific industry standards or certifications (e.g., ISO, CE) may carry higher price tags but can ensure reliability and safety, which is crucial for welding applications.
-
Supplier Factors: The supplier’s reputation, reliability, and previous experience in manufacturing welding backpacks can impact pricing. Established suppliers may charge a premium but often provide better quality assurance.
Buyer Tips
For international B2B buyers, especially from regions like Africa, South America, the Middle East, and Europe, consider the following tips:
-
Negotiation: Always negotiate pricing and terms. Many suppliers expect some level of negotiation, especially for larger orders.
-
Cost-Efficiency: Evaluate total cost of ownership (TCO) rather than just the purchase price. Consider durability, potential repair costs, and replacement frequency.
-
Pricing Nuances: Be aware of currency fluctuations, import tariffs, and local market conditions that can affect pricing. Engaging in forward contracts for currency can mitigate some of these risks.
-
Understand Incoterms: Familiarize yourself with shipping terms to avoid unexpected costs. Selecting the right Incoterms can significantly impact the total landed cost of the product.
Disclaimer
Prices for welding backpacks can vary widely based on the aforementioned factors. The insights provided here are intended as a guideline; actual costs may differ based on specific supplier negotiations and market conditions. Always obtain multiple quotes and assess them against your needs and budget.
Spotlight on Potential welding backpack Manufacturers and Suppliers
This section offers a look at a few manufacturers active in the ‘welding backpack’ market. This is a representative sample for illustrative purposes; B2B buyers must conduct their own extensive due diligence before any engagement. Information is synthesized from public sources and general industry knowledge.
Essential Technical Properties and Trade Terminology for welding backpack
When sourcing a welding backpack for industrial applications, understanding the essential technical properties and trade terminology is crucial. This knowledge ensures that B2B buyers can make informed decisions, especially when navigating international markets across Africa, South America, the Middle East, and Europe.
Key Technical Properties of Welding Backpacks
-
Material Grade
– Definition: The quality and type of materials used in the manufacturing of the backpack, such as ballistic nylon, polyester, or canvas.
– Importance: High-grade materials enhance durability and resistance to wear and tear, making them suitable for the demanding environments where welding tools are utilized. -
Weight Capacity
– Definition: The maximum weight that the backpack can safely carry, often specified in kilograms or pounds.
– Importance: This is critical for ensuring that the backpack can accommodate the tools and equipment required for welding tasks without compromising comfort or safety. -
Water Resistance
– Definition: The ability of the backpack to repel water, often measured in millimeters of water column (e.g., 1000mm, 2000mm).
– Importance: Welding environments can be unpredictable, and a water-resistant backpack protects sensitive equipment from moisture, thus prolonging their lifespan. -
Zipper Quality
– Definition: The type and robustness of zippers used, including features like corrosion resistance and ease of use.
– Importance: High-quality zippers prevent failures during operation, ensuring that tools remain secure and accessible, which is vital in fast-paced work settings. -
Tolerances and Dimensions
– Definition: Specifications regarding the size and fit of the backpack, including height, width, depth, and tolerances in construction.
– Importance: Precise dimensions ensure compatibility with specific welding gear and ergonomic design for user comfort during extended use.
Common Trade Terminology
-
OEM (Original Equipment Manufacturer)
– Definition: A company that produces parts and equipment that may be marketed by another manufacturer.
– Relevance: Understanding OEM relationships can help buyers identify reputable suppliers and ensure they are sourcing from manufacturers who adhere to quality standards. -
MOQ (Minimum Order Quantity)
– Definition: The smallest number of units that a supplier is willing to sell.
– Relevance: Knowing the MOQ is essential for budgeting and inventory management. It can also impact the negotiation process when sourcing products for resale or corporate use. -
RFQ (Request for Quotation)
– Definition: A document issued by a buyer to solicit price quotations from suppliers for specific products or services.
– Relevance: An RFQ helps streamline the procurement process, allowing B2B buyers to compare prices and terms from different suppliers effectively. -
Incoterms (International Commercial Terms)
– Definition: A set of predefined international trade terms published by the International Chamber of Commerce (ICC) that clarify the responsibilities of buyers and sellers.
– Relevance: Familiarity with Incoterms is crucial for international transactions, as they define who is responsible for shipping, insurance, and tariffs, thereby reducing potential disputes. -
Lead Time
– Definition: The time taken from placing an order to the delivery of the product.
– Relevance: Understanding lead times is vital for planning and ensuring that welding backpacks are available when needed, especially in urgent project scenarios. -
Quality Assurance (QA)
– Definition: A systematic process of ensuring that products meet specified quality standards before reaching the customer.
– Relevance: QA practices are critical in manufacturing, particularly for welding backpacks that must withstand rigorous use. Buyers should inquire about a manufacturer’s QA processes to ensure product reliability.
By grasping these technical properties and trade terms, B2B buyers can navigate the complexities of sourcing welding backpacks more effectively, ensuring they select products that meet their operational needs and quality expectations.
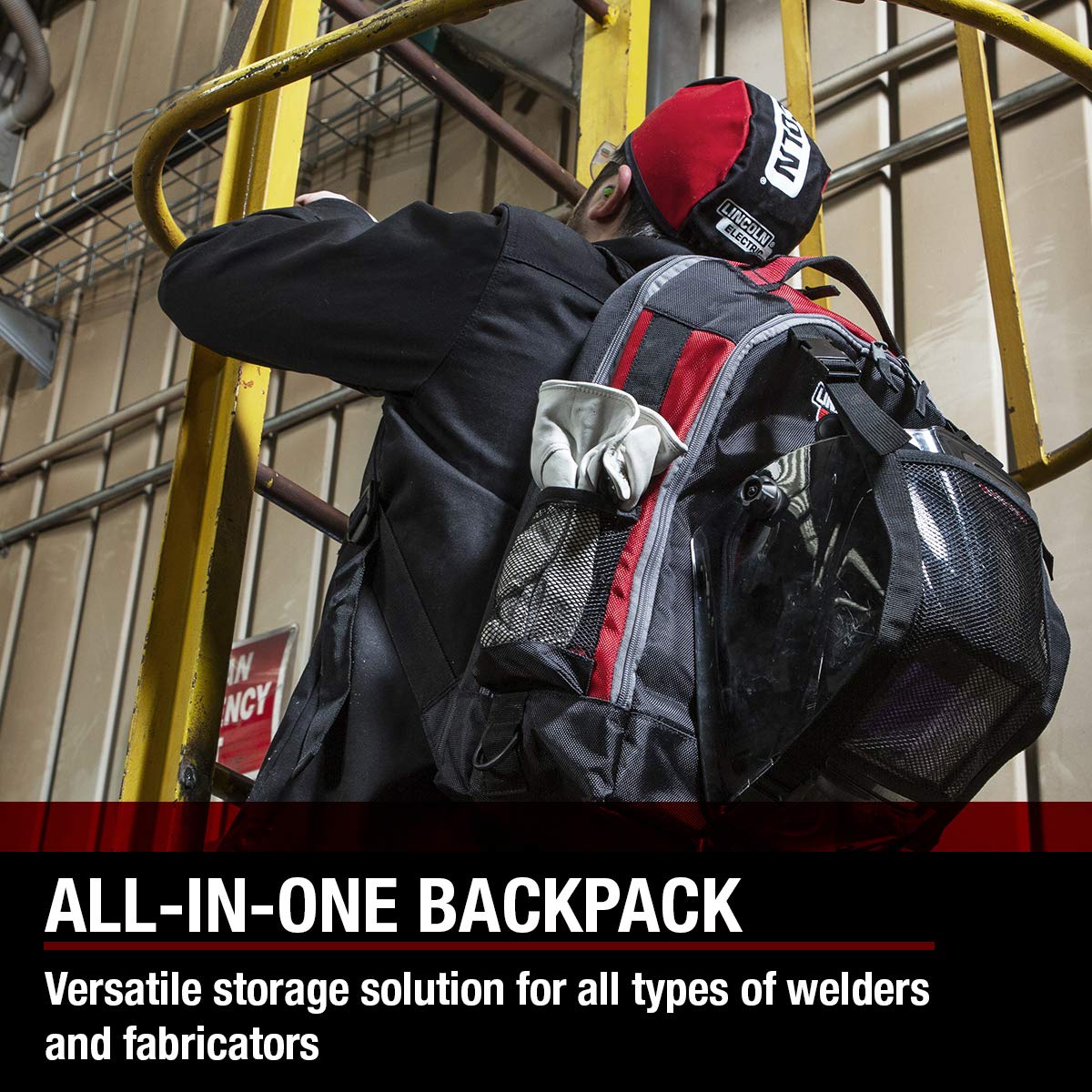
Illustrative Image (Source: Google Search)
Navigating Market Dynamics, Sourcing Trends, and Sustainability in the welding backpack Sector
Market Overview & Key Trends
The welding backpack sector is experiencing significant growth driven by increasing demand for portable and efficient storage solutions among professionals in various industries, including construction, manufacturing, and maintenance. Key trends shaping this market include the integration of advanced materials and innovative designs that enhance functionality. For instance, the use of lightweight, durable fabrics such as ballistic nylon and reinforced stitching has become a standard, ensuring that welding backpacks can withstand the rigors of industrial environments.
Emerging technologies, such as 3D printing, are revolutionizing the manufacturing process, allowing for customized designs tailored to specific user needs. Moreover, the rise of e-commerce platforms has simplified the sourcing process, enabling international buyers from Africa, South America, the Middle East, and Europe to access a broader range of products. However, this also necessitates a thorough understanding of local regulations and standards, particularly regarding safety and quality certifications.
For B2B buyers, it is crucial to stay informed about regional market dynamics. In Europe, for example, there is a growing emphasis on compliance with strict safety regulations, while in the Middle East, rapid urbanization is driving demand for high-quality welding equipment, including backpacks. Buyers should leverage data analytics to assess market trends and consumer preferences, ensuring that their sourcing strategies align with the evolving landscape.
Sustainability & Ethical Sourcing in B2B
Sustainability is becoming increasingly important in the welding backpack sector, with environmental impacts prompting manufacturers and buyers to adopt more responsible practices. The production of welding backpacks often involves materials that can have significant ecological footprints, making it essential for companies to prioritize ethical sourcing and sustainable practices.
International B2B buyers should seek suppliers that utilize eco-friendly materials, such as recycled PET or organic cotton, which reduce waste and promote sustainability. Certifications such as Global Organic Textile Standard (GOTS) and OEKO-TEX® Standard 100 can serve as benchmarks for evaluating the environmental impact of materials used in welding backpacks. Additionally, transparent supply chains that ensure fair labor practices are crucial for maintaining ethical standards.
Investing in sustainable products not only enhances brand reputation but also appeals to an increasingly eco-conscious consumer base. Buyers can differentiate themselves in the marketplace by partnering with manufacturers committed to reducing their carbon footprint and employing sustainable manufacturing processes. This alignment with sustainability can also lead to potential cost savings through waste reduction and efficiency improvements.
Brief Evolution/History
The evolution of the welding backpack can be traced back to the growing need for portable solutions in industrial sectors. Initially, traditional tool bags were used, which lacked the ergonomic designs and specialized compartments required by welders. Over the years, manufacturers began to recognize the importance of functionality and durability, leading to the development of backpacks specifically tailored for welding professionals.
These modern welding backpacks now incorporate features such as heat-resistant materials, padded straps for comfort, and multiple compartments for organizing tools and protective gear. The shift towards lightweight yet durable materials has further enhanced their usability, making them essential for professionals who require mobility without compromising on equipment safety. As the industry continues to innovate, the welding backpack is expected to evolve further, integrating smart technology and advanced materials to meet the demands of future users.
Related Video: International Trade Explained
Frequently Asked Questions (FAQs) for B2B Buyers of welding backpack
-
How can I effectively vet suppliers for welding backpacks?
To vet suppliers, start by checking their business credentials, including registration and certifications. Request references from previous clients and assess their manufacturing capabilities through site visits or virtual tours. Use platforms like Alibaba or Global Sources to read reviews and ratings. It’s also beneficial to verify compliance with international standards, such as ISO certifications, which ensure quality and reliability in production processes. -
What customization options are available for welding backpacks?
Most manufacturers offer a variety of customization options, including size, color, material, and additional features like compartments for welding tools or protective gear. When discussing customization, provide detailed specifications and any unique branding requirements, such as logos. Be prepared to collaborate closely with the supplier during the design phase to ensure that the final product aligns with your specific needs. -
What are the typical minimum order quantities (MOQs) and lead times?
MOQs for welding backpacks can vary significantly based on the supplier and the complexity of the design. Generally, MOQs can range from 100 to 500 units. Lead times typically range from 30 to 90 days, depending on production schedules and material availability. Always confirm these details upfront to avoid delays and ensure that your purchasing plans align with your project timelines. -
What payment methods are commonly accepted by suppliers?
Suppliers often accept various payment methods, including bank transfers (T/T), letters of credit (L/C), and online payment platforms like PayPal or Escrow services. It’s essential to negotiate payment terms that protect your interests, such as a deposit upfront and the balance upon delivery. Ensure clarity in terms of currency, as international transactions may incur additional fees due to currency exchange rates. -
How can I ensure quality assurance and certifications for my welding backpacks?
To ensure quality, request that your supplier provide certifications, such as ISO 9001, which indicates a commitment to quality management systems. Implement a quality control plan that includes pre-production samples and in-line inspections during manufacturing. Consider conducting final inspections before shipment, possibly through third-party services, to verify that the products meet your specifications and standards. -
What logistics considerations should I keep in mind when sourcing welding backpacks?
Logistics are crucial when importing welding backpacks. Discuss shipping options with your supplier, including freight forwarding services, to determine the most cost-effective methods. Understand the import regulations and tariffs in your country, as these can impact overall costs. Ensure that your supplier provides the necessary documentation for customs clearance, such as invoices and packing lists, to avoid delays. -
What steps should I take if a dispute arises with my supplier?
In the event of a dispute, maintain clear communication with your supplier to resolve issues amicably. Reference the purchase agreement to clarify terms and obligations. If necessary, consider mediation or arbitration as a means of resolution. It’s advisable to document all correspondence and agreements to support your case. Establishing a good relationship upfront can also facilitate easier conflict resolution. -
Are there any specific certifications or standards welding backpacks should comply with?
Welding backpacks should ideally comply with safety and quality standards pertinent to the welding industry. Look for certifications such as EN 340 (general requirements for work clothing) or any local regulations relevant to safety gear. Ensure that the materials used are flame-resistant and durable, as these features are crucial for protecting users in welding environments. Discuss these requirements with your supplier to ensure compliance during the production process.
Strategic Sourcing Conclusion and Outlook for welding backpack
In conclusion, strategic sourcing is essential for international B2B buyers seeking high-quality welding backpacks tailored to their specific needs. By understanding the manufacturing process—from design and material selection to quality control—buyers can make informed decisions that lead to better product outcomes and long-term partnerships. Emphasizing durable materials such as nylon and polyester, as well as sustainable practices, will not only enhance product quality but also align with the growing consumer demand for eco-friendly solutions.
Key Takeaways:
– Focus on Quality: Prioritize manufacturers with a proven track record in quality control and durable material selection.
– Understand Regional Needs: Different markets, such as those in Africa, South America, the Middle East, and Europe, may have unique requirements for functionality and design.
– Leverage Technology: Utilize platforms that provide transparent pricing and reliable supplier information to mitigate risks associated with sourcing.
As the demand for specialized welding backpacks continues to rise, now is the time to refine your sourcing strategies. Engage with reputable suppliers who understand your market and can meet your specific requirements. By doing so, you position your business for success in an increasingly competitive landscape.
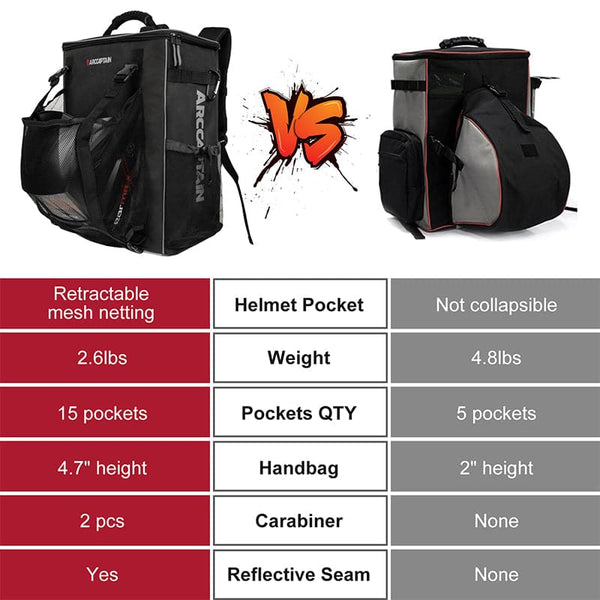
Illustrative Image (Source: Google Search)